Injection molding is one of the most popular manufacturing processes alongside CNC machining and 3D printing. However, it is notorious for its relatively high prices unlike the other two. Many factors, such as the complexity of your product, the quantity of the product, etc., go into determining the price of an injection molding process.
This article will explain why the process is expensive, how machinists calculate and even suggest useful tips on how to reduce your injection molding costs. Read to the end to find out great money-saving suggestions on injection molding costs.
Why is Injection Molding So Expensive?
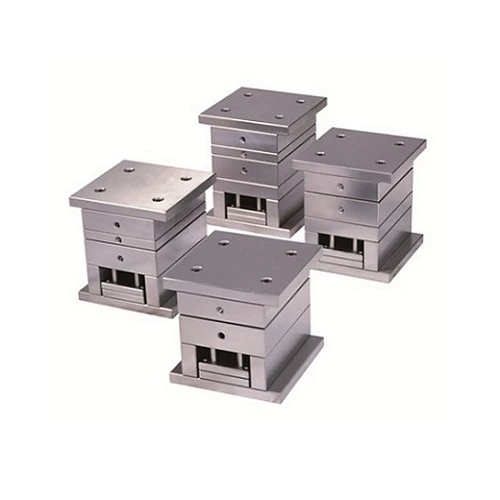
Plastic injection molding produces plastic parts by heating plastics pellets to their melting points and injecting them into a metal mold. The process involves leaving the molten plastic to cool and retain the shape of the mold when it hardens.
The injection mold used to shape the molten plastic is unarguably the most expensive part of the molding project. But why is the mold expensive? Here’s are some reasons below:
1. The materials used to make the mold are quite costly
The materials used for making the mold have to be high grade, hence their expensive cost. This is because the injection molding requires thousands of pounds of pressure to make the plastic pellets, and a weak mold cannot withstand such pressure. Thus, machinists make the mold out of solid materials that can stand the test of time and not deform in the face of such high pressure.
The mold base contributes to the high cost of molding.
The base is like a case holding all the mold cavities in place. It also holds the inserts and other components of the mold together. The bigger the size of the mold, the costlier the base.
2. The complexity of the part to be produced
The complexity of the part you want to produce is another reason why injection moldings are expensive. Therefore, if you want to make complex parts, you have to spend more to design and machine a complex mold. In other words, the more the complexity of the parts you want to produce, the more complex and costly the mold.
Once they make a mold for a particular design, to modify it is sometimes impossible. Hence, if you need to make multiple designs, you may have to purchase new molds. This is another reason why molding is so expensive.
Breakdown on Injection Molding Costs
To make an accurate calculation of the cost per part of injection molding, we need to factor in all the manufacturing processes and what those processes entail. These factors include the cost of labor, type of materials used, etc. In this section, you’ll learn how to calculate plastic injection molding costs like a professional. The factors to consider include:
1. Cost of the plastic injection mold
As earlier discussed, injection molds come in different sizes and sell at different prices. To purchase a plastic injection mold, you may be looking at spending a thousand dollars or even tens of thousands, depending on the machine’s complexity. However, if you need a single cavity mold, you don’t have to bother about spending so much on purchasing a mold with multiple cavities.
2. Cost of Polymer resin material
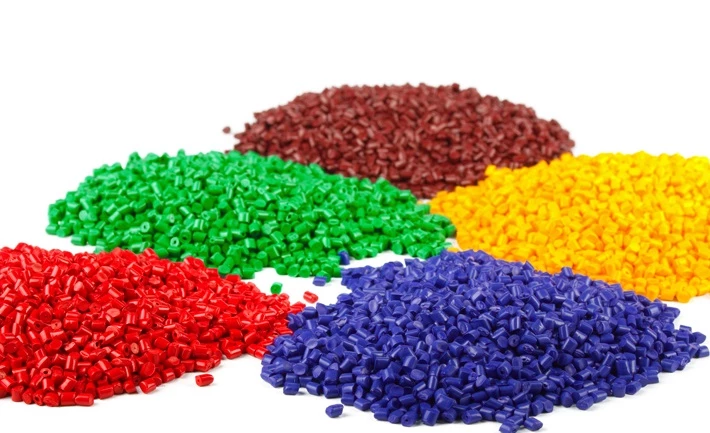
A polymer resin is an essential part of the production. Therefore, the quality of Polymer resin used in the production will influence the plastic injection molding cost. For instance, if you make parts using engineering resin with extra strength and chemical resistance, the material will be a little more expensive than those made of commodity resin-like polyethylene. If you want low-cost injection molding, you can opt for resins made from recycled plastics. They are more affordable.
3. Cost of labor
Although the company is fully in charge of hiring the machinists needed and maintenance of machines and tool bits needed for the job, the cost of labor will be partly included in the quotation you receive, which is also a part of the custom injection molding cost.
Tips to Reduce Injection Molding Costs
Saving costs on manufactured parts is not rocket science. Therefore, you can reduce your injection molding costs without compromising the quality of your produce. The following tips will save you some dollars while working on your molding designs:
1. Avoid Unnecessary features
In most cases, molded part numbers, textured surfaces, and company logos are unnecessary for your designs. They consume extra polymer resin, which will add up to your injection molding costs. However, in some cases like military applications and aerospace, permanent part numbers may be required and cannot be omitted. However, there’s are still ways around that.
