Have you ever wondered how machinists make those heavy aluminium tools and engine parts? They definitely did not make them with hands or cast in a furnace. They make these parts from a process called CNC precision machining.
For those who are new to the manufacturing world, CNC precision machining is a manufacturing process that enlists the use of computer programs to create any product to exact specifications. This article will define the process, the different pieces of equipment used, its applications, the different programming and processing involved. If you have an interest in learning more about this manufacturing process, you should read to the end.
What is CNC Precision Machining?
Definition
If the question “What is precise machining?” still lingers in your mind, here’s the answer. Just as the name implies, CNC Precision machining involves shaping raw material into a finished product by cutting out excesses as designated by a Computer Aided Design (CAD) or Computer Aided Manufacturing (CAM) blueprint. Machinists use this process in different manufacturing processes and on different materials.
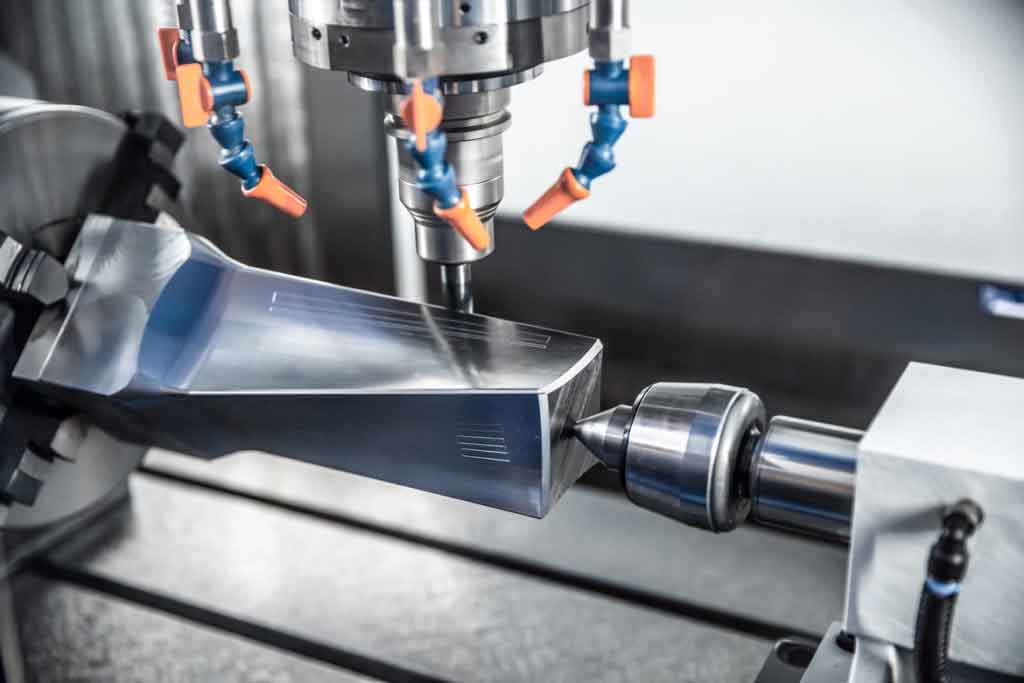
Before any product can be successfully made using precision CNC machining, the product’s blueprint must have been made using CAD or CAM programs. These programs make highly detailed 3D outlines that a precise machining process must follow to replicate the product successfully.
From toys to medical devices, automobiles, or space shuttles, any product that has parts needs precision machining. Using Computer Numerical Control (CNC) equipment, the process utilizes actions like cutting, milling, turning, and electrical discharge machining to achieve the final product.
Although the process requires the overwatch of a skilled machinist, a machine does most of the work automatically. The Computer Aided Design (CAD) software creates the design, the Computer Aided Manufacturing (CAM) software then translates it into manufacturing instructions for the machine. A final post-processor software codes the instruction into information the machine can understand. The machinists then load the instruction into the CNC equipment to start the manufacturing process.
Tolerance
Although precision CNC machining tools are very accurate, these machines cannot accurately reproduce the dimensions of products just as they are in the CAD blueprint. This is why machinists use tolerances.
Tolerance is the amount of deviation in the dimension of a part that is acceptable by conventional standards. A synonym for it is dimensional accuracy. There is no standard tolerance for all precision CNC machining processes. The strictness of tolerance depends on the manufacturing process. The number of decimal places a tolerance value has shows the strictness of the measurement.
