CNC Machining in the Electronics Industry
Dec 25, 2019
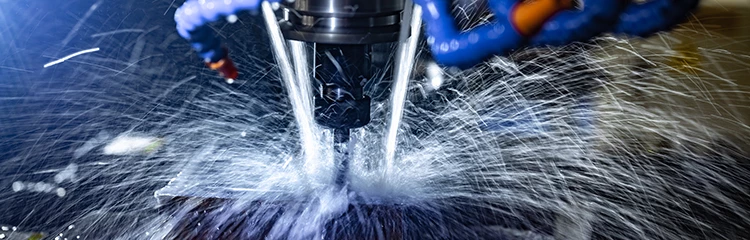
CNC machining is the manufacturing process behind many electronic devices, from PCBs to laptop housings. This article looks at the applications of CNC in electronics industries.
Electronic devices are ubiquitous in personal and professional life. And from family-friendly iPads to industrial monitoring systems, many electronic devices can be manufactured with the help of CNC machining.
CNC is suitable for a range of materials, and its ultra-high level of precision makes it suitable for small and complex parts that can form part of a larger electronic assembly, or for larger components like the aluminum shell of a laptop. Moreover, the tight tolerances afforded by machining centers mean that machined parts are often suitable for end-use after minimal post-processing.
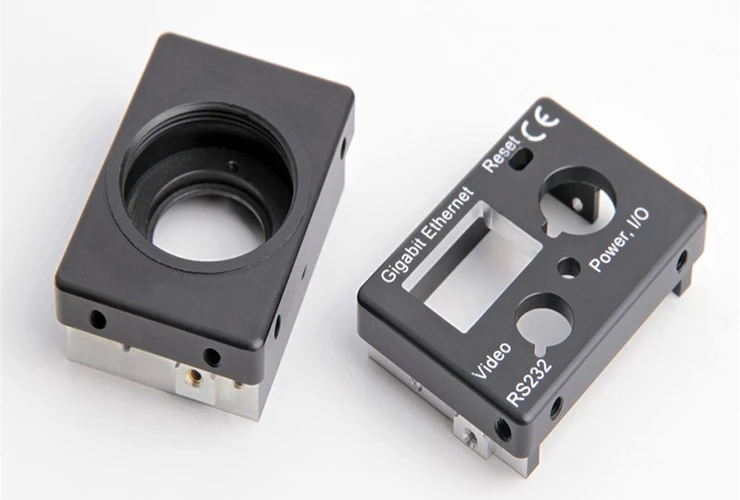
The high reliability of CNC machining means that electronics manufacturers use the technology for small and large production runs of electronic parts, in addition to the prototyping of various components.
This article looks at how CNC machining is commonly utilized in the electronics industry.
Overview of CNC machining electronics
CNC machining is a widely used manufacturing process for metal and plastic parts. It is known for its precision, repeatability, and ability to produce strong and durable parts from extruded blocks of material.
It can also be used to make parts in a short timeframe, since no tooling is required, but produces parts of a higher quality than other short-turnaround technologies like 3D printing.
For all of these reasons, CNC machining is highly suited to the prototyping and production of components for electronic devices, from simple handheld devices to expensive pieces of industrial equipment.
Components large and small, simple and complex can be CNC machined, and these are just a few of the most widely made.
1. CNC machined Printed Circuit Boards (PCBs)
PCBs are an essential feature of almost all electronic products. Used to electrically connect the various parts of an electronic device, PCBs use conductive tracks and other features and are usually made by a process of etching. The conductive features of a PCB are generally made from copper, while the flat substrate underneath is made from a non-conductive material.
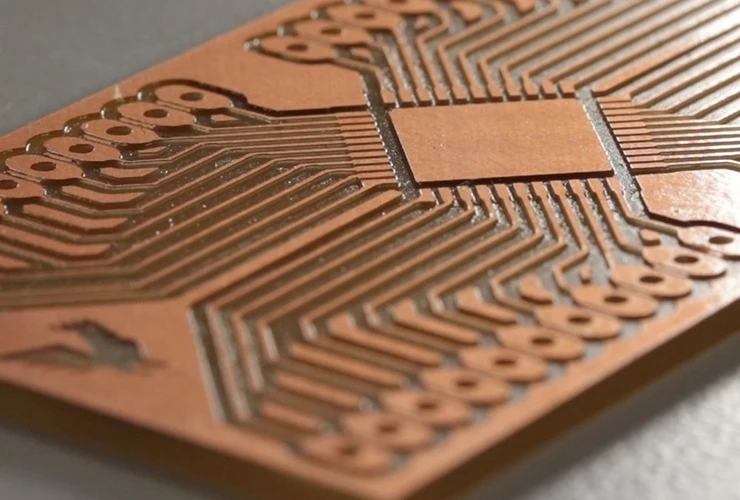
Etching is the most widely used method for making PCBs, but it is not always the most practical: etching requires hazardous chemicals, so it should not be used in offices and other non-industrial workspaces.
