Manufacturing Capabilities
CNC Machining
CNC milling (3, 4, 5 axis), CNC turning (Lathe), Post-processing
CNC Machining Materials
Aluminum
2024, 3003, 5052, 5083, 6061, 6061-T651, 6063, 6082, 7075, ADC12 (A380)
Stainless steel
SUS201, SUS301, SUS303, SUS304, SUS316, SUS316L, SUS401, SUS410, SUS416, SUS416L, SUS420, SUS430, SUS431, SUS440C, SUS630 / 17-4PH
Steel
1008, 1018, 1020, 1025, 1045 (45 #), 11Smn30, 1215, 4041, 40Cr, 4130, 4137, 4140, 42 Crmo, 4340, 4J36 Alloy, 5140, 5160, 52100 Bearing, 60Si2Mn, 65Mn, 718H, A2 Tool, A36, C3600 , Class 8 Gray iron, Cr12Mov, D2 mould, DC-01 Cold rolled, EN16T, EN3B, EN8T, G10 / FR-4, Galvanized / SGCC / SECC, H13, Inconel, Invar 36, NAK80, P20, S136, S7, S7 Tool, SCM440 (40CrMo) alloy, SK5, SKD11, SKD61, SKH51, SKS3, ST37 (Q235), ZGmn13-5
Brass & Copper
260, 2680, 360, 385, CAD260, H59, H62, Antimony copper, Beryllium copper, Chromium zirconium copper, Common Copper , Copper 101, Copper for EDM, Tungsten copper
Plastics
ABS, ABS+PC, PC, PC+GF30, PMMA, POM, PA, PA6+GF15, PEEK, PEEK+30%GF, PE, HDPE, Bakelite, CPVC, EPP, FR-4, HIPS, LDPE, PAI, PBT, PBT+GF30, PEI, PET, PET+GF30, PETG, PP, PP+GF30, PPA, PPS, PPS+GF40, PPSU, PS, PTFE, PVC, PVDF, UPE
Others
Bronze, Titanium, Magnesium, Zinc
Manufacturing Standards
CNC Milling
Maximum part size
Stainless steel, tool steel, alloy steel & mild steel | 2000 x 1500 x 200 mm 78.7 x 59.0 x 7.8 in |
Aluminum, copper & brass | 1500 x 800 x 500 mm 59.0 x 31.4 x 27.5 in |
Plastics | 1200 x 800 x 500 mm 47.2 x 31.4 x 19.6 in |
Minimum feature size
All materials | Ø 0.50 mm | Ø 0.019 in |
Maximum part size
All materials | 650 x 650 x 300 mm | 25.5 x 25.5 x 11.8 in |
Minimum feature size
All materials | Ø 0.50 mm | Ø 0.019 in |
CNC Turning
Maximum dimension limitations
Part diameter | 431 mm | 17 in |
Part length | 990 mm | 39 in |
Swing over the carriage | 350 mm | 13.7 in |
Spindle through-hole | 40 mm | 1.5 in |
Speed | 1700RPM | |
Motor power | 640W |
Sheet Metal
Laser cutting, CNC punching, Water jet, Plasma cutting, Sheet metal bending, Sheet metal welding, Post-processing
Sheet Metal Materials
Aluminium
2024, 5052, 6061, 6061-T651
Stainless steel
PP631 / 17-7PH, SUS201, SUS301, SUS303, SUS304, SUS316, SUS316L, SUS401, SUS410, SUS416, SUS416L, SUS420, SUS430, SUS431, SUS440C, SUS630 / 17-4PH
Steel
1008, 1018, 1020, 1025, 1045 (45 #), 11Smn30, 1215, 4041, 40Cr, 4130, 4137, 4140, 42 Crmo, G10 / FR-4, S7 Tool, SCM440 (40CrMo) alloy, SKS3
Brass
260, 2680, 360, 385, CAD260, H59, H62
Copper
Antimony copper, Beryllium copper, Chromium zirconium copper, Common Copper , Copper 101, Copper for EDM, Tungsten copper
Bronze
bronze plate, Phosphor bronze (QSn6.5-0.1), Tin bronze, Tin phosphor bronze
Manufacturing Standards
Highly accurate, capable of cutting dissimilar thicknesses at the same time, low heat-affected zone, and able to cut hole diameters under half a material thickness.
– Cutting area
Up to 4000 x 6000 mm
– Maximum material thickness
Carbon steel | Stainless steel | Aluminum | Copper alloys |
<20 mm | <20 mm | <10 mm | <10 mm |
– Laser sources
Up to 6 kW
– Repeatability
Ps: +/- 0.05 mm
– Positioning accuracy
Pa: +/- 0.1 mm
Pushes material through a press into the desired shape, creating either a hole or an indentation.
– Maximum thickness
Aluminum | Carbon steel | Stainless steel |
3.0 mm | 2.5 mm | 2.0 mm |
– Hole capacity
Up to 50mm
Highly accurate, versatile, and durable, capable of cutting up to 10” thick with abrasive additive in the high-pressure fluid stream.
