CNC Machining Applications in Medical Industry
Dec 13, 2019
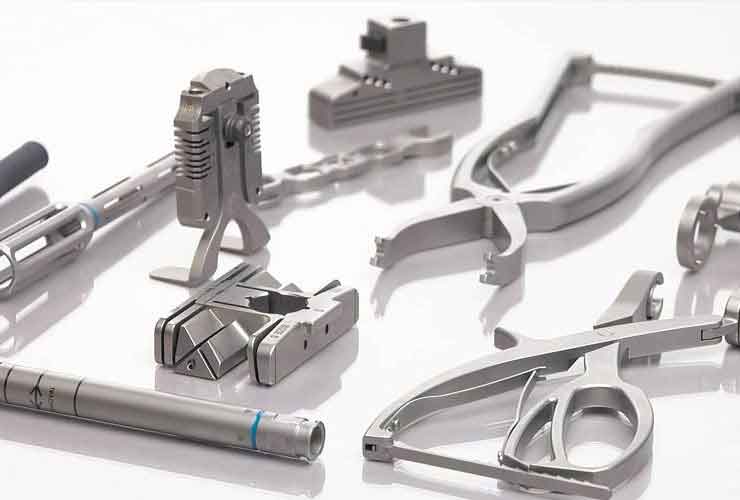
Thanks to its precision, speed and material versatility, CNC machining is a vitally important manufacturing process for the medical industry. From surgical tools to bedside monitoring devices to hip implants, machined parts can be found throughout the world of healthcare.
Many machined medical parts are made by specialist medical machine shops. These shops must be capable of making parts with extremely tight tolerances and may have a focus on bio-safe and biocompatible materials. Crucially, they must also be capable of making parts that meet international and governmental standards, such as those set by the American Food and Drug Administration (FDA).
That being said, any machine shop capable of precision machining has the technical resources to make medical parts. Items like bodily implants require exceptionally tight tolerances and therefore require precision machining, but medical-grade materials are available to all machine shops.
This article discusses the many ways in which CNC machining can be used in the medical industry.
Who can make CNC machined medical parts?
Making machined parts for the medical industry is not like making parts for consumer goods. Whereas most ordinary metal parts must meet ISO 9001 quality management requirements, medical parts must meet further standards.
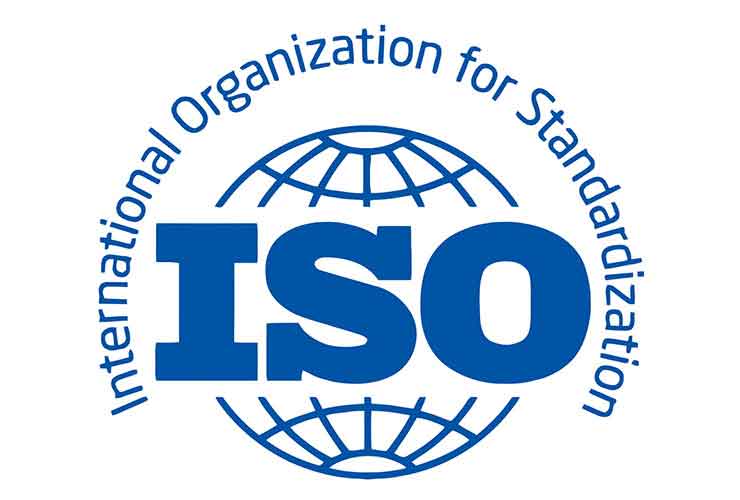
According to the International Standards Organization, companies involved in the design, development, production, storage, distribution, installation or servicing of medical parts must demonstrate their “ability to provide medical devices and related services that consistently meet customer and applicable regulatory requirements.”
The standard used to measure that ability is ISO 13485, which is recognized by regulators such as the FDA.
Requirements for medical CNC machining
Besides meeting standards and obtaining certifications, CNC machine shops must take other steps if they are to successfully machine medical parts. After all, human lives may depend on the success or failure of these machined components.
Basic requirements for medical CNC machining include:
- Precision machining to tight tolerances (as tight as 0.0001” inches for some parts)
- 4-axis and 5-axis machining for complex geometries
- Ultra-high level of cleanliness, especially for an implant manufacturer
- A wide material selection that includes stainless steel and medical-grade plastics such as PEEK
- High-level surface finishing capabilities
1. Machined medical implants
One of the most important uses of medical CNC machining is the production of bodily implants such as knee implants and hip replacements.