That’s where CNC machining comes in. Like etching, CNC machining can be used to carve out functional PCBs. However, machining does not require hazardous chemicals and is, therefore, a safer option for certain work environments.
Advantages of machined PCBs:
- Unlike etching, CNC machining doesn’t require chemicals
- Can be made in-house, ideal for prototyping
- Fast turnaround
- Easy to design and execute with CAD/CAM software
- Brings multiple operations together under one machine
2. CNC machined electronics casings and enclosures
CNC machines can be used to create the compact PCBs at the heart of an electronic device, but they can also be used to manufacture the plastic or metal enclosures that function as a device’s exterior shell.
These casings and enclosures can also be made using die casting or other tooling-based processes, but CNC machining has the advantage of high precision, tight tolerances and — crucially for consumer goods casings — minimal surface defects.
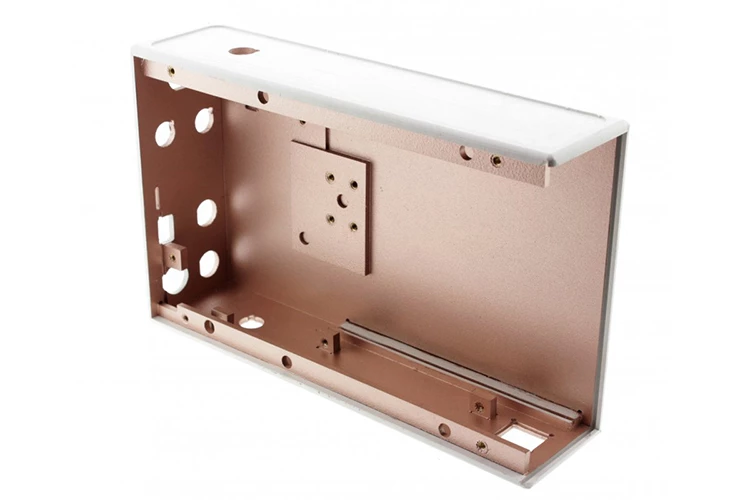
Electronic devices like smartphones, digital cameras, and laptops all require aesthetic and durable casings that contain the devices’ circuitry and hardware. Many manufacturers use molding processes to make these parts, but others favor CNC machining for complex designs and a more professional finish.
Advantages of machined enclosures:
- Milled from solid materials like aluminum, resulting in high strength
- Range of surface finishes including anodization
- Engraving possible
- Fast turnaround
- Possible to incorporate threads and other features
3. CNC machined heat sinks
Many electronic devices, including computers, require heat sinks. Heat sinks are passive heat exchangers that take the heat generated by electronic parts and transfer it into the air or a liquid coolant, dissipating the heat from the device to ensure it does not cease to function through overheating.
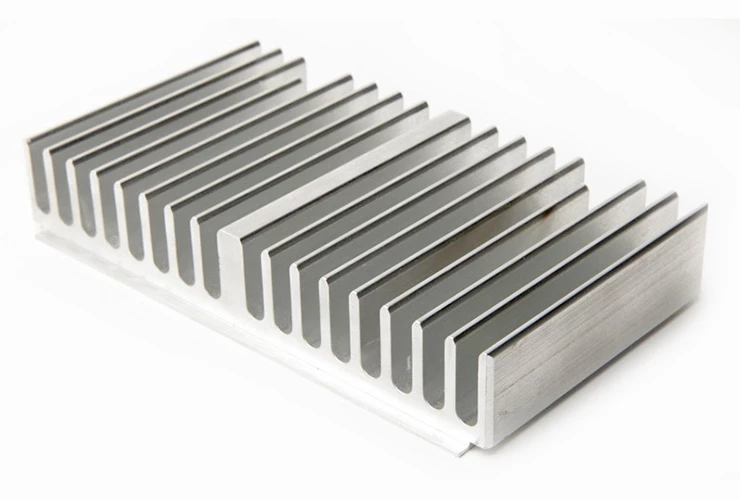
CNC machines can be used to make these heat sinks, even though the components can sometimes be very small in size. In fact, CNC machines offer specific advantages in heat sink construction, such as the ability to fabricate unusual fin patterns.
