Many important technologies comprise what has come to be known as Industry 4.0, all of which have been making major contributions to how machine shops will operate in the future. Some of the most interesting advancements in recent years have been in the realm of IIoT (or Industrial Internet of Things). As a concept, it has the potential to shape how the custom machining industry structures its production, quality assurance and workflow.
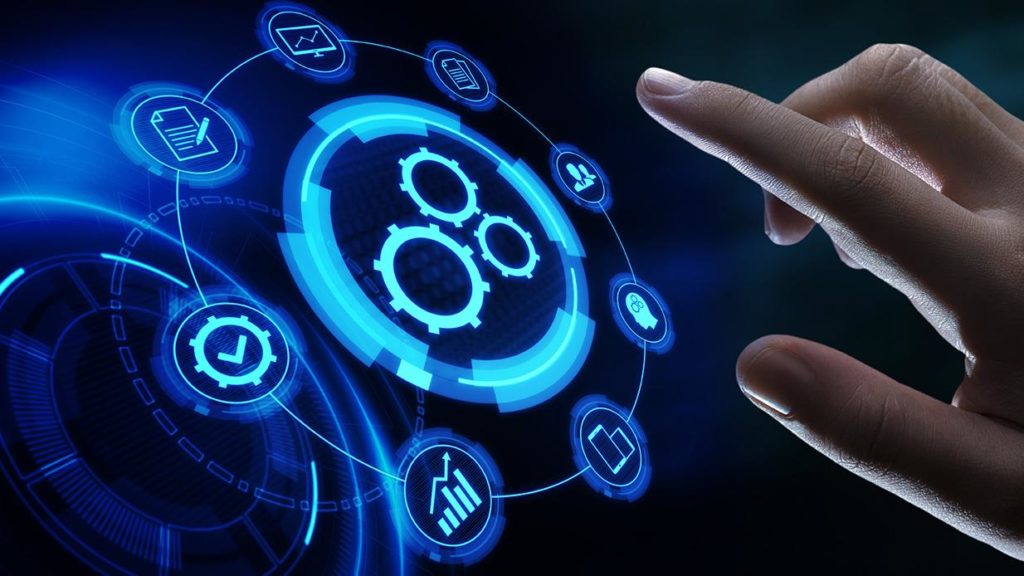
As a technology, Global spending on IIoT Platforms for Manufacturing is slated to grow from $1.67B in 2018 to $12.44B in 2024. This gives it a 40% compound annual growth rate (CAGR) over the course of seven years, according to Forbes. Among the industries that will benefit most from this, manufacturing is expected to be at the top in the coming years. The use of such technologies promises a greater level of connectivity than ever before, boasting particular applications for the custom machining and additive manufacturing fields.
Here are the key benefits it can provide:
1.Defining Industrial Internet of Things
As an innovation, the Internet of Things covers a pretty broad section of technologies, but they share one thing in common: data communication. IoT encompasses people, processes and the use of technologies that communicate with smart sensors and actuators. As a result, the technologies in question can transmit data in batch processing or even real-time, so as to create a smart network.
The Industrial Internet of Things is a subset of this category of technologies that focuses on industrial applications. This can be machines and processes that allow for constant monitoring and evaluation of products as they are being built. IIoT is also referred to as the ‘Industrial Internet’, which is a term GE coined in 2012.
The broader Industrial Internet doesn’t just refer to electronics or manufacturing, but also to tools and traditionally non-electric equipment. An example of this can be seen in new metal pipes that instantly send signals when they detect corrosion anywhere in their lining. These can detect leaks in industrial equipment before they get out of hand, and in some cases can shut down the system in the event of abnormalities.
Many IIoT compliant devices have in-built sensors but other manufacturing technologies can be retrofitted after the fact. These sensors allow them to carry signals that can make communication far more convenient for a machine shop. The reporting can easily be set to a plethora of common devices, from phones to computers. These devices can often piggy-back off of wi-fi, Bluetooth or Near Field Communication (NFC), making them easy to apply to any workplace with little additional sensors necessary.
This doesn’t just comprise the main CNC machine, but even parts and bits. This would be a paradigm shift, as now individual machine components would be able to broadcast data such as temperature readings, performance metrics, levels of vibration, etc. This in-depth data can lead to far better standards of machine operations along many fronts.
