What is 4-axis and 5-axis CNC machining?
Jun 30, 2020
When selecting a CNC machining service for a project, you’ll hear a lot of talk about axes. CNC machines tend to operate using 3, 4 or 5 axes, with 4-axis and 5-axis CNC machines promoted as the most capable kinds.
But what exactly does 4-axis and 5-axis mean? If a machined part has three dimensions — height, width and depth — then where are those extra two axes coming from? And is it really worthwhile to choose 5-axis machining over cheaper alternatives?
This section of the China Medical CNC Machining Inc. Knowledge Base explains the basic principles of 4-axis and 5-axis CNC machining, and looks at some of the specific ways those extra axes can improve your machining project.
How does a 4-axis or 5-axis CNC machine work?
The alternative
To understand how 4-axis and 5-axis machining works, we first need a clear picture of the alternative: 3-axis machining, which is still the most widely used form of CNC machining today.
Look at a typical 3-axis CNC milling machine. A typical 3-axis CNC mill creates parts by moving its spindle up and down, side to side, and back and forth. The cutting tool, attached to the spindle, cuts pieces away from the workpiece as the spindle moves along those three axes.
For some machined parts, this is a perfectly suitable way to work. However, the 3-axis setup has some severe limitations.
With three-axis machining, the angle of the cutting tool remains uniform, pointing downwards or sideways, which makes it harder to cut away parts of the material in hard-to-reach sections of the workpiece, such as crevices.
Furthermore, it may be necessary to carry out multiple setups for a part: if the part needs machining on several sides, it may need to be taken out of the machine, reoriented, then returned to the machine for further cutting. Naturally, the need for multiple setups can drastically reduce productivity.
Adding rotational axes
A 5-axis CNC machining center is a lot like a three-axis CNC machine, but with some very important features that provide those two extra axes and a great deal more cutting flexibility.
So where do those two extra axes come from?
In a 3-axis CNC machine, the spindle travels along three axes: up and down, side to side, and back and forth, while the workpiece remains stationary on the machine table. With 4-axis and 5-axis machines, the spindle or the table can also rotate.
The implications of this rotation are huge. On a 5-axis CNC machining center, not only can the spindle and cutting tool move along three axes, it can also adjust its orientation (or the orientation of the workpiece) about two of those three axes.
Rotation about the X-axis is called the A-axis, rotation about the Y-axis is called the B-axis, and rotation about the Z-axis is called the C-axis.
Methods of rotation
5-axis machines can utilize any two of these rotational axes, depending on their configuration. (4-axis machines utilize one.)
Some 5-axis machines use a trunnion table, which rocks the workpiece about two axes as the spindle moves along three axes without rotating. Other 5-axis machines use a swivel head — a spindle that moves and rotates while the workpiece remains on a stationary bed.
Regardless of their particular configurations, all 4-axis and 5-axis machines can move their cutting tools in more varied ways, and from a greater number of angles, than 3-axis machines. This allows for more complex machining operations and increased accuracy, and can completely eliminate the need for multiple setups.
What is 3+2-axis CNC machining?
A subtype of 5-axis machining is 3+2-axis machining, which is — as its name suggests — a kind of middle ground between 3-axis and 5-axis. It is nonetheless a rapid and highly effective form of 5-axis machining, and is sometimes known as positional 5-axis machining.
With 3+2-axis machining, the angle of the cutting tool does not change as the spindle or table rotates about the two extra axes. Because of this, the cutting tool is not always perpendicular to the part, which does not always create perfect cuts. (There is, however, a form of 3+2-axis machining called indexed 3+2-axis machining, in which the angle of the cutting tool is manually adjusted between cuts.)
5-axis machining in which the cutting tool can always be kept perpendicular to the part is called continuous or simultaneous 5-axis machining. This process can provide a superior surface finish, and allows access to hard-to-reach areas, but is slower than 3+2-axis machining.
Benefits of 4-axis and 5-axis CNC machining
5-axis CNC machining provides numerous benefits, including increased accuracy, a reduced setup time and the potential for more complex parts.
Other specific advantages depend on the type of machine configuration — whether it a trunnion or swivel head CNC machine, or something else altogether — and whether the machine utilizes 3+2-axis or continuous 5-axis.
In general, 3+2-axis machining offers advantages such as:
- Fast machining
- Easy setup
- Slim chance of tool interference
Continuous 5-axis machining offers advantages such as:
- Excellent surface finish
- Better part access
- Less tool wear
Trunnion setups can be beneficial for:
- Better part access
- Larger volumes
- Greater torque
Swivel head setups can be beneficial for:
- Heavy parts (table does not need to move)
- Slim chance of tool interference
Applications of 4-axis and 5-axis CNC machining
4-axis and 5-axis machining centers can be particularly useful for creating molds with deep cavities, for creating complex 3D shapes, and for machining on tilted surfaces of a part without compromising precision.
Although 5-axis machining can be used for a wide variety of parts, it has become particularly dominant in the production of parts like impellers and turbine blades, which have contoured surfaces unsuitable to 3-axis machining.
Share on social media...
Get Your Parts Into Production Today
Only 4 simple steps to complete your project. Follow the instruction and give it a try!
Upload Files
Get Quotation
Place an Order
Start Production
Latest news and stories
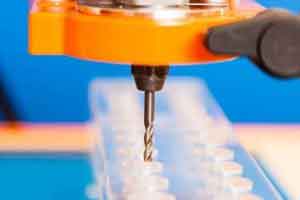
Understanding Plastic Fabrication Processes: A Complete Guide
Plastics are versatile materials with plenty of polymer options. They are among the most common […]
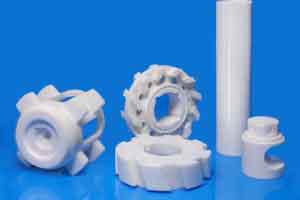
Ceramic CNC Machining: Another Option for Custom Manufacturing
It could be quite a cumbersome task to choose the best material for your manufacturing […]
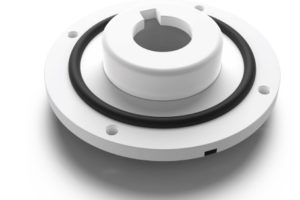
The Overmolding Design Guide You Must Never Forget
Overmolding is an injection molding process where you cast a layer of resin (usually a […]