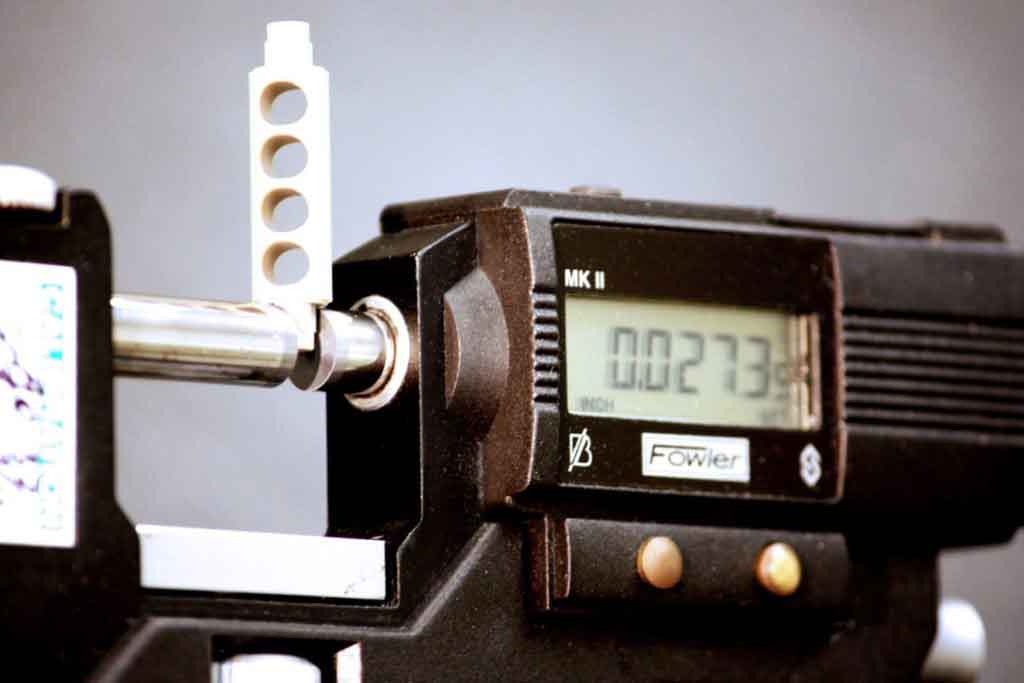
There are different types of tolerance measurement systems. Examples include;
- Unilateral Tolerance measurement: In this type of tolerance measurement, the deviation is only allowed on one side of the nominal value. This means if the nominal value of a shaft to fit into a bearing is 20mm, a shaft larger than this wouldn’t fit in. Therefore, machinists only allow the deviation for such a shaft on the smaller side.
- Limit Tolerances: This is when the tolerance value is placed in a range. For example, if the nominal value for the shaft is 15mm and the tolerance is expressed as 15 – 15.5mm, this represents a limit tolerance.
- Bilateral tolerances: This type of tolerance allows deviation on both sides of the nominal value. It is usually expressed as a +/- value. This means if a part has a measurement of 25 mm with a tolerance of +/- 0.05mm, it means the value can be within 24.95mm and 25.05mm.
Knowing when to choose tighter tolerances for your part manufacture is very important. Although it is not necessary for the whole part to have tight tolerances, the important structural parts, such as those which fit into other components, need little deviation from the nominal value as inaccuracy could severely affect the integrity of the part.
Tolerances are important in precise machining processes because they help to reduce production costs and turnaround times. As important as they are, they require a lot of skill and patience to get it right. The standard tolerance of CNC machines is 0.005 inches. At China Medical CNC Machining Inc., our 5-axis CNC machines can achieve tolerance up to 0.002”. We offer a range of tolerances to suit our customers’ needs. Our standard tolerances for CNC machining metals are compliant with DIN-2768-1-fine, while for plastics it is DIN-2768-1-medium, a full chart of these tolerances can be found here.
Types of Precision CNC Machining Equipment
Due to the different processes involved in CNC precision machining, it requires different pieces of equipment to make it work. In some cases, these tools are put on a single machine, and the machinist only has to start and stop the process.
In some other situations, the tools have to be placed on different machines, and the machinist will have to move the workpiece/raw material from one machine to another. Examples of machines used in CNC precision machining includes:
CNC Milling Equipment:
Milling is the precise machining process that involves using rotary cutters to remove excess material from a workpiece. It involves several types of mills. Examples of such mills include end mills, chamfer mills, and helical mills. The CNC-enabled mills also include hand milling machines, plain milling machines, universal milling machines, and omniversal milling machines. These machines either have a horizontal or vertical orientation.
