When we talk about plastic products, the most common manufacturing method is injection molding, covering a vast majority of the plastic parts we use every day. As the names suggest, injection molded parts produce intricate, complex objects using plastic deposited into molds until the material solidifies into the desired shape. Producing molds would ordinarily require CNC machining from various metals like aluminum or steel.
However, more and more companies are opting for 3D printed injection molds rather than those that use subtractive manufacturing methods. Here are some of the reasons why:
Cheaper Molds & Faster Production
One of the issues with traditional injection molding is that molds can be expensive to make. These molds would require a massive investment that could be as large as $3,000 to over $100,000 (depending on the complexity of the mold or the material being used). In fairness, these would often net a large number of objects when at high-volume production rates. The molds would also last fairly long. Still, these can be a massive amount to pay, especially compared to their 3D printed counterparts.
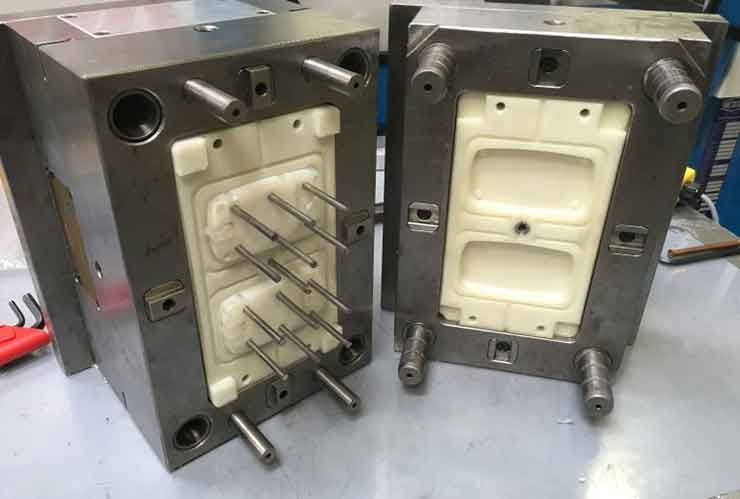
3D Printed injection molds, especially ones developed with SLA or Material Jetting, can roughly match the accuracy of CNC machined molds at a far lower price. They can also allow for far faster turnaround time for products, prototypes, and testing. Not only that, but they also allow companies to produce and test molds in-house, with an increased level of control over the final product.
Control switch manufacturer Berker found these benefits to be crucial in their operations. Using an Objet30 Pro, they were able to reduce production times from 28 days to 3, while diminished costs from $22K to USD 3K.
“This new flexibility enables us to try out two or three different solutions at the same time to get the best result,” says Andreas Krause Head of Technical Department & Manufacturing at Berker. “The confirmed quality of our products produced using these functional prototypes has accelerated our R&D processes.”
Low-volume Manufacturing
As mentioned earlier, while 3D printed molds are great for price and speed, they aren’t all too applicable to large-volume manufacturing. This is because printed plastic molds are not as good at resisting wear and tear and thus, they don’t last as long. However, this isn’t a massive drawback as this has allowed it to develop a niche in the realm of low-volume manufacturing. Prototype injection molds created with 3D printing were never intended to be replacements for soft or hard tools in mid and high-volume production, but they are intended to fill the gap between soft tool molds and 3D printed prototypes.
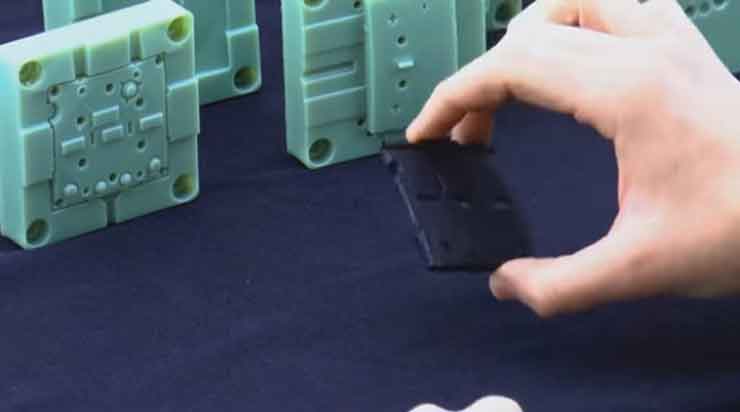
With the use of modern temperature resistant 3D printing materials and the design freedom, 3D printing allows, 3D printed molds have become a viable option for manufacturing low-run injection molding dies. These molds are best suited for faster turnaround times (1-2 weeks opposed to 5-7 weeks). For certain products like electrical components or plumbing equipment, it’s more profitable to have smaller runs rather than jumping into mass manufacturing.
These runs can operate with production quantities as low as 50 – 100 parts. They are also great for fairly small parts, i.e. less than 150 mm. While the runs may seem small, they drastically reduce the start-up costs for injection molding, allowing companies to produce in the middle-size production level.
Enhancing Part Complexity
There are two types of printed injection molds: Mold inserts developed in aluminum frames and those that are developed as stand-alone pieces, entirely 3D printed. In terms of quality, 3D printed molds without frames have quite a bit to offer. This comes down their basic construction, as they can allow for all sorts of details when they don’t rely on these traditional aluminum casings.
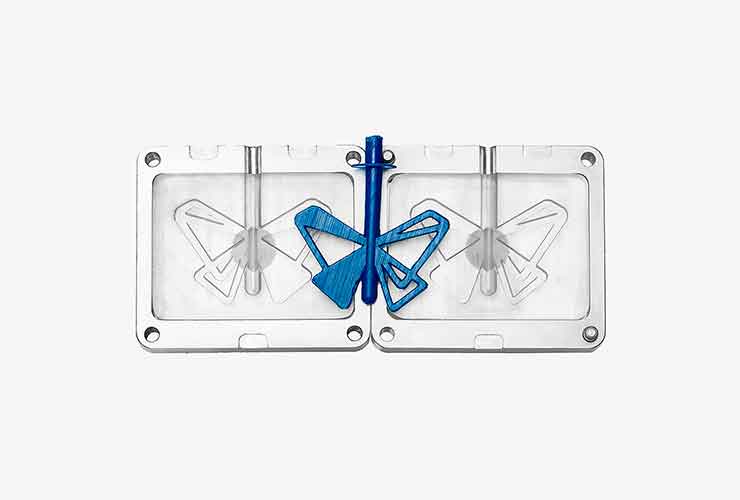
Without the use of the aluminum frame, the printer may have to use more material and time, but it will ensure that smaller details like intricate cooling channels. The higher level of detail these molds allow can be crucial to adding all the tiny functional components and gaps that certain products need. Companies like Grundfos, who produce pumping systems, found that this was the best way to get tiny details into the molded object while maintaining an excellent surface finish.
This is even more impressive considering how injection molding already offers some of the most complex parts and best finishing on the market. However, the final product is only ever as good as the mold it was made from, and so these details push the envelope even further.
If you’re interested in learning about all the possibilities offered by Modern manufacturing like 3D printing, CNC machining or a host of other technologies, be sure to check out cn.mfgmachined.com for more information or convenient on-demand services.
Share on social media...
Tags
Popular Topics
1
Understanding Plastic Fabrication Processes: A Complete Guide
Ayotomiwa Omotosho13 Feb
2
Ceramic CNC Machining: Another Option for Custom Manufacturing
Oluwafemi Adedeji13 Feb
3
The Overmolding Design Guide You Must Never Forget
Oluwafemi Adedeji13 Feb
4
What You Need to Know About the Overmolding Process
Paul Richard05 Feb