– Maximum cutting area
Up to 3000 x 6000 mm
– Maximum material thickness
Up to 300 mm
Offers the variable material cutting capability of lasers with a significantly lower capital cost.
– Cutting area
Up to 4000 x 6000 mm
– Maximum material thickness
Carbon steel | Stainless steel | Aluminum |
50mm | 50mm | 40mm |
Forms generally uniform-thickness material to a specific shape or angle along a straight axis.
– Metal folding capacity
Up to 200 tons
– Maximum bending length
Up to 4000 mm
– Maximum thickness
Up to 20 mm
Melts the base materials and fuses it together, forming a metallurgical bond that joins the metals together.
Size Limiations
Forming and bending
+/- 0.020”
Bend to hole or feature
+/- 0.010”
Linear dimensions excluding locations to bends
+/- 0.005”
Diameters with inserts
+0.003/-0
Angularity
+/- 2 degrees
Surface roughness (blank material)
Ra 125 uin max
Surface roughness (timesave)
Ra 100 uin max
Injection Molding
Rapid tooling, Production tooling, Family molds, Multi-cavity molds, Over-molding
Injection Molding Materials
Plastics
ABS, ABS+PC, PC, PC+GF30, PMMA, POM, PA, PA6+GF15, PEEK, PEEK+30%GF, PE, HDPE, Bakelite, CPVC, EPP, FR-4, HIPS, LDPE, PAI, PBT, PBT+GF30, PEI, PET, PET+GF30, PETG, PP, PP+GF30, PPA, PPS, PPS+GF40, PPSU, PS, PTFE, PVC, PVDF, UPE
Additives and fibers
UV absorbers, Flame retardants, Plasticizers, Colorants, Carbon fibers, Glass fibers
Manufacturing Standards
Part size (mm) | Precision tolerance | Ordinary mold tolerance |
1~22 | ±0.06~0.09 | ±0.08~0.13 |
22~70 | ±0.11~0.17 | ±0.14~0.24 |
70~160 | ±0.20~0.29 | ±0.30~0.43 |
160~250 | ±0.36~0.44 | ±0.51~0.68 |
250~315 | ±0.44~0.55 | ±0.68~0.85 |
315~500 | ±0.70~0.90 | ±1.08~1.38 |
500~1000 | ±1.20~1.90 | ±1.83~2.90 |
1000~1400 | ±2.30~2.65 | ±3.50~4.05 |
1400~2000 | ±3.05~3.80 | ±4.65~5.80 |
3D Printing
SLA, SLS, Polyjet, FDM
Processes, Applications and Materials
Filament
ABS, Nylon, PLA, Resin
Manufacturing Standards
Compatible with a broad range of materials and used for prototyping or end-use production, FDM extrudes melted filament through a nozzle, building the part layer by layer.
– Maximum build size
Up to 500 x 500 x 500 mm (19.68” x 19.68” x 19.68”)
– Lead time
From 3 business days
– Dimensional accuracy
± 0.5% with a lower limit of ± 0.15 mm (± 0.006″)
– Layer height
100-300 μm
– Infill
20-100%
Sterolithography (SLA) produces parts layer by layer, using light to crosslink monomers and oligomers to form rigid polymers photochemically. SLA is used to make marketing samples, packaging mock-ups, and non-functional conceptual samples.
– Maximum build size
Up to 145 × 145 × 175 mm (5.7″ x 5.7″ x 6.8″)
– Lead time
From 6 business days
– Dimensional accuracy
± 0.5% with a lower limit of ± 0.15 mm (± 0.006″)
– Layer height
25-100 um
Jets layers of liquid photopolymer onto build surface and cured to harden. PolyJet is also capable of multi-color and multi-material 3D printing.
– Maximum build size
Up to 380 x 250 x 200 (19.46” x 9.84” x 7.87”)
– Standard lead time
9 business days
– Dimensional accuracy
± 0.1% with a lower limit of ± 0.1 mm (± 0.004″)
– Layer height
32 μm
A 3D printing process that uses a computer-controlled laser to sinter a powdered material (such as Nylon or polyamide) layer by layer. The process produces accurate, high-quality parts that require minimal post-processing and supports.
– Maximum build size
Up to 300 x 300 x 300 mm (11.8” x 11.8” x 11.8”)
– Lead time
From 6 business days
– Dimensional accuracy
± 0.3% with a lower limit of ± 0.3 mm (± 0.012”)
– Layer thickness
100 μm
Surface Finishing Capabilities
Anodizing improves corrosion resistance, enhancing wear resistance and hardness, and protecting the metal surface. Widely used in mechanical parts, aircraft, and automobile parts, precision instruments, etc.
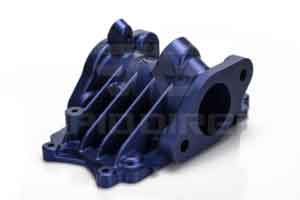
Electroplating can be functional, decorative or corrosion-related. Many industries use the process, including the automotive sector, in which chrome-plating of steel automobile parts is common.