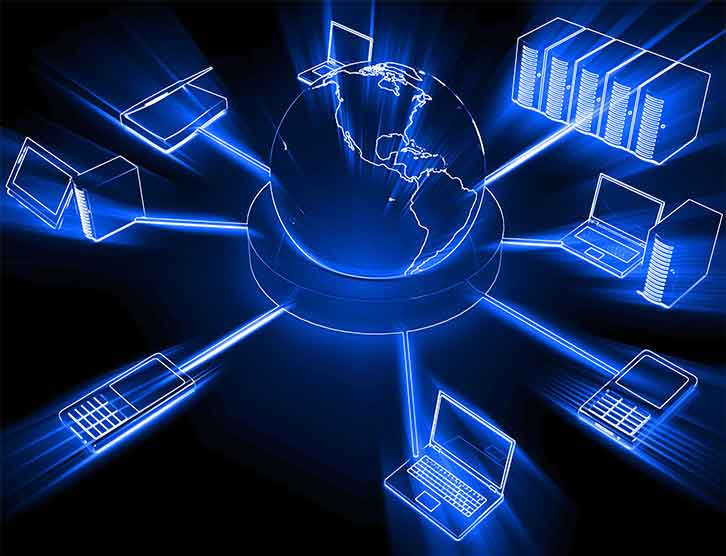
2.Process Monitoring & Quality Assurance Made Easy
While quality control can be laborious under normal circumstances, IIoT systems can ensure all the relevant quality assurance metrics and checks are taken care of. These make the upkeep duties of the machine shop far easier and relieve the use of manual labor and in-person checks. These factors help any manufacturing operation run smoothly with the aid of cloud computing platforms that keep performance and product quality up to scratch.
One of the ways the Industrial Internet of Things achieves this is with enhanced processed monitoring and keeping functions running optimally. This allows for better material usage and better processes. IIoT devices also provide process analytics and data to further improve the state of a machine shop’s workflow.
It can also make adjustments based on external weather or temperature changes, humidity and other factors that may affect how machines perform. This can be particularly useful for sensitive operations, where machines can detect possible changes and adjust for them. This could entail communicating with the thermostat or air conditioning to keep a necessary level of warmth within the work environment.
In terms of process improvements, devices operating within the Industrial Internet can communicate with each other within M2M systems. This can allow devices in the same workflow to share info about abnormalities or variations in a product on the assembly line or machining process, allowing them to adjust to make up for deficiencies in one area or the other. This enhanced level of communication between steps of the manufacturing workflow can improve the quality of the end-product and ensure consistency across units all at once.
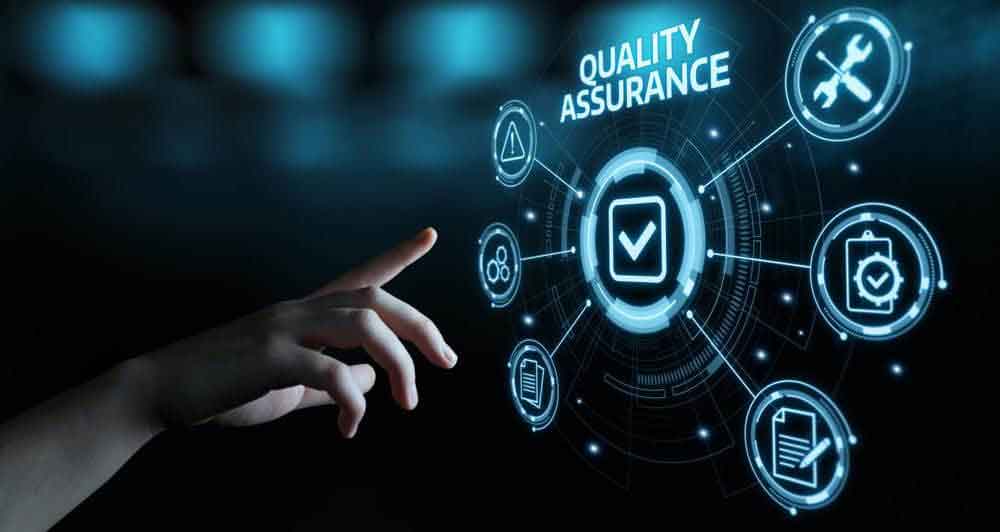
3.Preventative CNC Machine Maintenance
IIoT moves the paradigm from reactive to preventative maintenance. This keeps machines functioning at optimal quality and prevents breakdowns. In the long run, this is a far better solution that prevents the halting of the work process that might happen due to repairs and manual check-ups. Additionally, with the ability to put sensors in a lot of different machines, it’s easier to detect and alert users about very specific problems with components.
Companies like Fanuc use sensors within their robot along with cloud-computing to compile efficiency data. They can instantly detect component failures and relay them to engineers, allowing for far quicker fixes. The constant monitoring also gives supervisors the ability to take note of degradation pertaining to work performance, making part replacement quicker, less intrusive and much easier.
