Introduction
Aluminum is a versatile material with properties that make it ideal for CNC machining. Aluminum has excellent machinability, welding and electroplating properties as well as good corrosion resistance. The metal is also characterized by a high strength-to-weight ratio and good temperature resistance. After machining, aluminum has a low risk of deformation or defects and is easy to polish and color.
Because of these properties, aluminum is a broadly used metal in many industries, including automotive, defense, aerospace, transportation, construction, packaging, electronics, consumer goods and more.
Aluminum Subtypes
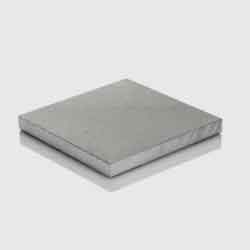
Aluminum 6061-T6
Aluminum 6061 is one of the most commonly used aluminum alloys in the world. It is characterized by its high strength and corrosion resistance as well as its excellent machinability and weldability. In terms of applications, the material is used for many things, from pipe fittings to aerospace-grade parts.
Tensile Strength | Elongation | Hardness | Maximum Temp | Manufacturing Process |
45 KSI | 17% | 95 HRB | 1080 °F – 1206 °F | Sheet Metal Fabrication, CNC Milling, CNC Turning |
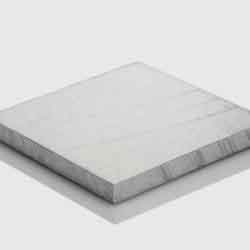
Aluminum 7075-T6
Aluminum 7075 is a high strength aluminum alloy that was originally created for the aerospace industry, specifically, for aircraft parts. Today, Aluminum 7075 is used to produce a range of high-stress components, such as keys, gears, rock climbing and bicycle parts.The aluminum alloy is commonly used instead of Aluminum 2024 as it has similar performance and superior strength.
Tensile Strength | Elongation | Hardness | Maximum Temp | Manufacturing Process |
74-78 KSI | 5-8% | 150 HRB | 890 F | CNC Milling, CNC Turning |
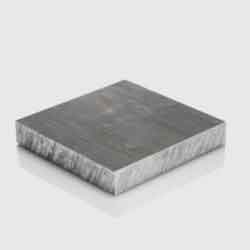
Aluminum 6082
Aluminum 6082 is a common aluminum alloy known for its medium strength and excellent corrosion resistance. In the Aluminum 6000 series, the 6082 alloy has the highest strength and is thus considered a structural alloy. The alloy is commonly used for applications in transport, general engineering, bridges and more.
Tensile Strength | Elongation | Hardness | Maximum Temp | Manufacturing Process |
270 Min MPa | 6 Min % | 95 HRB | 1070 – 1200 ºF | CNC Milling, CNC Turning |
Surface Finish
Anodizing
Anodizing improves corrosion resistance, enhancing wear resistance and hardness, and protecting the metal surface. Widely used in mechanical parts, aircraft, and automobile parts, precision instruments, etc.
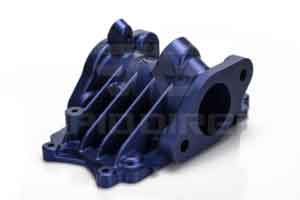
Bead blasting
Bead blasting results in parts with a smooth surface with a matte texture. Used mainly for visual applications and can be followed by other surface treatments.
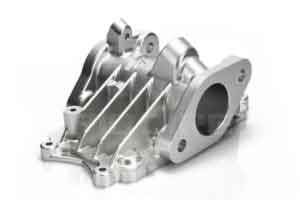
Brushing
Brushing is a surface treatment process in which abrasive belts are used to draw traces on the surface of a material, usually for aesthetic purposes. Most commonly applied to aluminum.
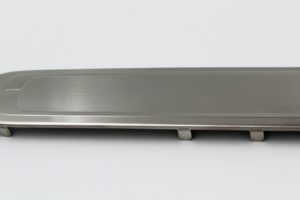
Electroplating
Electroplating can be functional, decorative or corrosion-related. Many industries use the process, including the automotive sector, in which chrome-plating of steel automobile parts is common.
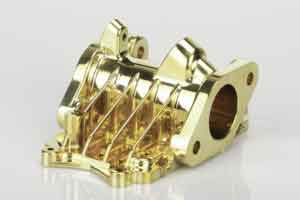
Painting
Painting the surface of a part improves its aesthetic appearance and can provide brand recognition to consumers. In addition, painting can have a protective effect on parts.
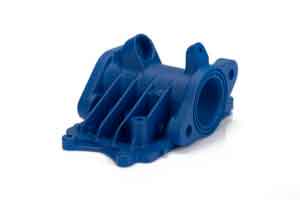
Polishing
Polishing is the process of creating a smooth and shiny surface, either through physical rubbing of the part or by chemical interference. The process produces a surface with significant specular reflection, but in some materials is able to reduce diffuse reflection.
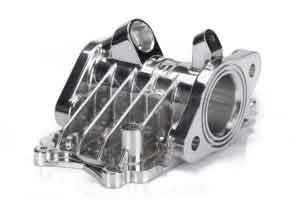
Powder Coating
Powder coating forms a durable, wear resistant and corrosion resistant layer on the surface of parts. Powder coating can be used to apply colors to parts and is compatible with any metal.
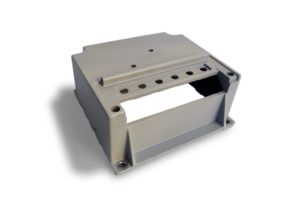
Manufacturability
Tolerance
- Standard: (+/-) 125 µm -Achievable: (+/-) 100 µm , (+/-) 50 µm
Wall Thickness
- The minimum wall thickness should be at least 1 mm for machined parts. - 2 mm is suggested for better strength and 2.5 mm for a rigid wall.
Pocket depth
- Pocket depth should be up to 3 times the diameter of the end mill
Engraving
- Engraving is preferable to embossing - For the clear, legible text consider fonts such as Arial or Gothic - Design letter strands with a width of at least 2 mm
Internal Radii
- The minimum internal radii possible is 1 mm - In general, internal radii dimensions depend on the depth of pocket being milled
Holes
- Use standard drill bit sizes - Minimum of 1 mm in diameter
Threads
- Use standard metric inserts - Smallest threaded insert possible is M2
Design Recommendations
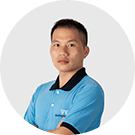
Get Your Parts Into Production Today
Only 4 simple steps to complete your project. Follow the instruction and give it a try!
Upload Files
Get Quotation
Place an Order
Start Production
Latest news and stories
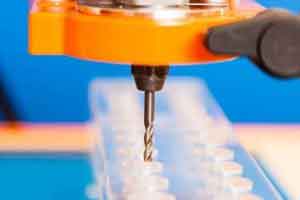
Understanding Plastic Fabrication Processes: A Complete Guide
Plastics are versatile materials with plenty of polymer options. They are among the most common […]
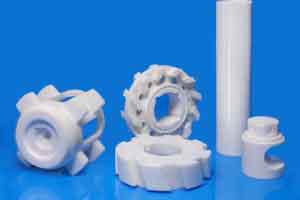
Ceramic CNC Machining: Another Option for Custom Manufacturing
It could be quite a cumbersome task to choose the best material for your manufacturing […]
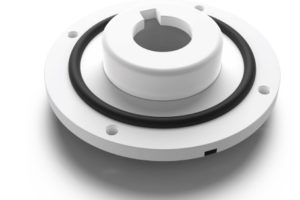
The Overmolding Design Guide You Must Never Forget
Overmolding is an injection molding process where you cast a layer of resin (usually a […]