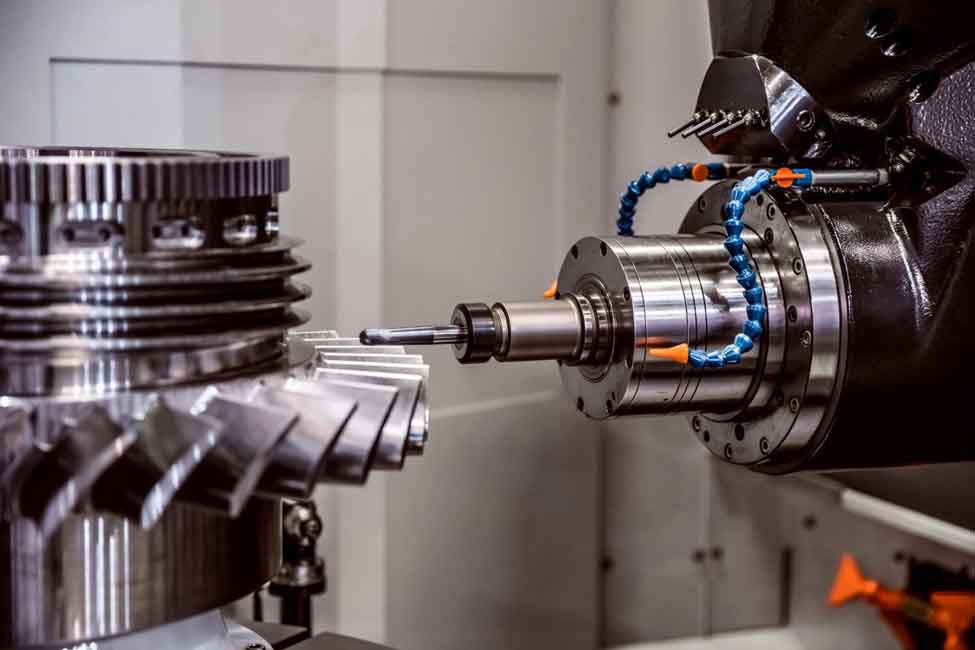
CNC Turning Equipment:
Turning is a precision CNC machining process that involves rotating the workpiece next to a rotating single-point cutting tool. The most popular tools used for turning processes are lathes. Examples of lathes include turret lathes, engine lathes, and engine-purpose lathes. Other turning equipment includes straight turning, taper turning, external grooves, and threads.
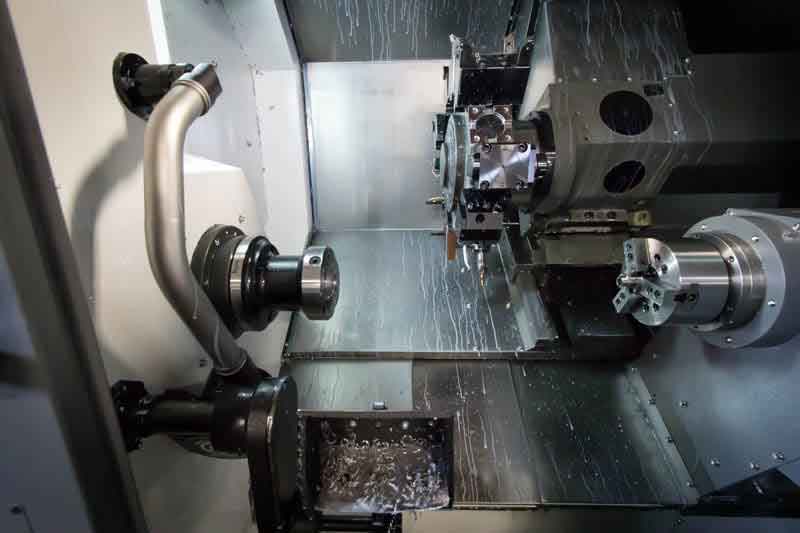
CNC Drilling Equipment:
Drilling is a precise machining process that uses rotating multi-point drill bits to create cylindrical holes in raw materials/workpieces. The design of the drill bits allows the chips off the workpiece to fall away from it. This keeps the drilled holes neat.
