Plastics are versatile materials with plenty of polymer options. They are among the most common materials used in producing end-use products, ranging from consumer products to medical materials. Plastic fabrication is a crucial part of the plastic industry, and it has for many years.
It involves designing, manufacturing, and assembling plastic products through different methods. There are many plastic processing techniques. The various options make it difficult to choose the best for individual application.
This article will guide you through the widely used plastic fabrication processes. It’ll help you understand the factors to consider to help you choose the best plastic manufacturing process. Let’s get straight to it!
Different Plastic Fabrication Processes
A wide variety of plastic manufacturing processes have developed over the years—the different methods aimed at covering several applications, plastic types, and part geometrics.
Therefore, it becomes crucial for every person involved in product development to get familiar with the options available. Below, you’ll find the most common plastic forming techniques.
Injection Molding
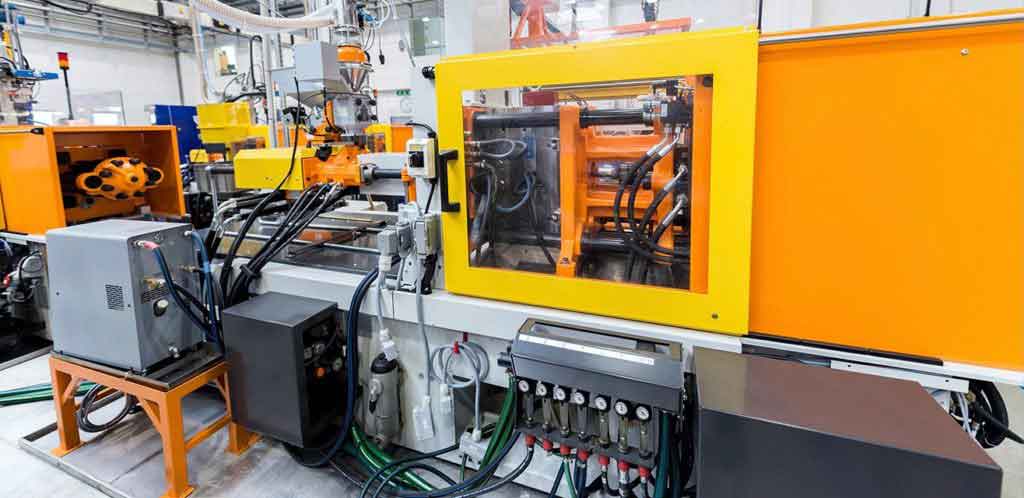
This method is one of the most common plastic processing techniques. This process involves the melting of plastic pellets, which could be thermosetting or thermostatic polymers.
The next process involves injection of the melted plastic pellets into a mold cavity at pressure once they are malleable enough. Injection into the mold cavity fills and solidifies the plastic to make the final product.
Plastic injection molding is a standard method in any plastic fabrication company. It may involve an aluminum mold or a steel mold.
The most commonly used mold is the aluminum variant. It transfers heat more efficiently than steel mold. Therefore, it does not need the use of cooling channels.
The first step in this process is the loading of plastic pellets into barrels or similar containers. Here, the melting and compression of the mold occur. Then, shooting of the melted hot pellets into a mold cavity occurs. The method may require ejector pins to remove the molded parts from the mold and have them boxed.
Injection molding helps to produce parts in large quantities. Its typical application is in mass-production processes where there’s a need to create the same part thousands of times in succession.
Vacuum Casting
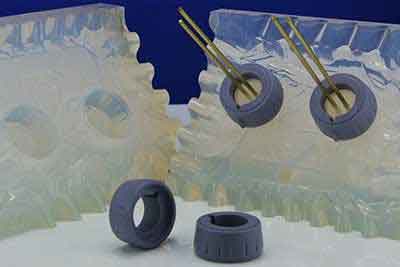
When you need a cost-effective alternative to the injection molding technique, then vacuum casting is a perfect choice. It is a form of ‘copying’ technique for custom plastic fabrication.
