What is CNC machining?
Jun 30, 2020
CNC machining is one of the most important manufacturing processes for creating metal and plastic components. This guide explains the basics of CNC machining, including its advantages and disadvantages.
What is machining?
Machining, in its loosest sense, is any manufacturing process in which material is cut away from a solid block. Because material is cut away rather than introduced, machining is known as a “subtractive” manufacturing process. (Processes that introduce material, such as 3D printing, are known as “additive” manufacturing processes.)
The material used in the machining process can be metal, plastic or something else, and the equipment and cutting tools can take various forms. Drilling, turning and milling are just some of the ways in which material can be removed from the block, which is commonly referred to as a “workpiece.”
This definition of machining has existed since the 19th century. It still applies today, though the methods of controlling cutting tools have evolved significantly.
What is Computer Numerical Control?
All machining processes involves the controlled movement of cutting tools. However, the biggest difference between traditional machining processes and today’s more advanced technologies is the means of control.
In the early days of machining, all cutting tools were controlled to some extent by hand. Machinists adjusted their mills and lathes manually, directing the sharp edge of the cutting tool toward the appropriate section of the workpiece using levers or wheels. This is still a common technique, and professional machinists can machine materials with a high level of precision. Tracers and patterns can also be used to increase accuracy and repeatability.
Now, however, there are alternatives to manual machining, the most important of which is CNC machining, or Computer Numerical Control machining, which was introduced throughout the 1940s and 1950s.
CNC machining involves the use of a computer to direct a machine’s cutting tools. Instead of relying on a human machinist to move the cutting tools to different sections of the workpiece, digital instructions direct the machine to precise coordinates, allowing it to operate without assistance.
How does the CNC machining process work?
The CNC machining process process starts with a digital 3D design of a part, which is created using Computer Aided Design (CAD) software. CAD software allows an engineer to create a visual rendering of a part: the 3D shape can be adjusted as necessary on-screen, and the software can sometimes carry out simulations to predict how the design will work in the real world.
Once the CAD design is finished, Computer Aided Manufacturing (CAM) software is used to convert it into something called “G-Code,” which is essentially a series of instructions for the CNC machine. The machine itself cannot comprehend a 3D shape in the same way a human can, but it can understand a series of simple instructions that, when followed, will ultimately lead to the creation of that 3D shape.
The G-Code contains information such as when and where the machine’s motors should move, how fast they should go, etc. These motors, following the instructions of the G-Code, guide the machine so that it can remove material from appropriate sections of the workpiece.
When the all the instructions have been followed, the result will be a completed part that matches the original design made on the CAD software. The part can then be used for its end purpose, refined further, or reproduced repeatedly.
Engineer designs part using CAD software > Design converted into G-Code > G-Code instructs cutting tools > Cutting tools remove material from workpiece > Workpiece becomes finished part
Advantages of CNC machining
CNC machining is a widely used manufacturing process for both prototypes and production parts. This is thanks to several factors, including cost, time and the specific mechanical advantages of machined parts.
Precision
Since CNC machines follow computer instructions, they are incredibly precise — more so than even the most skilled human engineer. Most CNC machines have an accuracy of around 0.02 mm, which means complex parts can be made with very tight tolerances.
Eliminating error is a high priority for manufacturers, and CNC machines dramatically reduce the probability of error.
Repeatability
One great thing about making parts from computer instructions is that those instructions can be executed over and over without changing anything. As long as the equipment itself is well maintained, CNC machines can reproduce identical parts over and over again.
This is much harder to do using manual techniques: even the very best machinist will struggle to create perfect replicas every time.
Scalability
Repeatability also has a beneficial effect on the scaling up of production. Since a machining job can be repeated multiple times (and across multiple machines if needed), companies can quickly turn a single prototype into a hundred thousand units of the same part.
As long as the digital file is kept safe, manufacturers can make infinite copies of a machined part.
Low labor costs
Although there are ethical considerations with all automated work, using CNC machines can reduce the cost of production when compared with traditional machining. Once the G-Code has been created and sent to the machine, it can be left alone unattended.
Of course, reduced machining labor doesn’t have to make human labor redundant. Instead, those machinists may choose to focus on producing an exceptional finish to the part once it leaves the CNC machine.
Versatility
CNC machines are capable of working with a wide array of materials, and can create a range of complex shapes. They are therefore used for a huge variety of different parts, from automotive components to food containers.
