While some still think of 3D printing as a hobbyist technology, not used for much more than making Yoda heads or pencil holders, they would be wrong. For years, 3D printers and 3D printer services have been capable of much more, evolving beyond DIY and maker applications to industrial prototyping. Today, 3D printing technology is even breaching the realm of end-use parts. This means that 3D printer services have grown substantially in recent years, with businesses from many industries relying on their capability and expertise to produce high-quality prototypes and small-batch production runs.
What is 3D printing?
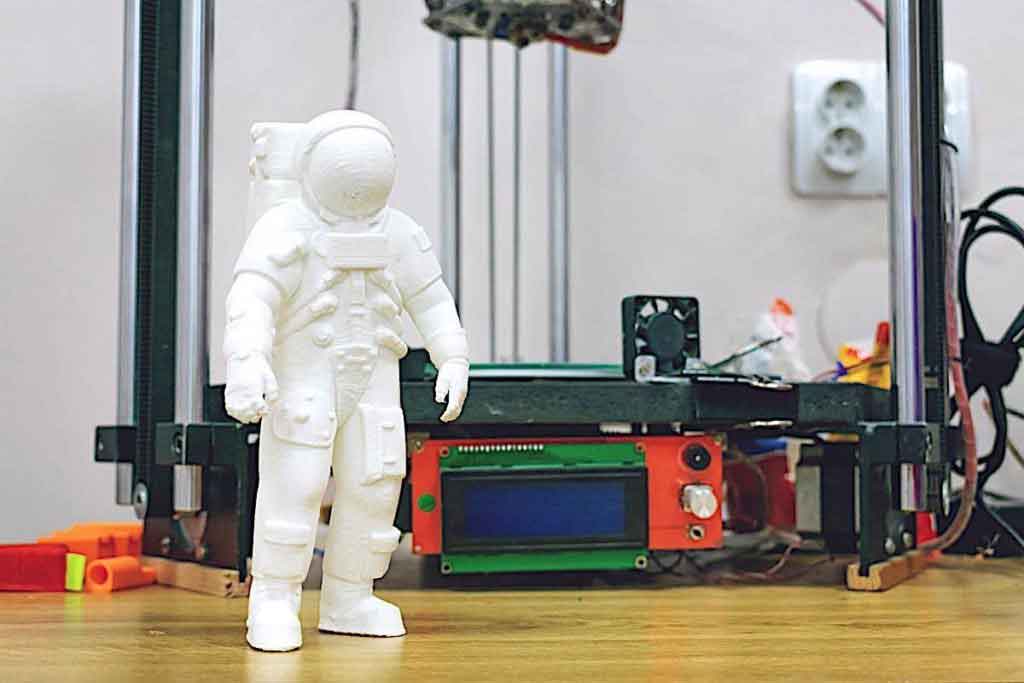
At its foundation, 3D printing, also known as additive manufacturing, refers to a group of technologies that build objects additively rather than in a subtractive manner. That is, while technologies like CNC machining make parts by removing material from a blank of raw material, 3D printing adds material, often layer by layer, to create a part from nothing.
Like CNC machining, 3D printing uses a digital model like a CAD file as its basis. The CAD file is processed through a 3D printing software (known as slicing software), which segments the model into printable layers and sends printing instructions to the machine.
Plastic 3D printing
Within the category of 3D printing, there are many technologies on the market. On the side of plastic, there are a handful of dominant technologies, including fused deposition modeling (FDM), selective laser sintering (SLS) and stereolithography (SLA).
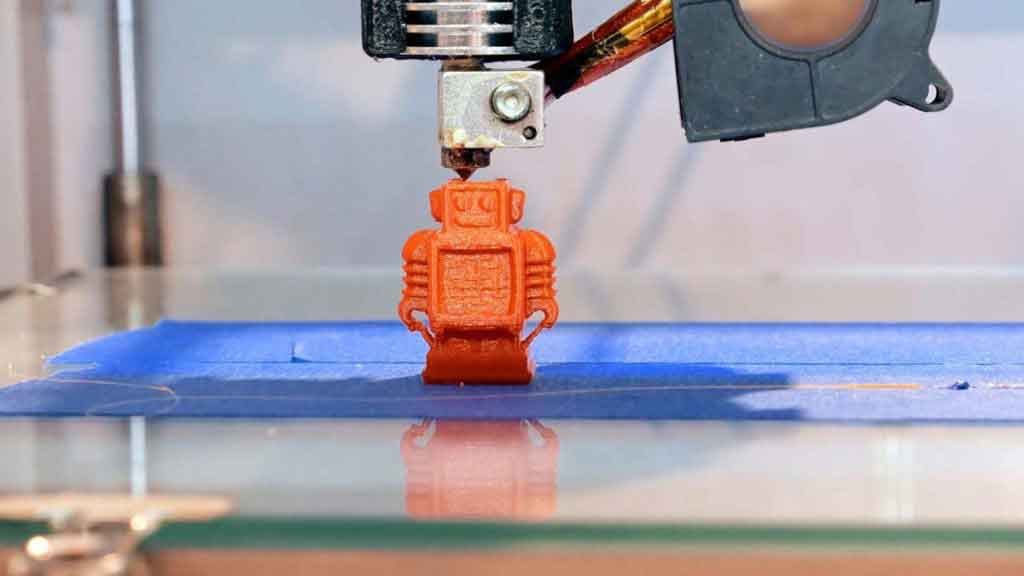
- FDM: An additive manufacturing process in which plastic filaments are fed through and melted by a hot end print head and extruded in fine layers to build up a part, from the bottom up. One of the most cost-accessible 3D printing technologies in terms of machine and materials.
- SLS: An additive manufacturing process in which a laser is used to sinter layers in a powder bed made up of fine polymer particles. One of the more cost-heavy plastic 3D printing processes in terms of machine and materials.