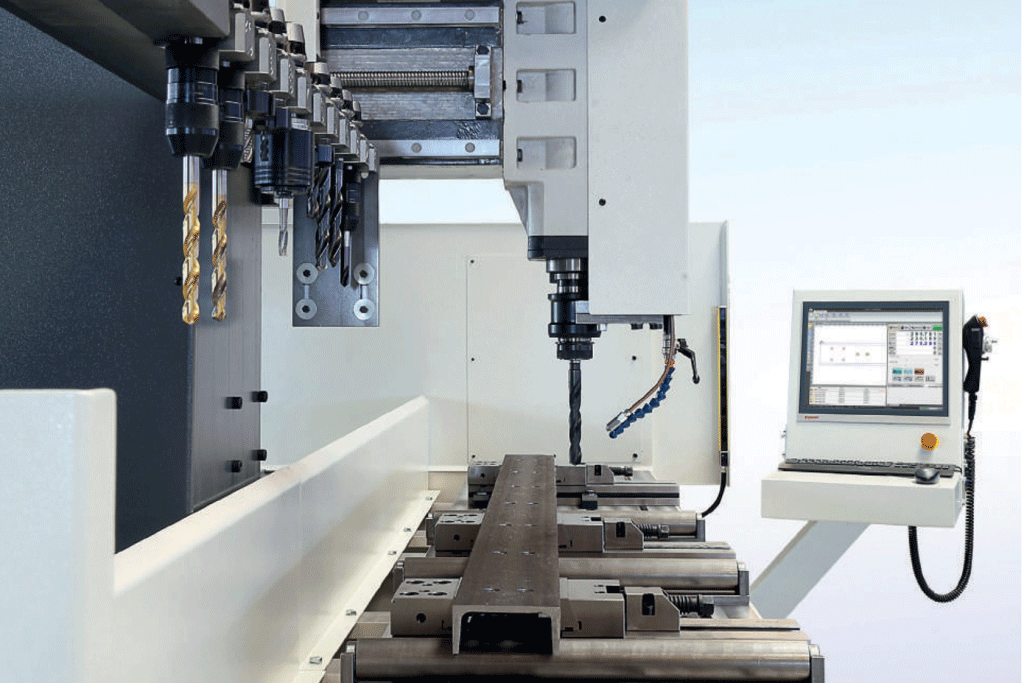
Examples of common drill bits used in CNC machining processes include spotting drills (for making shallow or pilot holes), peck drills (for reducing the number of chips on the workpiece), screw machine drills (for producing holes without a pilot hole), and chucking reamers (for enlarging previously produced holes). There are also drill presses, which are drill bits made for a particular drilling task.
CNC Electric Discharge Mining Equipment:
Electrical Discharge Mining is a precise machining process that uses electrical discharges (sparks) to obtain the finished product.
The setup is made up of the tool electrode (tool) and the workpiece electrode (workpiece) separated by a dielectric fluid and subject to an electrical voltage. The process is also known as spark machining, spark eroding, burning, die sinking, or wire erosion.
CNC Precision Machining Applications
Industries
Precision Machining is gradually gaining more ground in the manufacturing world due to its multiple uses, cost, and time-effective processes. The precise machining process is used in industries like:
- Medical Industry:
Medicine is rapidly evolving with the need arising for new equipment. Apart from producing New equipment, they also have needs for high volumes of existing ones. Precision CNC machining is responsible for making this equipment. Examples of such include orthotic devices, safe enclosures, Implants, MRI machines, research equipment, etc.
- Automotive Industry:
With automobile companies coming up with new innovations to add to their latest car iterations, they need to develop prototypes of these parts before adding them to the manufacturing line. CNC Precision machining is responsible for developing these prototypes to exact specifications. CNC precision machining also makes parts for other means of transport like shipping vessels, transport trucks and many more.
- Aerospace Industry:
Ranging from transportation planes to space shuttles, aerospace vehicles require very precise contraptions as a single error could lead to severe damages on the different aeronautical vehicles. The CNC precision machining process is responsible for making many components in this industry, such as landing gear ports, bushings, manifolds, airfoils, etc.
- Military and Defense Industry:
CNC has never been more relevant, with different nations having different designs for new ammunition and defense systems. The precise machining process is responsible for bringing all of these designs to life using various materials and processes. Examples of devices made for this industry include plane parts, transportation components, communication components, ammunition, etc.
Advantages
Using these highly precise machines for your manufacturing process would definitely provide a host of advantages. A few are:
- Reduced cost of production:
In terms of price, CNC Machining is the way to go especially if you’re looking to make a few to a hundred parts. CNC machining will require a less upfront cost compared to injection molding (due to the expenses of creating the mold).
- Increased speed:
CNC machines provide a higher rate of speed compared to injection molding. Unlike injection molding which might take months to make the mold and ensure the parts are in tolerance, CNC machining can produce parts in a matter of weeks.
- Allows for Rapid and Cost-effective Prototyping:
With CNC machining services, your prototype production is even more effective. This is because CNC can work with a lot of cost-effective materials, so you don’t have to spend a lot on prototypes. Of course, when the prototypes are made faster, the whole production process is quickened even more. At China Medical CNC Machining Inc., we deliver prototypes that meet up to manufacturing requirements and quality standards.