Patient-specific implants are suitable for CNC machining. CNC turnaround times are short and there are no tooling costs, which makes the process suitable for one-off, tailor-made parts as opposed to mass-produced parts.
Implants are commonly machined from metals like titanium and plastics like PEEK. These materials don’t just need to be strong and durable: they also need to be biocompatible. They must not corrode and break down within the human body, since this would pose severe risks to a patient’s health.
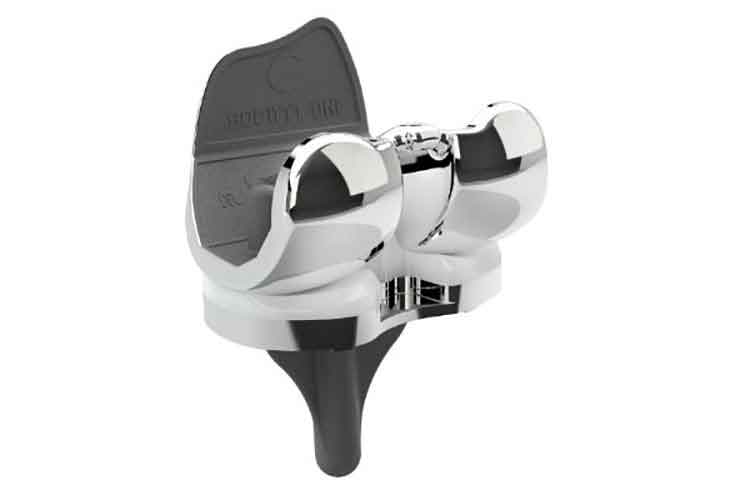
Because there is so much at stake with medical implants, machining can be difficult. Many suitable materials are difficult to machine without heat buildup, and coolant is often prohibited due to risk of contamination.
3D printing is also becoming a popular technology for the production of one-off medical implants.
Common machined implants
- Hip implants
- Spine implants
- Knee implants
Common materials for machined implants
- Titanium alloys such as Ti6Al4V
- Cobalt-chrome alloys such as CoCr28Mo6
- Stainless steels (for temporary implants)
- Polyether ether ketone (PEEK)
2. Machined surgical instruments
In addition to the creation of bodily implants, CNC machining can be used to create surgical instruments used by medical professionals during operations. These metal components may include surgical scissors, biopsy tubes, blade handles, cutters, saws, forceps, implant holders, clamps, spacers, plate benders and more.
These CNC machined surgical tools and instruments must be made with care and precision, and are subject to extra safety requirements such as ease of sterilization.
Medical device manufacturers may favor CNC machining for these surgical tools because the demand for precision is high and because some tools and instruments must be manufactured in small production runs. Some are even fabricated for individual patients. Machined parts can also be subjected to comprehensive surface finishing treatments to ensure there are no surface defects.
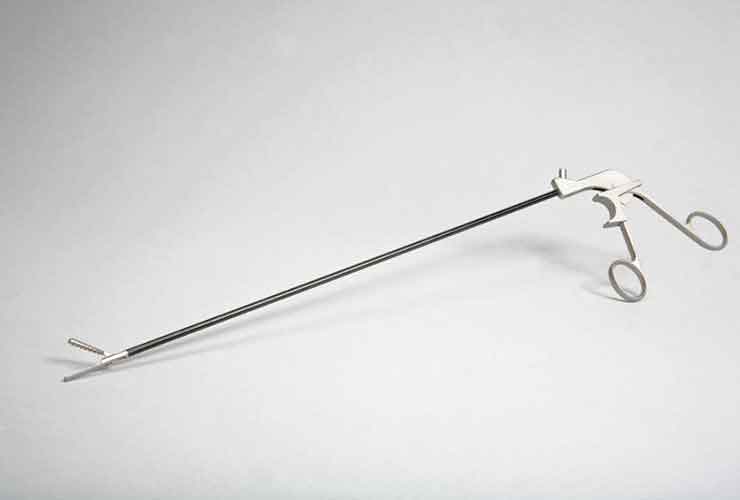
Electrical discharge machining (EDM) is another machining option for medical device manufacturers since the technology can achieve exceptionally tight tolerances.
