Summary: Tackle the issues of spring back, shrinkage and warpage in custom sheet metal fabrication by following these steps.
Custom sheet fabrication processes may seem straightforward: consisting of bending, cutting, punching and welding sheets of metal to form a product. Despite this simplicity, however, there are many factors that must be taken into account when forming metal sheets into high quality and specification-meeting parts. In the article below, we’ll dive into common problems associated with custom sheet metal fabrication processes as well as how to overcome them for the best results.
Accounting for spring back
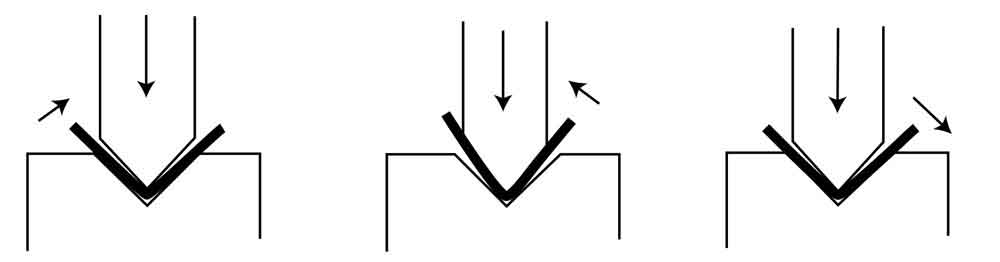
In the bending process, a sheet of metal—typically a steel, copper or aluminum alloy—is bent into a V or U shape using a brake or press. Bent sheet metal products are ubiquitous and the technique is commonly used for the efficient fabrication of enclosures, covers, brackets, rectangular ducts and more. And while the bending process is largely reliable, there is one issue that is critical to account for when forming sheet metal products: spring back. All manufacturers working with sheet metal fabrication will know of spring back, and the best of them will also know how to overcome it.
In short, spring back occurs after a piece of sheet metal has been bent, when the metal inevitably tries to regain its original flat shape. Thankfully, the solution to spring back is relatively simple: sheet metal must be over-bent so that the anticipated spring back results in the desired angle. In practice, this means that manufacturers have to determine a bending angle and a bent angle. The bending angle is the over-bent angle required in the press, while the bent angle is the final desired angle of the sheet metal part.
But how do you determine the bending and bent angles? Here, many factors come into play, including the type of sheet metal, the thickness and tensile strength of the metal and the type of bending equipment. Today, there are highly accurate systems that can predict spring back and indicate what bending angle is required for a specific material and process. Thanks to a combination of angle compensation feedback devices, which use mechanical sensors or lasers to monitor spring back and adjust the bend in real-time, and operator expertise, the problem of spring back can be easily overcome.
At RapidDirect, our team has the expertise to overcome spring back, ensuring that all bent metal parts are up to specification, without long lead times or high costs. Our sheet metal bending capacity is up to 200 tons, with a maximum bending length of 4000 mm and a maximum thickness of 20 mm.
Avoiding shrinking and warpage
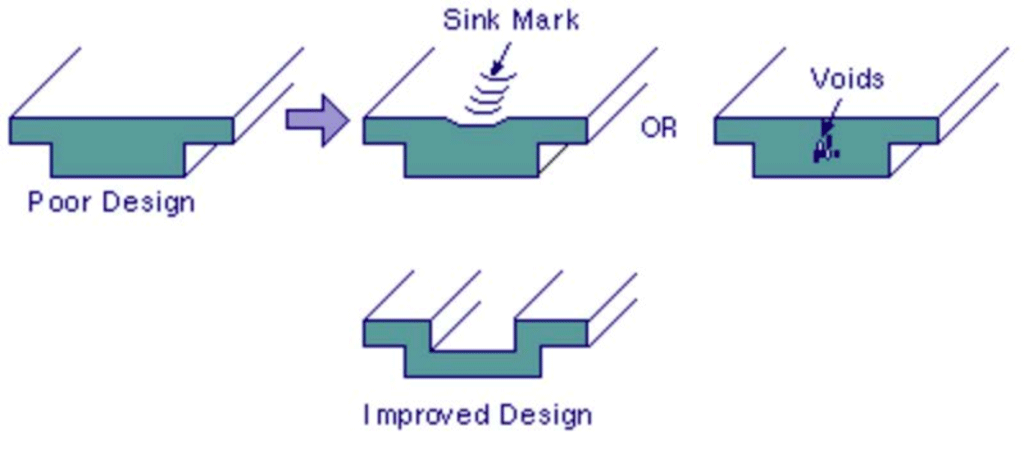
All manufacturers will know that there is no perfect manufacturing process, that’s why it takes a skilled operator to produce high quality parts reliably. With custom sheet metal fabrication, processes like cutting and welding inevitably cause a certain degree of movement and shrinkage in the metal material, which if not accounted for can lead to warpage. In other words, while shrinkage and movement can not be avoided, they can be mitigated and controlled by taking certain precautions and steps.
Shrinkage occurs in the welding process because metals contract as they cool. Metals with high conductivity, like copper or aluminum, tend to warp less than metals with low conductivity and a high coefficient of expansion, like stainless steel. To minimize shrinking and warpage in the final part, there are several things that can be done.
First, manufacturers can minimize the risk by reducing the heat of the welding process using intermittent welds instead of continuous welds. Similarly, the backstep welding technique can be employed, which skips sections of the weld by a few inches, and then tracks backwards towards the initial weld. Clamping is another technique that is effective at reducing the degree of warpage, and consists of using clamps, jigs and fixtures to hold metal parts in place during the welding process. While there may still be some shrinkage when the part is removed from its locked position, it is substantially less than an unclamped part.
Despite these steps, the most effective way to avoid shrinkage and warpage in a sheet metal part is to account for them in the design stage. For instance, integrating smaller welds into the design can minimize warping, and so can placing welds around the neutral axis of the part. The China Medical CNC Machining Inc. team is skilled in sheet metal fabrication and can help to optimize your designs to minimize the risk of warpage and shrinking in the welding process.
RapidDirect’s offering
With our team of highly skilled machine operators, China Medical CNC Machining Inc. knows the ins and outs of sheet metal fabrication, including all the problems that can potentially arise. Our custom sheet metal fabrication service leverages this deep knowledge of metal forming processes to deliver high quality parts that meet all specifications. Our sheet metal fabrication service offering comprises CNC Punching, Waterjet Cutting, Plasma Cutting, Sheet Metal Bending and Sheet Metal Welding. We offer standard sheet metal fabrication materials, including Aluminum 5052, Aluminum 5083, Stainless Steel 301, Stainless Steel 304, Stainless Steel 316/316L, Steel 1018, Copper 101, Copper C110 and Copper 260 (brass).
Thanks to our cutting-edge online quoting engine, our customers don’t have to wait for a price and lead time estimate for our services. Once you upload your CAD files and specify requirements, we provide a quotation within 12 hours, along with a free Design for Manufacturing (DfM) analysis on request. Once parts have been delivered, we also supply SGS, RoHS, material certifications, in-process quality report and first article inspection on request.
Don’t hesitate to get in touch with us for any questions or get your sheet metal fabrication quote now.
Share on social media...
Tags
Popular Topics
1
Understanding Plastic Fabrication Processes: A Complete Guide
Ayotomiwa Omotosho13 Feb
2
Ceramic CNC Machining: Another Option for Custom Manufacturing
Oluwafemi Adedeji13 Feb
3
The Overmolding Design Guide You Must Never Forget
Oluwafemi Adedeji13 Feb
4
What You Need to Know About the Overmolding Process
Paul Richard05 Feb