Vacuum casting involves producing a small series of functional plastic parts or prototypes. Therefore, there’s a need for a master model with a high-quality surface finish for an efficient vacuum casting process. Most manufacturers use Laser Sintering or Stereolithography to create the master model. Then, the next step involves the encapsulation of the master model into a silicone mold.
Curing of the silicone mold occurs at high temperatures, ensuring strength and durability. After curing, the mold is cut open, revealing a hollow space with the same dimensions as the master model.
The cut mold is then filled with the designated resin material in a vacuum chamber. Many manufacturers often mix the resin with coloring pigment or metallic powder. Therefore, you can be sure of achieving aesthetic or certain functional characteristics. The resin’s final curing occurs in the oven at high temperatures, after which there’s the removal of the silicone mold.
Using the Vacuum casting plastic forming process ensures high precision final product. Even if there’s complex geometry, the finished product looks exactly like the original. Also, vacuum casting is more cost-effective due to the affordable nature of silicone. Moreover, you can make several other products from an already used mold.
Blow Molding
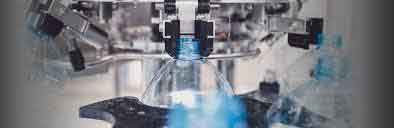
Here’s another popular method involved in plastic fabrication. It involves the inflation of heated plastic tubes to create hollow plastic parts. The raw material in blow molding are thermoplastic pellets, which could include any of the following:
- Low-Density Polyethylene (LDPE)
- High-Density Polyethylene (HDPE)
- Polypropylene (PP)
- Polyethylene Terephthalate (PET)
- Polyvinyl Chloride (PVC)
- Co-polyester
- Polystyrene
The thermoplastic pellets are first melted into a hollow tube – known as the parison. There are various methods of forming the parison. They include
- Extrusion Blow Molding. In this case, a rotating screw helps to force the melted plastic through a die head, forming the parison in a blow pin. The next step then involves the extrusion of the parison between two open molds. The parison inflates by blowing pressurized air through the blow pin.
- Injection Blow Molding. The injection molding process is used to form a hollow parison. The manufacturer then transfers the core and parison into the blow mold and clamped securely. Also, pressurized air inflates the parison when the core opens. This method is best for smaller applications.
- Stretch Mold Molding. The parison in the stretch molding process also forms the same way as injection blow molding. Once the manufacturer transfers the parison to the blow mold, heating and stretch of the core occur before inflation. The stretching helps to give the plastic more strength. Parts created from this custom plastic fabrication are durable and can withstand internal pressure.
Thermoforming
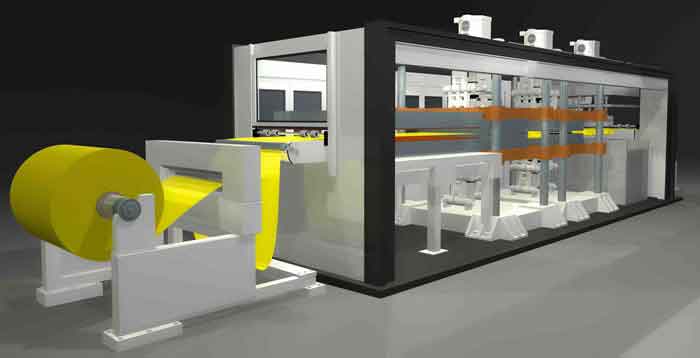
This is a unique process involving the heating of thermoplastic to a pliable temperature. The heated thermoplastic can then be formed into a specific shape in the mold. After then, it will be trimmed to create the final product.
Thermoforming can use different mold types and processes to get the finished parts. It could involve the bending of plastic sheets on strip heaters. Also, molding of complex plastics occurs via the vacuum forming method.
Thermoformed parts usually have lower tooling costs. This is because the instrument do not need to operate at very high temperatures and pressures. Thermoforming is an efficient and versatile process that helps to create plastic parts ranging from disposable cups to medicinal equipment and more.
Choosing the Right Plastic Fabrication Process
Before you select a plastic manufacturing process for your product, it’s best to consider the following factors:
Form
Different plastic parts have different features and tolerance requirements. It will be best if you consider these factors before choosing a plastic fabrication process. The manufacturing processes may depend on the design’s geometry. It may also require the optimization of design for manufacturing (DFM). This ensures a more economical production.