Common machined surgical instruments
- Handles
- Cutters
- Saws
- Forceps
- Holders
- Clamps
- Spacers
Common materials for surgical instruments
- Stainless steels, particularly surgical steel (AISI 316L)
- Titanium alloys
3. Machined parts for electronic medical equipment
Surgical instruments are simple devices often consisting of one or two metal parts. But CNC machines can be used to create parts for much more complex pieces of equipment. Think heart rate monitors, MRI scanners and X-ray machines.
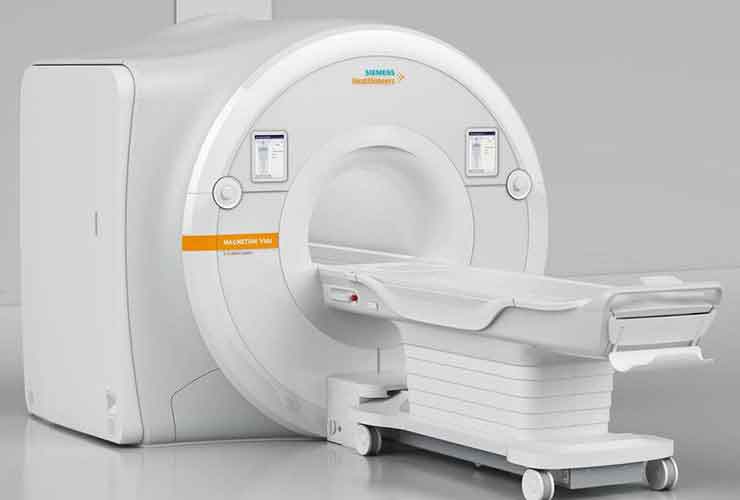
These expensive pieces of equipment may comprise hundreds or thousands of individual parts, and many of these parts can be fabricated with CNC machines.
Machined equipment parts can include small components like switches, buttons and levers, and larger items such as to monitor housings.
All of these components must be high standards in order to eliminate any chance of machine failure, especially since medical equipment is regularly wheeled from room to room around a hospital.
However, unlike implants and surgical tools, these parts may not need to be biocompatible or bio-safe, since they may never make direct contact with a patient. As such, a much wider variety of CNC machining materials can be used.
Electronic medical equipment commonly fitted with machined parts
- Ultrasound equipment
- MRI scanners
- CT scanners
- Diagnostic equipment
- Monitors
- Lighting
4. Micromachining
Medicine is a gigantic industry, but medical device manufacturers must sometimes make incredibly small parts. For implantable devices, exploratory surgical tools and more, there is a requirement for very small components that must be made with precise manufacturing technologies. Feature sizes of these components may be well under 50 microns.
Within the medical industry, the practice of micromachining may be used for the production of stents, catheters, pacemaker components, drug delivery systems, ophthalmic devices, miniature screws for implants and devices, tiny plastic tubes and more.

Of course, not all machining centers are suitable for micromachining, and extremely fine cutting tools must be used to meet tight tolerances on tiny parts. EDM and wire EDM may be used for certain components.
Common micromachined medical parts
- Stents
- Catheters
- Pacemaker parts
- Drug delivery systems
- Screws
- Tubes
Share on social media...
Get Your Parts Into Production Today
Only 4 simple steps to complete your project. Follow the instruction and give it a try!
Upload Files
Get Quotation
Place an Order
Start Production
Latest news and stories
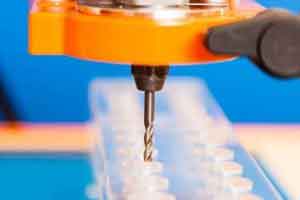
Understanding Plastic Fabrication Processes: A Complete Guide
Plastics are versatile materials with plenty of polymer options. They are among the most common […]
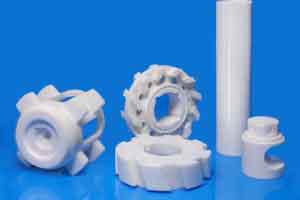
Ceramic CNC Machining: Another Option for Custom Manufacturing
It could be quite a cumbersome task to choose the best material for your manufacturing […]
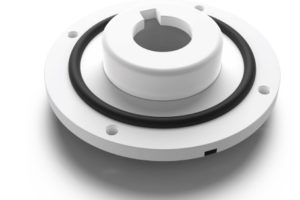
The Overmolding Design Guide You Must Never Forget
Overmolding is an injection molding process where you cast a layer of resin (usually a […]