IIoT systems can keep track of over-heating, tool breakage, increased vibrations and a lot more. These metrics can give engineers a good idea of whether a machine part is in need of changes or replacement. Similarly, more in-depth data can inform maintenance staff about the need for lubrication or better chip clearance.
Scheduling maintenance checks can be a hassle for many machines, but having IoT components can allow for automated reminders. Custom machining shops have multiple CNC machines with so many components in constant need of monitoring. With the right software, parts can inform the engineers automatically. These sorts of systems can even send notifications right to a phone or a computer when necessary.
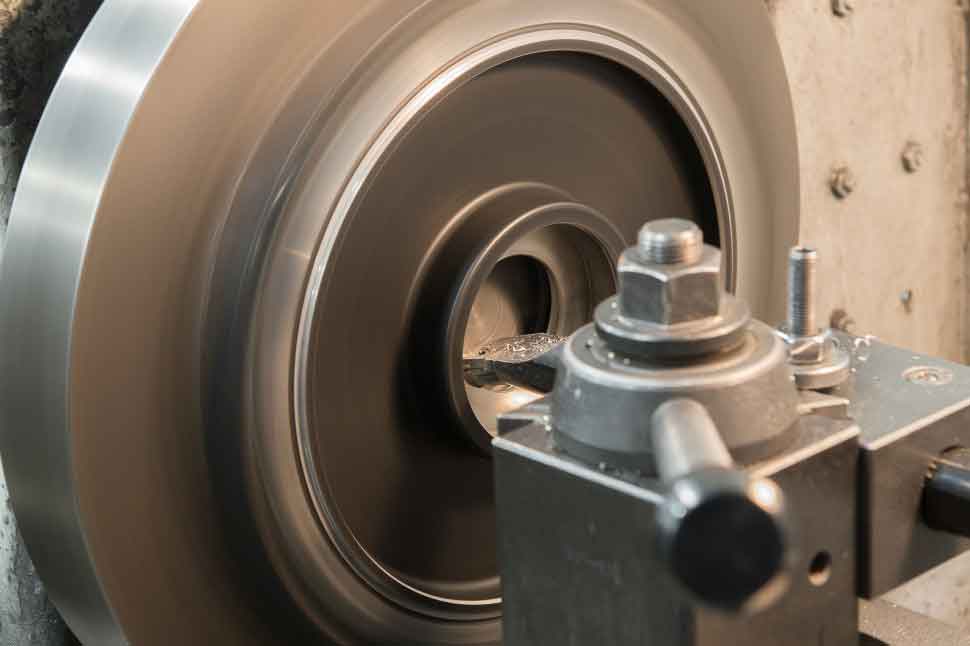
4.Production Benefits & Asset Tracking
IoT sensors within machines can also relay data to machine manufacturers. This particular type of benefit is useful for CNC machine manufacturing companies and machine shops in the long run. As they collect data usage, efficiency stats and monitor performance, manufacturers can upgrade and improve their CNC machines with further iterations.
This sort of data collection can give companies insight into their own products on the field and even allow them to make recommendations to users based on their own metrics. In essence, a manufacturer could notice lags or dips in a machine’s performance and contact them as a form of pre-emptive customer support. They can advise shops on how to optimize their systems with gathered intel.
By tracking their assets, manufacturers could aid machine shops remotely, without having to look at the machine or request an inspection from the owner. Consequently, the company can give feedback and resolve issues far quicker. Machine shops could derive massive benefits from this by requiring fewer maintenance checks of their own.
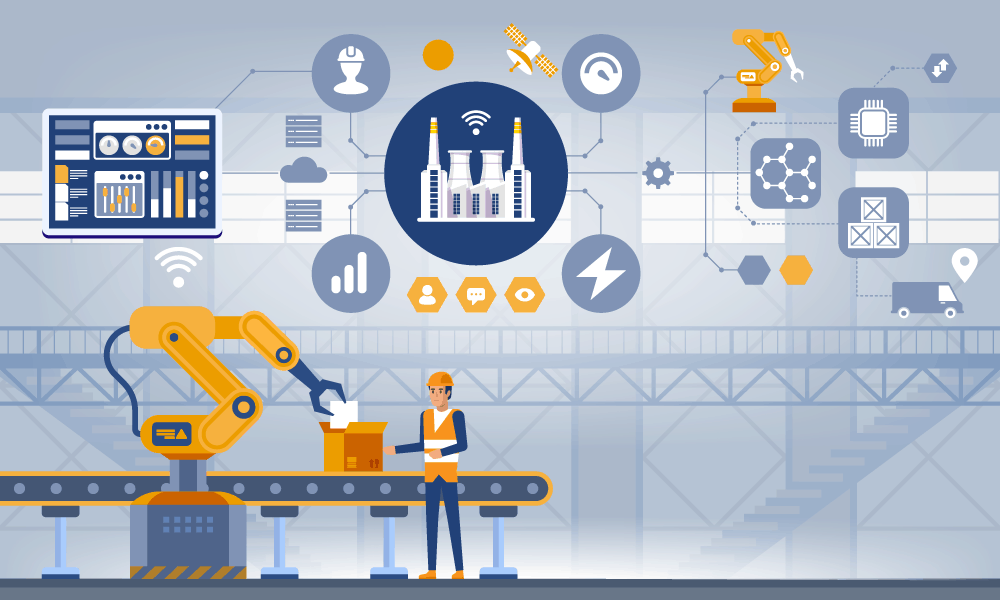
5.Decreased Manual Labor & Better Safety
Like with all forms of automation, IIoT decreases the level of labor required at any given moment. As machines are monitoring themselves, companies can rely on messaging systems, computer data collection and quality assurance procedures within the IoT process to take up the load. This frees up staff to focus on other duties.