Material
What strains or extreme conditions will your product have to withstand? Choosing a material for your applications needs you to consider some factors. Hence, need to consider aesthetic and functional requirements and balance them with the cost. Compare the ideal features of your applications and contrast them with the manufacturing processes available.
Cost/Volume
The total volume of the parts you wish to manufacture is very important. Some processes have additional costs for setup and tooling. However, they produce inexpensive parts on a per-part basis. On the other hand, some low volume processes have lower setup costs with constant cost per part. This is a result of slower cycle times, manual labor, and less automation.
Lead Time
Another major factor you need to consider is how soon you need the finished products. Some fabric fabrication processes create the first few parts within a day. Other high-volume processes include tooling and setup that may take several months.
China Medical CNC Machining Inc. Plastic Fabrication Service
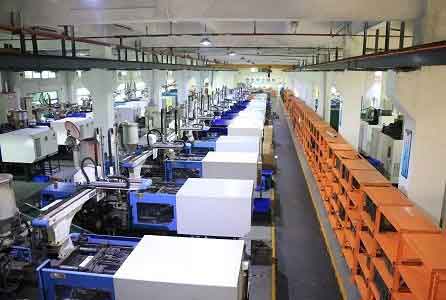
Many product designers, entrepreneurs, and engineers have been exposed to low-quality plastic fabrication. Do you need the best plastic fabrication company to handle your manufacturing processes?
Then, choosing RapidDirect will be one of the best decisions you can make. At China Medical CNC Machining Inc., we support the use of a wide range of plastic manufacturing processes. We consider plastic fabrication a crucial part of prototype operations for quality applications.
Our large number of expert engineers will refine the design of your parts and ensure efficient fabrication. All of our engineers specialize in relevant technologies and processes. Therefore, you can be sure of high-quality on-demand services. Once you’re ready to work with us, we provide you with all the information related to your project.
We also provide updates on the manufacturing process and a faster turnaround period. We carry out heavy research, consistent analysis, and rigorous tests to ensure your finished product meet industry standards. You’ll get all of this at a very affordable rate.
Conclusion
Choosing the best plastic fabrication process requires a good understanding of how to fabricate plastic. This article introduces the most significant plastic manufacturing processes to help you understand what they entail. We also covered the different factors you must consider to choose the best process for your application. At RapidDirect, we’re always ready to take your plastic fabrication projects to the next level.
FAQ – Plastic Fabrication Processes
How Do I Know the Materials to Use for My Products?
Selecting materials is specific to they what the plastic part is intended for and its characteristics. Understanding the following will help you choose the right materials:
- Application of the product
- How the finished product will perform its application
- The conditions the product will be exposed to
- Color requirements of the part
- Electrical conductivity
- Regulatory requirements
What is the Difference Between Blow Molding and Injection Molding?
The most noticeable difference between the two plastic processing techniques can be seen in the parts. Parts made with injection molding are solid, while blow molding makes hollow parts. Also, different molds are used during the manufacturing process. Injection molding requires the injection of melted resin into a hollow mold until there’s complete filling. On the other hand, blow molding involves the heating and filling of plastic tube to form a parison.
What is the Function of a Mold in Plastic Manufacturing?
The mold is a hollow cavity receptacle. It is usually made of metal, allowing the pouring of melted plastic resins. Often, a mold is designed to meet the initial template of the final product. Therefore, the mold is crucial to reproduce several uniform copies of the intended final product.
Share on social media...
Tags
Popular Topics
1
Ceramic CNC Machining: Another Option for Custom Manufacturing
Oluwafemi Adedeji13 Feb
2
The Overmolding Design Guide You Must Never Forget
Oluwafemi Adedeji13 Feb
3
What You Need to Know About the Overmolding Process
Paul Richard05 Feb
4
The Guidelines of Laser Cutting Product Design You Must Never Forget
Oluwafemi Adedeji01 Feb