You can still save cost by using a mill-friendly font like Arial, Century Gothic Bold, or Verdana (san-serif fonts). To further save cost, you need to do more than opting for these fonts is. You shouldn’t go deeper than 0.010 or 0.015-inch maximum. Going deeper will require more resin, and that is not economical. You should keep your font above 20 pt so that they are legible enough to read. You could use our design guide to check if your design is a good fit for production
2. Only use cosmetics when required
Putting beautiful finish touches on your parts is nice, but some cosmetics should be avoided to save cost. You’ll spend some extra dollars by using EDM, bead blasting, high mold polish, etc., for your design, whereas, in some cases, they are not essential. If they are not needed, you should avoid using them to save cost. However, if you must polish the parts, you can still save cost by polishing half of the mold or the small area needed instead of polishing the entire body.
3. Mold mods
You can re-machine an existing mold to suit your new need instead of purchasing a new one. This process might be complicated, though, but if well done, it’ll save you some dollars, thereby reducing your injection molding tooling cost. Purchase the needed parts, and replace the old parts with them. That way, you’ve upgraded your machine to meet your new need without purchasing a new one.
4. Choose a suitable mold size
You can save yourself unnecessary stress and cost by purchasing a suitable mold size for your parts. Size in this regard refers to how big the pieces you want to design are and the volumes required. Some injection molds are ideal for smaller part quantities, while some are designed for larger quantities. To manage the demand volatility of your parts and leverage cost-efficient bridge tooling, you should choose a suitable mold size. This is another effective way to save injection molding costs.
You could also use our instant quoting platform on China Medical CNC Machining Inc., which gives you an estimate for the cost of your injection molding process within a minute. It calculates this using all the factors that we’ve mentioned earlier and gives an accurate result.
China Medical CNC Machining Inc. Turnkey Injection Molding Services
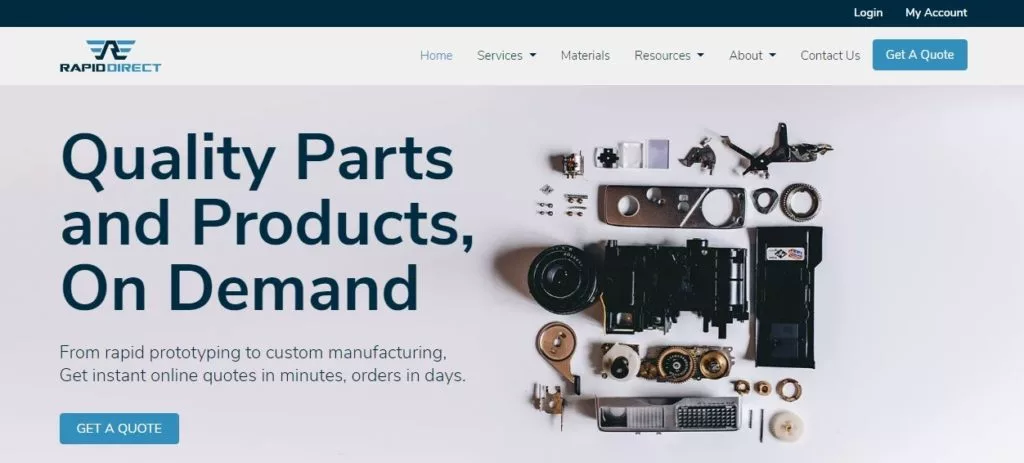
Have you been searching online to find a suitable firm offering quality custom injection molded prototypes and production parts? Then, you just found what you are looking for. China Medical CNC Machining Inc. is an expert in the industry.
You can rely on us to get prototype molds durable up to 10,000 components. One incredible feature that stands us out from others is our ability to provide you with an accurate quote in less than 24-hours. We know how much you value time; thus, we are time cautious. More so, we’ll provide you with in-time progress feedback and coordination during production. Therefore, you’ll not be kept in the dark during production; instead, you’ll see how committed we are to your project.
Do we have the robust capabilities required for your large project? Yes! We have a vast in-house factory denoting our supreme manufacturing capabilities. Therefore, you can rely on us to deliver your injection molded prototype parts on time.
FAQs
A: The price varies from a thousand dollars to tens of thousands of dollars, depending on the complexity of mold you desire.
A: Modern injection molding processes are more environmentally friendly. They owe this to their efficient machinery, coupled with durable thermosetting polymers that can withstand extreme temperatures. However, this doesn’t mean that injection molding is absolutely safe for the environment. It also releases harmful gases causing greenhouse effects, but this is well controlled with modern injection molding.
A: Yes, there are! You can achieve this by reducing or removing unnecessary features like company logos, textured surfaces, and molded part numbers, among others.
Conclusion
Injection molding is a popular manufacturing process due to its cost-effective solution to scale and produce a large number of parts. However, it could be quite costly, especially when you’re only making a handful of parts. You can read up on this article to find useful tips to reduce your injection molding costs or use our instant quoting platform to get an estimate for your injection molding process.
Share on social media...
Tags
Popular Topics
1
Understanding Plastic Fabrication Processes: A Complete Guide
Ayotomiwa Omotosho13 Feb
2
Ceramic CNC Machining: Another Option for Custom Manufacturing
Oluwafemi Adedeji13 Feb
3
The Overmolding Design Guide You Must Never Forget
Oluwafemi Adedeji13 Feb
4
What You Need to Know About the Overmolding Process
Paul Richard05 Feb