Finishing options for injection molding
Jul 09, 2020
Injection molding is an invaluable process for creating plastic parts: it’s fast, cheap and can be used to create huge volumes of identical objects.
But one of the biggest advantages of injection molding is the natural surface finish of molded parts. Even without any post-processing treatment, molded parts have a smooth surface finish suitable for many end uses. And the simple pre-coloration of plastic pellets means that molded parts sometimes don’t require any painting or tinting after fabrication.
Nonetheless, the vast range of applications for injection molding means that injection molded parts often require some form of surface finishing — whether that’s a quick polish or something more comprehensive. Some companies will demand a very smooth finish for aesthetic reasons; others will prefer a high level of roughness to extend a part’s lifespan.
This guide describes some of the available surface finishing options for injection molded parts, with advice for specific materials.
Factors that affect injection molding surface finish
Treating molded parts with a dedicated finishing process is the best way to achieve maximum control over the texture of a plastic part. However, there are steps that can be taken to manipulate the surface finish of a part even before the molding cycle begins.
Tooling
The mold itself plays a big role in the surface finish of injection molded parts. Various metals can be used to create the mold, but tool steels and aluminums remain the most common options, and these two metals have a very different effect on molded plastic parts.
In general, the very smoothest surface finishes can only be achieved using molds made from hard tool steel. If parts have an aesthetic purpose that demands a very low level of surface roughness, starting with a steel mold may be the best way to go.
Material choice
Not all injection molding materials can be given the same surface finishes. Some plastics are more amenable to smooth finishes, while some are easier to roughen up for a more textured finish.
Additionally, certain material additives like filler and colors may affect the surface finish of a molded part.
This table shows the suitability of certain injection molding materials for specific surface finishes:
Grade | Effective finish | Suitable materials |
A | Glossy | Acrylic, PC |
B | Semi-glossy | ABS, HDPE, Nylon, PP, Polystyrene |
C | Matte | ABS, HDPE, Nylon, PP, Polystyrene |
D | Very rough | ABS, HDPE, Nylon, PP, Polystyrene, TPU |
Process variables
Factors such as injection speed and temperature can affect the surface finish of injection molded parts. Glossier surfaces with fewer weld lines can be achieved by using a fast injection speed and high melt temperature.
Injection molding surface finishing options
Surface finishing procedures for injection molding can be used to either increase or decrease the roughness of a part. Glossier finishes may be preferred for aesthetic parts such as toys, while rougher parts may be preferred for certain mechanical parts or simply to reduce overall costs.
Parts can also be left as-machined, which may be perfectly acceptable for non-aesthetic components or parts that have been made using very hard steel tooling.
Glossy (A)
Min. roughness: 0.012 μm
Injection molded parts can be made glossier using a specialist finishing process such as diamond buff polishing. In this process, a loose abrasive material is applied to a work wheel and applied to the surface of the part with minimal aggression, contributing to the glossiest possible finish.
Not all materials can achieve a glossy finish. Plastics like acrylic and PC can be buffed to a very smooth finish, but it is virtually impossible to apply such a finish to a material like TPU, which has a high resistance to abrasion and is thus also resistant to the buffing process.
Semi-glossy (B)
Min. roughness: 0.05 μm
For parts that require some glossiness, a B-grade finish can be applied using grit sandpaper. This process is compatible with a wider range of injection molding plastics and still produces highly aesthetic parts suitable for consumer products and other parts.
Matte (C)
Min. roughness: 0.35 μm
Using grit sanding stones, it is possible to remove machining marks from molded parts without creating a glossy finish. This process is suitable for parts that do not have aesthetic value but which require a consistent surface finish and no noticeable marks or divots.
The stone polishing process can be applied to most injection molding plastics.
Very rough (D)
Min. roughness: 0.80 μm
For parts that require a very rough or textured surface finish — to increase friction for a mechanical purpose, for example — it is possible to apply a rough surface finish using the sandblasting process.
Sandblasting uses compressed air to direct abrasive material against the part with force, roughening its surface.
To learn more about the surface finishing options that China Medical CNC Machining Inc. provides, to view our injection molding service page.
Share on social media...
Get Your Parts Into Production Today
Only 4 simple steps to complete your project. Follow the instruction and give it a try!
Upload Files
Get Quotation
Place an Order
Start Production
Latest news and stories
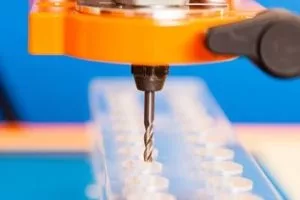
Understanding Plastic Fabrication Processes: A Complete Guide
Plastics are versatile materials with plenty of polymer options. They are among the most common […]
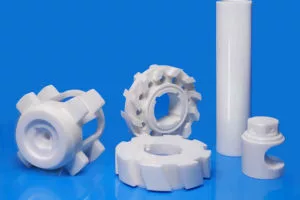
Ceramic CNC Machining: Another Option for Custom Manufacturing
It could be quite a cumbersome task to choose the best material for your manufacturing […]
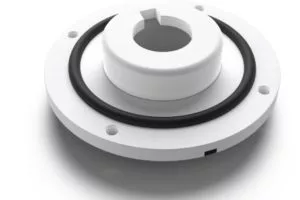
The Overmolding Design Guide You Must Never Forget
Overmolding is an injection molding process where you cast a layer of resin (usually a […]