How to Get the Best CNC Machined Finish for your Products.
Jun 30, 2020
Helpful tips to ensure that your CNC Machined prototypes, end-use parts and mold-making components have the best surface finish possible.
It goes without saying that achieving a high quality finish with CNC machining is of critical importance, especially for end-use parts and mold-making components. As a manufacturing solution, CNC machining is highly sought after because of its ability to produce parts with very tight tolerances. However, metal or plastic components that are milled and machined do not always have the smooth finish needed for certain end-use or molding applications.
To address this, there are a number of post-processing techniques which can be employed to give CNC machined parts the desired professional finish. Moreover, if a high surface quality is a top priority for your products, there are a number of helpful tips that can help to ensure that even your as-milled component is the best it can be.
Knowing what surface finish you need
When working with CNC Machining, professional services such as RapidDirect offer a range of surface finishes to meet the requirements of various applications, whether you are ordering a prototype, a mold or end-use component. Below are the finishing solutions offered by China Medical CNC Machining Inc. for CNC machined components, in order of cost.
As-milled
An as-milled surface finish for CNC machining does not require any post-processing as it simply indicates the part will remain in its machined state. As CNC machining is able to manufacture parts with tight tolerances of up to ± 0.025 mm, as-milled parts usually result in the best dimensional precision.
It should be noted, however, that as-milled parts will be dull and still show tool marks on their surface and thus will not be perfectly smooth. The average surface roughness (Ra) of an as-milled part is about 3.2 μm, though additional smoothing and polishing can reduce the machined texture.
Without smoothing or polishing, an as-milled surface finish should not incur any additional production costs and is thus the most cost-effective solution. An as-milled finish is most suitable for prototypes and jigs and fixtures.
Bead Blasting
Bead blasting consists of shooting small spherical media (such as glass beads) at the surface of a CNC machined part using compressed air. The result of bead blasting is typically a uniformly smooth texture with either a matte or satin finish.
Because the process relies on using small beads to remove incremental amounts of material from the machined part’s surface, it is possible that the post-process can affect the dimensional accuracy of the part (though only slightly). Bead blasting is primarily used for aesthetic applications and products that require good visual qualities.
Powder coating
The powder coating process consists of applying a thin layer of dry polymer powder to the machined part to add strength and wear-resistance. Various layers of powder coating can be applied to parts in order to increase strength, however this might affect the dimensional tolerances of the finished component.
Powder coating is compatible with all machining metals and enables users to choose from a wide variety of color finishes. The post-process can also be combined with bead blasting for a superior smooth finish—ideal for end-use products.
Anodization (Type II and III)
As a post-process, anodization adds a very thin ceramic layer to the surface of metal machined parts which imparts corrosion and wear resistant properties. The anodic coating applied during the electrochemical post-process is also non-conductive, meaning that if conductivity is required, elements of the part should be masked during anodization.
The main advantages of anodizing CNC machined parts are a high aesthetic quality, the ability to dye parts different colors and durability. In terms of applications, anodization is commonly used for engineering parts. When considering anodization for your product, it is also important to remember that it is only applicable for parts made from titanium or aluminum.
Tips for the best as-milled surface finish
If as-milled is your preferred surface finish, there are ways to ensure that your part has the best as-milled surface quality possible. Here are some helpful tips:
Use the right feeds and speeds
Similar to ensuring that dimensional tolerances are met, achieving the right as-milled surface finish depends on using the right milling speeds and feeds. Typically, it is advisable to increase the speed (surface feet per minute, or SFM) and reduce the feed (inch per revolution, or IPR) to achieve the best surface quality.
Use tools specifically for finishing
To achieve the best surface finish for CNC machined parts, one should reserve certain tools specifically for finishing to create a finer surface texture at the end of the production process. Earlier on in the process, a dedicated roughing tool can be used to remove material more rapidly (though with less finesse).
Clear away material chips
Throughout the machining process it is crucial to continuously remove excess material chips that are created in order to avoid them scratching or damaging the part’s surface. By using air blasting at many points in the CNC machining process, excess chips can be blown away to minimize the risk of scratching or surface damage.
Minimize tool deflection and chatter
Another key element in ensuring the best possible surface finish for your as-milled part is to stop the tool from deflecting or chattering, which can both cause a sub-par and inconsistent finish. Minimizing deflection and chatter is achieved by increasing the rigidity of the CNC machine tool.
Minimize run out
In general, it is best to avoid run out when CNC machining, as it results in the tool spinning inaccurately instead of around the ideal axis. This phenomenon can lead to bad surface finishes or even failed parts. Tool choice, tool replacement and a clean machining area all play an important role in minimizing run out.
Share on social media...
Get Your Parts Into Production Today
Only 4 simple steps to complete your project. Follow the instruction and give it a try!
Upload Files
Get Quotation
Place an Order
Start Production
Latest news and stories
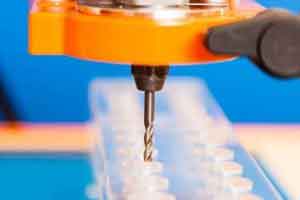
Understanding Plastic Fabrication Processes: A Complete Guide
Plastics are versatile materials with plenty of polymer options. They are among the most common […]
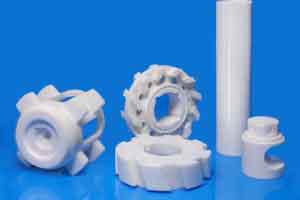
Ceramic CNC Machining: Another Option for Custom Manufacturing
It could be quite a cumbersome task to choose the best material for your manufacturing […]
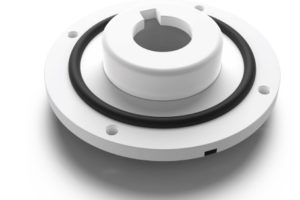
The Overmolding Design Guide You Must Never Forget
Overmolding is an injection molding process where you cast a layer of resin (usually a […]