Similarly, as machines can monitor their own status, they can pre-emptively warn staff about over-heating, mechanical failures or any potential power shortages. These can decrease workplace injury and make repairs far less reliant on guesswork as well. Another aspect of this constant monitoring is that it can decrease workplace hazards due to the lack of presence of physical staff. As monitoring is done remotely, fewer workers being present leads to less potential workplace safety violations.
This is just the tip of the iceberg, however. Many companies are already working on repair and maintenance robots that operate on IoT principles. These robots can detect and manage other machines using pre-programmed protocols. This would further eliminate the need of human presence and ensure instant repairs in most situations. These IIoT solutions would have a lot to offer.
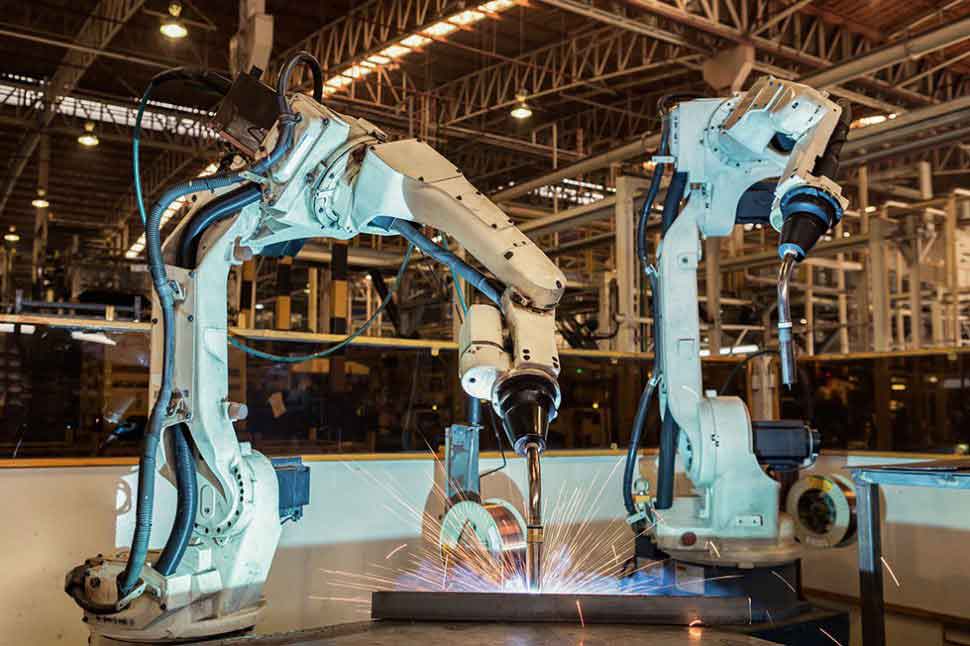
These functions are still only scratching the surface of what’s possible since the technology is still developing. IIOT confluence of its growth along with CNC machining and 3D printing is shedding light on all sorts of workflow improvements and modes of production. These technologies are likely to grow together in the near future, offering new possibilities to machine shops all over the world.
Share on social media...
Tags
Popular Topics
1
Understanding Plastic Fabrication Processes: A Complete Guide
Ayotomiwa Omotosho13 Feb
2
Ceramic CNC Machining: Another Option for Custom Manufacturing
Oluwafemi Adedeji13 Feb
3
The Overmolding Design Guide You Must Never Forget
Oluwafemi Adedeji13 Feb
4
What You Need to Know About the Overmolding Process
Paul Richard05 Feb