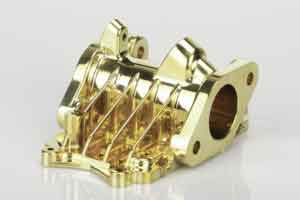
Bead blasting results in parts with a smooth surface with a matte texture. Used mainly for visual applications and can be followed by other surface treatments.
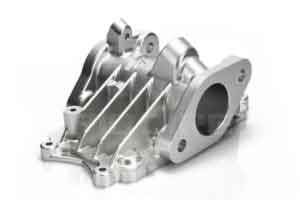
Polishing is the process of creating a smooth and shiny surface, either through physical rubbing of the part or by chemical interference. The process produces a surface with significant specular reflection, but in some materials is able to reduce diffuse reflection.
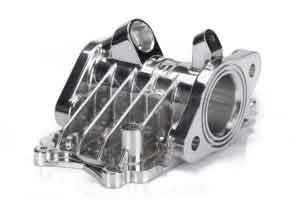
Brushing is a surface treatment process in which abrasive belts are used to draw traces on the surface of a material, usually for aesthetic purposes. Most commonly applied to aluminum.
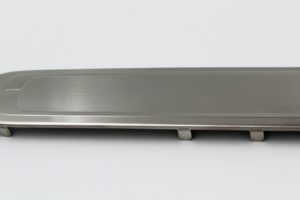
Powder coating forms a durable, wear resistant and corrosion resistant layer on the surface of parts. Powder coating can be used to apply colors to parts and is compatible with any metal.
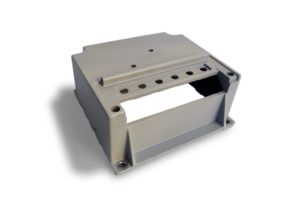
Painting the surface of a part improves its aesthetic appearance and can provide brand recognition to consumers. In addition, painting can have a protective effect on parts.
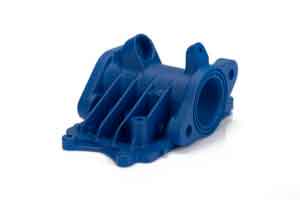
A grade finishes are made using a diamond buffing process and yield shiny and glossy surfaces.
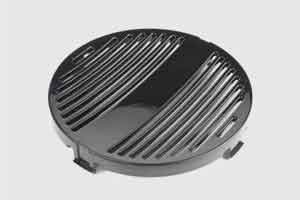
B grade finishes use grit sandpaper to produce parts with a slightly rougher finish than grade A parts. Products that undergo B grade finishing have a matte surface texture.
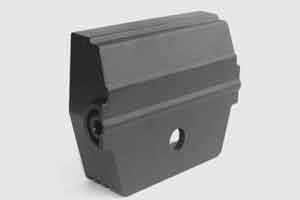
C grade finishes use grit sanding stones to produce a rough, uneven surface. Products that undergo C grade finishing have a matte surface texture.
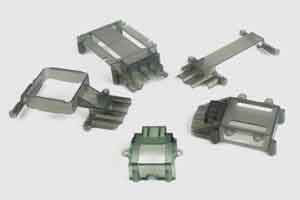
D grade finishes use grit and dry glass beads or oxide to produce a very rough textured finish. Depending on the type of material used, products can have a satin or dull finish.
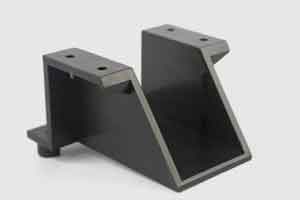
Screen printing is a printing technique where a mesh is used to transfer ink onto a substrate, except in areas made impermeable to the ink by a blocking stencil.
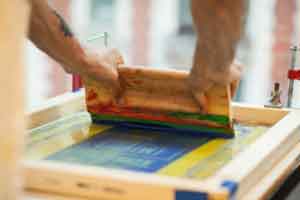
Quality Reports & Certifications
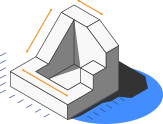
Full Dimensional Inspection Report
For every order on our platform, we provide a full dimensional inspection report on customers’ request. Dimensions are verified using a precision measuring instrument (caliper or gauge) and with a Coordinate Measuring Machine when required. The report includes:
- Quantity of parts
- Critical dimensions
- Threads and tolerances
- Thicknesses and depths
- Part appearance
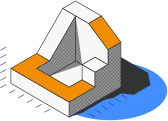
Material certification
On the request of customers, we can provide the certification of the material used in the manufacturing process. The report comes from the raw material manufacturer and usually includes:
- Material heat number
- Material grade
- Material dimensions
- Mechanical properties
- Chemical analysis
- Heat treatment (if applicable)
Get Your Parts Into Production Today
Only 4 simple steps to complete your project. Follow the instruction and give it a try!
Upload Files
Get Quotation
Place an Order
Start Production