Most machined heat sinks are made from aluminum or copper alloys, but other possible materials include stainless steel and Inconel, and CNC machining of heat sinks is often favored for short-run production or rapid prototyping of electronic devices.
Advantages of machined heat sinks:
- Flexibility with fin patterns and other features
- Various material options
- Fast turnaround
- Exceptionally tight tolerances suitable for miniature electronic devices
- Ideal for prototyping and experimentation
4. CNC machined connectors and sockets
Many electronic devices are designed to work in conjunction with other devices. Think of a USB keyboard and mouse for a computer, for example, or an electronic musical instrument designed to plug into an amplifier or mixing desk.
These connectable devices require metal connectors and sockets, to which devices or cables can easily be attached.
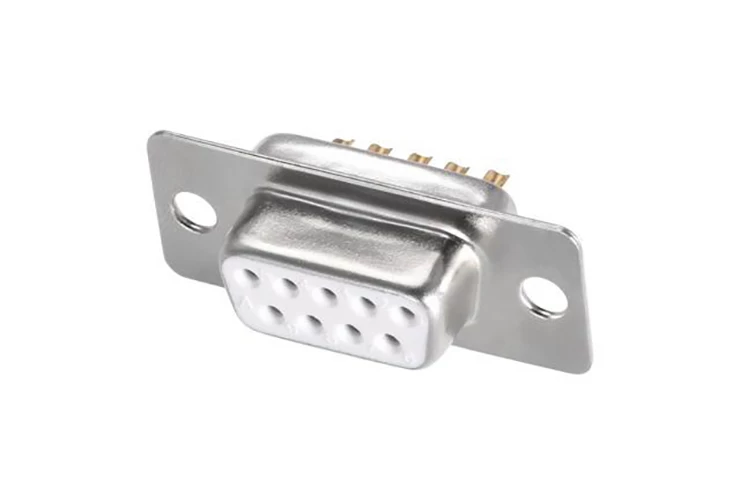
CNC machining plays a big role in the manufacture of these connectors and sockets – the technology is adept at cutting small metal components to very tight tolerances. And if the pins of a connector or the circumference of a socket do not meet required tolerances, the connection between devices may fail.
Machined parts in this category include sockets, contacts, sleeves, hoods, and pins, many of which are suitable for machining with copper alloys.
Advantages of machined connectors and sockets include:
- Tight tolerances
- Can be made for one-off devices or short production runs
- Fast turnaround
- CNC machines can process highly conductive metals
Share on social media...
Get Your Parts Into Production Today
Only 4 simple steps to complete your project. Follow the instruction and give it a try!
Upload Files
Get Quotation
Place an Order
Start Production
Latest news and stories
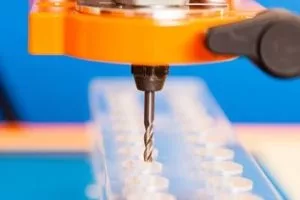
Understanding Plastic Fabrication Processes: A Complete Guide
Plastics are versatile materials with plenty of polymer options. They are among the most common […]
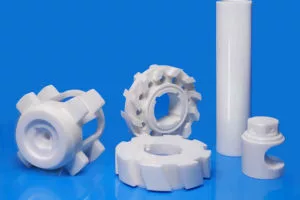
Ceramic CNC Machining: Another Option for Custom Manufacturing
It could be quite a cumbersome task to choose the best material for your manufacturing […]
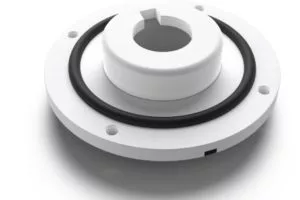
The Overmolding Design Guide You Must Never Forget
Overmolding is an injection molding process where you cast a layer of resin (usually a […]