What is injection molding?
Jul 09, 2020
Injection molding is a popular manufacturing process that uses molds and molten material to create huge volumes of identical plastic parts. It is used across many industries, and is suitable for the production of furniture, automotive parts, food packaging, toys, storage containers, mechanical parts and much more.
Because of its speed, versatility and cost-effectiveness, injection molding is currently the most widely used manufacturing process in the world for plastic parts.
So what exactly is injection molding? How does the process process work? What is a mold and what is being injected? Moreover, why have so many designers, engineers and manufacturers turned to injection molding to create plastic parts? This guide explains the basics of the injection molding process and presents some of its major advantages and disadvantages.
What is a mold?
The injection molding process comprises many stages and requires complex pieces of equipment to carry out. However, the process is easy to understand once you become familiar with its central component: the mold.
A mold is a piece of tooling made from a hard metal such as steel or aluminum that contains a cavity shaped like the part being made. The mold is therefore an inverse image of the part, with the empty space within the mold representing the actual object, whether that be an electronics casing, some food packaging, a bottle, a car component or maybe even a child’s toy.
This mold, with its cavity shaped like the desired part, gives manufacturers a great deal of power and freedom. Because although the metal mold itself can take a long time to fabricate, the plastic parts created by the mold can be made very, very quickly.
What this means is that manufacturers can potentially use one single mold to create hundreds of thousands of identical parts in a short space of time. They do this by injecting a molten plastic into the precisely shaped mold cavity, letting it cool and solidify, then pushing the solidified plastic out of the mold. The removed piece of plastic now has the exact shape of the mold cavity.
Because molds are durable, the process can be repeated over and over again, allowing for the creation of huge volumes of identical plastic parts.
How does injection molding work?
In principle, injection molding is simply the process of squeezing liquid plastic into a mold and waiting for it to harden. In practice, however, it’s a little more complicated than that.
There are a wide range of material possibilities with injection molding, so the first stage of the process involves selecting an appropriate thermosetting plastic — a material that can be melted, injected and then cooled in order to rapidly form a plastic part. Many materials can be used for this process, including rigid, flexible and rubber-like plastics.
Before the injection molding cycle starts, the material is usually acquired in granular form. But before it can be turned into a part, it must be heated and transformed into its molten form. This process is carried out by a heated barrel. The material, stored in a hopper, is forced by a ram into the heated barrel, where it liquifies. It is then pushed toward the mold by a reciprocating screw.
The force from the screw, which is rotated by a motor, moves the molten plastic to where it needs to be. When the material reaches the end of the heated chamber, it is ejected from a nozzle through some thin channels (known as runners) and into the mold cavity. This is the injection process that gives the process its name.
Because the metal mold is cold, the plastic solidifies almost immediately, forming the final part. This solid part is then removed by opening the mold, allowing for the next shot of plastic to be prepared.
The process can be repeated over and over, until the job is completed or until the mold needs to be replaced. In many instances, replacing the mold will not be necessary, since molds made from very hard steel can be used over a million times.
Advantages of injection molding
Efficiency
The injection molding process is extremely fast. Molten thermoplastics cool rapidly within the metal mold, and the time between cycles can be as little as 20 seconds, making the process highly efficient and cost-effective.
Machinery can also be operated round the clock, which shortens total production time.
Material & color options
The injection molding process is compatible with many different plastics and color formulations. Depending on the project at hand, plastics can be selected based on a number of factors, including tensile and impact strength, elasticity and heat resistance.
Injection molded parts are also easy to color, which is one of the reasons the process is widely used for consumer goods. Colors can be applied in pellet and liquid form, and some moldable resins are pre-colored.
Strength
Molded parts can be made from high-performance thermoplastics, and inserts can be used to further increase strength. Unlike 3D printed parts, molded parts do not have layer lines and therefore do not exhibit weakness across certain planes.
Complex & detailed parts
Although certain design principles must be followed, molds for injection molding can be made in a variety of complex shapes, allowing for the creation of complex plastic parts.
Furthermore, the high pressures used to inject the plastic mean that parts can be created with small and intricate details.
Surface finish
One of the biggest advantages of injection molding is the high surface quality of parts, even those coming straight from the mold. Although parts can be treated with finishing procedures, as-molded parts have a smooth surface that is suitable for many end uses.
Consistency
Since a single mold can be used for hundreds of thousands of cycles, parts are highly consistent and able to meet required standards and certifications.
Disadvantages of injection molding
Mold cost
Although the cost per unit of an injection molded part can be very low, the initial tooling costs are high. Metal molds must be made using a process like CNC machining or metal additive manufacturing, and this requires significant material and labor costs.
Nonetheless, the emergence of rapid tooling as a prototyping technique has made low-volume injection molding more affordable. With rapid tooling, molds are fabricated quickly and to looser tolerances, allowing manufacturers to shorten lead times.
Design restrictions
Engineers must work within certain design parameters when creating metal molds. And although it is possible to create a huge variety of injection molded parts, some alternative manufacturing methods may offer greater design flexibility. 3D printing, for example, allows for more complex internal geometries.
Lead times
Because injection molding is a two-stage process — mold fabrication is followed by part fabrication — it can be slower than some alternative processes, at least in smaller volumes.
Cost of low-volume orders
Since metal tooling costs significantly more than a single shot of plastic, high-volume orders have a much lower cost per unit.
Whether injection molding represents the best value for money depends on several factors, such as number of parts required, cost of tooling and availability of alternative technologies.
Start your injection molding project is easy, just upload your CAD files to our plaform, get free quotation and professional suggestions today!
Share on social media...
Get Your Parts Into Production Today
Only 4 simple steps to complete your project. Follow the instruction and give it a try!
Upload Files
Get Quotation
Place an Order
Start Production
Latest news and stories
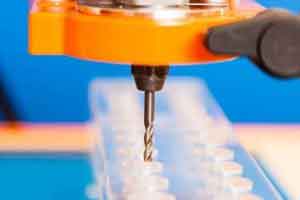
Understanding Plastic Fabrication Processes: A Complete Guide
Plastics are versatile materials with plenty of polymer options. They are among the most common […]
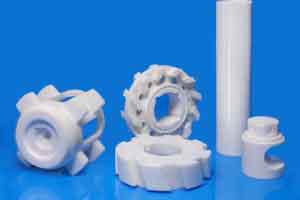
Ceramic CNC Machining: Another Option for Custom Manufacturing
It could be quite a cumbersome task to choose the best material for your manufacturing […]
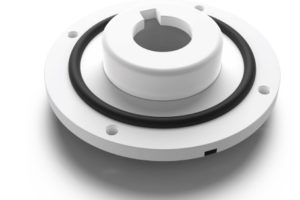
The Overmolding Design Guide You Must Never Forget
Overmolding is an injection molding process where you cast a layer of resin (usually a […]