How to carry out precision machining
Materials
Precision CNC machining can operate on a wide variety of materials. At China Medical CNC Machining Inc., we provide you with material certification (SGS, RoHS, etc.) if you request for it. Here are a few examples of metals and plastics we offer certification for:
Metals
- Aluminium (Aluminum 6061, Aluminum 6061-T651, Aluminum 606, etc.)
- Stainless steel (201, 301, 303, 304, 316, etc)
- Steel (1008, 1018, 1020, etc)
- Brass (280, 260, 2680, etc)
- Copper
- Bronze
- Titanium
Plastics
- ABS
- PC
- PMMA
- POM
- PA
Above are just the most common materials in precision CNC machining. China Medical CNC Machining Inc. provides hundreds of materials for your custom prototyping and production needs. To check the full list of our materials, upload your design to get instant quote in minutes and start your project today!
Programming
Before the precise machining process can commence, the machines have to be programmed to make the process run smoothly without any errors. To do this, here’s the process to follow:
After the Computer-Aided Design (CAD) software has made either the 2D vector or 3D solid blueprint for the product to be manufactured, it is exported to a CNC-compatible file format like STEP or IGES.
The Computer-Aided Manufacturing Software (CAM) then generates the digital programming code that will control the tooling and produce the custom-designed part.
There are two main programming codes: the G-code and the M-code. The G-code is more popular and is known as the Geometric code. It tells the machine when, where, and how the machine moves. The M-code is the miscellaneous function code that controls the auxiliary functions of the machine.
Processing
After programming the machine, the next step is to start processing the raw material to get it to fit the exact specifications for the finished product. Depending on the product, quite a few processes are used in getting the final product. Examples include:
- CNC Milling
- CNC Turning
- CNC Drilling
Surface Finishing
This involves plating the surface of the finished product with different materials to further strengthen and beautify it. At China Medical CNC Machining Inc., we use different types of finishing techniques such as anodizing, bead blasting, electroplating, powder coating, etc.
Conclusion
CNC Precision machining is arguably the most effective way to manufacture your custom-made parts. Apart from saving you cost, it takes very little time and allows little space for errors. Incorporate this manufacturing process into your production today!
RapidDirect: The Precision CNC Machining Company You’ve Been Searching For
At China Medical CNC Machining Inc., we bring your CAD blueprints to life in the best way you could ever hope for. We guarantee strong manufacturing capabilities with our wide array of engineering experience and approach. Our 3,4, 5-axis CNC machines and a wide range of auxiliaries make us capable of your CNC designs, be it custom prototypes as little as one or making parts taking up to months of production.
Our technical support for our clients is unrivalled. We offer services like shipping the product in two sets if you wish. The first set would be shipped to get your verification before we go into full production. After finishing production, we give you the right assurance that your product will fit and work just as it is meant to by shipping it with the part dimensions. We also provide material certification with all our products which enables you to find out about the material characteristics.
Apart from all these features, our prices also stand out from the pack. With a 30% lower price than the average you’ll find anywhere, we help you save costs on production at China Medical CNC Machining Inc.. Just as stated in our certified ISO 9001:2015 QMS standards, we supply you with finished parts of the highest quality made with the latest advancement in CNC technology.
At China Medical CNC Machining Inc., you do not have to wait for ages to get your quotation. Once you upload your CAD file to our website, you get the online quotation that provides you with a real design within a minute. This saves us all the back-and-forth emails. You also enjoy the Design for Manufacturing feature, which shows if your design is ideal for manufacture or not.
Upload your design files and start your project today!
FAQ
CNC precision machining simply involves shaping a raw material/workpiece to meet specific and exact dimensions. This involves using blueprints made from CAD and CAM designs.
A CNC mill cost depends on the size and range of operations they can execute. Its prices range from around $50,000 – $170,000.
The phrase used to quantify the accuracy of a CNC machine is ‘positional accuracy.’ It is calculated by programming the machine to move to a particular value and its deviation from these programmed value is recorded. After taking multiple readings, the statistical average value of the deviations is calculated and this is the positional accuracy of the machine. 0.02mm is the average value for most CNC machines. If your value is not within that range, your machine is most likely not accurate.
Share on social media...
Tags
Popular Topics
1
Understanding Plastic Fabrication Processes: A Complete Guide
Ayotomiwa Omotosho13 Feb
2
Ceramic CNC Machining: Another Option for Custom Manufacturing
Oluwafemi Adedeji13 Feb
3
The Overmolding Design Guide You Must Never Forget
Oluwafemi Adedeji13 Feb
4
What You Need to Know About the Overmolding Process
Paul Richard05 Feb