Endurance
Most CNC machines can work around the clock, and maintenance is relatively straightforward. As long as cutting tools are maintained and replaced when necessary, CNC machines can demonstrate impressive stamina, allowing for high-volume production at speed.
Disadvantages of CNC machining
Although CNC machining is used for a huge variety of applications, it is not suitable for every manufacturing job. Its limitations range from geometrical restrictions to cost factors.
Cost
CNC machines are much more expensive pieces of equipment than manual machines, and this is reflected in the price of CNC machined parts. As CNC becomes even more widespread, however, this price difference will become narrower.
Cost factors also depend heavily on quantities. For one-off parts, 3D printing may be a cheaper alternative to CNC machining; for hundreds of thousands of parts, a mass-manufacturing process like injection molding may be more cost-effective.
Geometrical restrictions
Compared to additive manufacturing, CNC machining comes with some geometrical limitations. Since the workpiece is cut from the outside, it is relatively difficult to create complex internal geometries within a machined part.
3D printers do not have this limitation, since a 3D printed part is created layer by layer.
Ethics of automation
CNC machines have made machining faster and more accurate, but they have also reduced the demand for skilled manual machinists, resulting in a shortage of work for many professionals.
Different types of CNC machine
Although all CNC machines use computer instructions to cut material from a workpiece, different machines achieve this objective in different ways. Depending on the shape and dimensions of a part, machinists may use CNC milling machines, CNC lathes, CNC routers or any specific variant of those machines.
CNC milling machines
Milling machines use rotary cutting tools to remove material from the workpiece, which remains stationary. They are highly accurate, and come in varying levels of complexity. 3-axis CNC mills can move their cutting tools along the X, Y and Z axes; 4-axis mills introduce rotation around the X axis; and 5-axis mills, the most flexible and therefore most useful, add further rotation around the Y axis.
CNC mills come in either horizontal or vertical formats. Horizontal milling machines mount their cutting surfaces on a horizontal arbor, while vertical milling machines orient the cutting head vertically. Heavier parts may be more easily machined using a horizontal machine, while vertical machines may be better for parts that require most machining on one side.
CNC turning machines
CNC lathes or CNC turning centers work in a different way to milling machines. Rather than move the cutting tool to different areas of a stationary workpiece, lathes rapidly rotate the workpiece itself. This allows the cutting tools to reach all around the object, and can be used to create conical, cylindrical and spherical parts with perfect symmetry.
Other CNC machine variants include:
- Plasma cutters
- CNC routers
- CNC drills
- Surface grinders
Unique advantages of 4-axis & 5-axis machining centers
All CNC machines are relatively effective at creating complex parts. Those with 4-axis or 5-axis capabilities, however, are exceptionally flexible and can be used to create highly complex components.
4-axis CNC machining centers add an extra axis of movement by introducing rotation around the X axis. This can be achieved by simply rotating the workpiece, and the extra axis of movement allows the cutting tool to approach the workpiece from new and otherwise impossible angles.
5-axis machining centers take that flexibility even further, introducing rotation around the Y-axis, tilting the work surface while also allowing the workpiece to rotate. This adds even more cutting capabilities, and is therefore the favored machining approach for engineers and machinists in industries like aerospace.
Share on social media...
Get Your Parts Into Production Today
Only 4 simple steps to complete your project. Follow the instruction and give it a try!
Upload Files
Get Quotation
Place an Order
Start Production
Latest news and stories
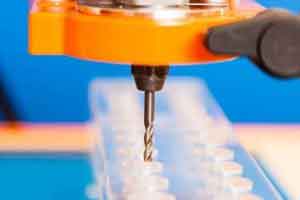
Understanding Plastic Fabrication Processes: A Complete Guide
Plastics are versatile materials with plenty of polymer options. They are among the most common […]
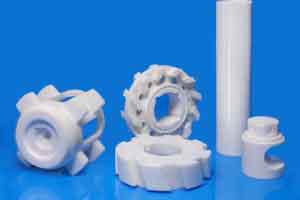
Ceramic CNC Machining: Another Option for Custom Manufacturing
It could be quite a cumbersome task to choose the best material for your manufacturing […]
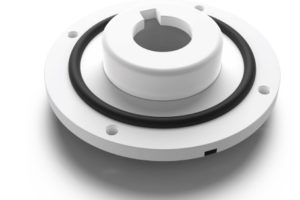
The Overmolding Design Guide You Must Never Forget
Overmolding is an injection molding process where you cast a layer of resin (usually a […]