- SLA: An additive manufacturing process in which a light source (often UV) is used to polymerize a vat of liquid plastic (resin) layer by layer, transforming the liquid material into a solid.
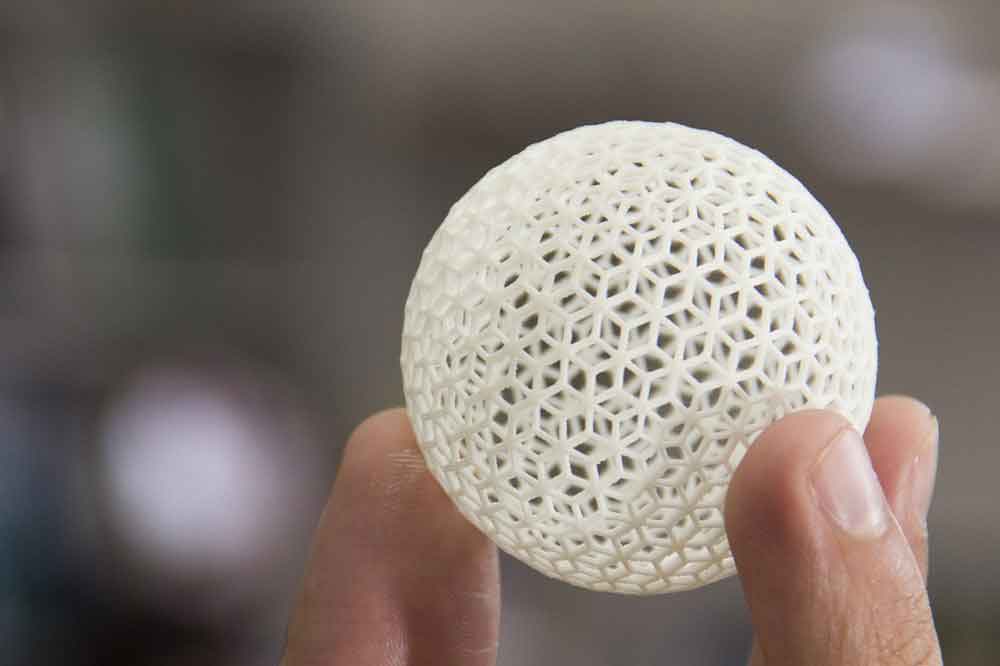
Enter metal 3D printing
Today, it is possible to manufacture more than just plastic parts using 3D printing technologies. Industries—including aerospace, automotive, medical, energy and defense—are increasingly using metal 3D printing to produce innovative new components that take advantage of 3D printing’s inherent design freedom (more on that below).
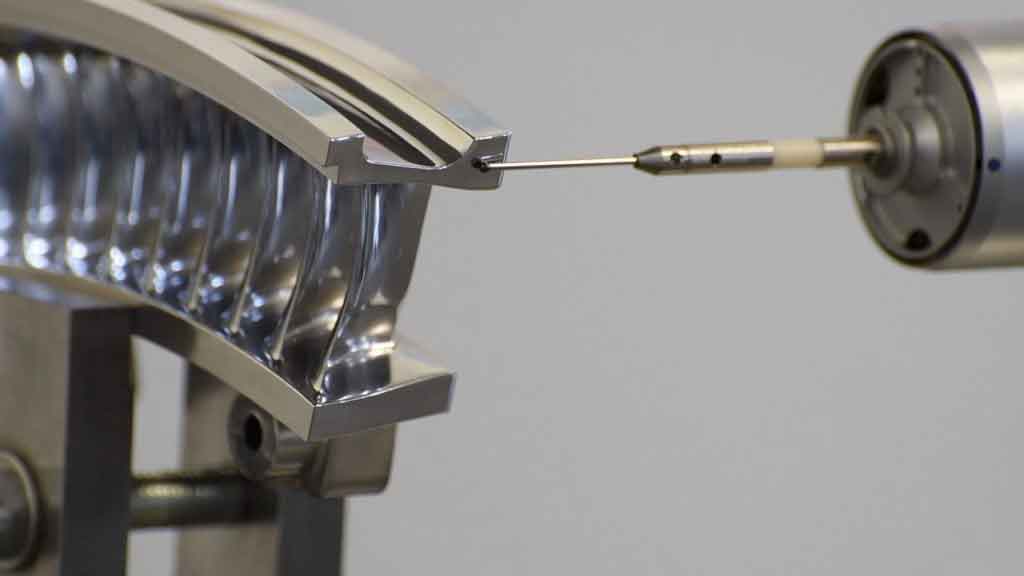
There are several metal 3D printing technologies on the market today, all of which have different benefits. Laser Powder Bed Fusion (LPBF) is probably the most widespread metal additive manufacturing technology. This process works by spreading a fine layer of metal powder onto a build surface and then using a laser beam to selectively melt the powder layer. This process is repeated, layer by layer, gradually building up a dense, metal component.
Another approach to metal 3D printing is a process called Direct Energy Deposition (DED). This technique uses either metal powder or metal wire as its base material. DED printers use a print head that combines a laser beam with a powder or wire extrusion system, effectively melting the metal feedstock as it comes out of the print head. This melted metal material is then deposited onto a build surface or a substrate.
One of the newer arrivals on the metal 3D printing market is Binder Jetting. Binder jetting uses a bed of metal powder (the quality of metal powder doesn’t have to be quite as high as it does for LPBF). Instead of a laser, the process jets a binder material onto the surface of the powder bed. This is repeated layer by layer until a part is built and removed from the unbound powder. Binder jetting results in a green part, meaning that the component must undergo a debinding and sintering process to result in a dense metal part suitable for end-use applications.
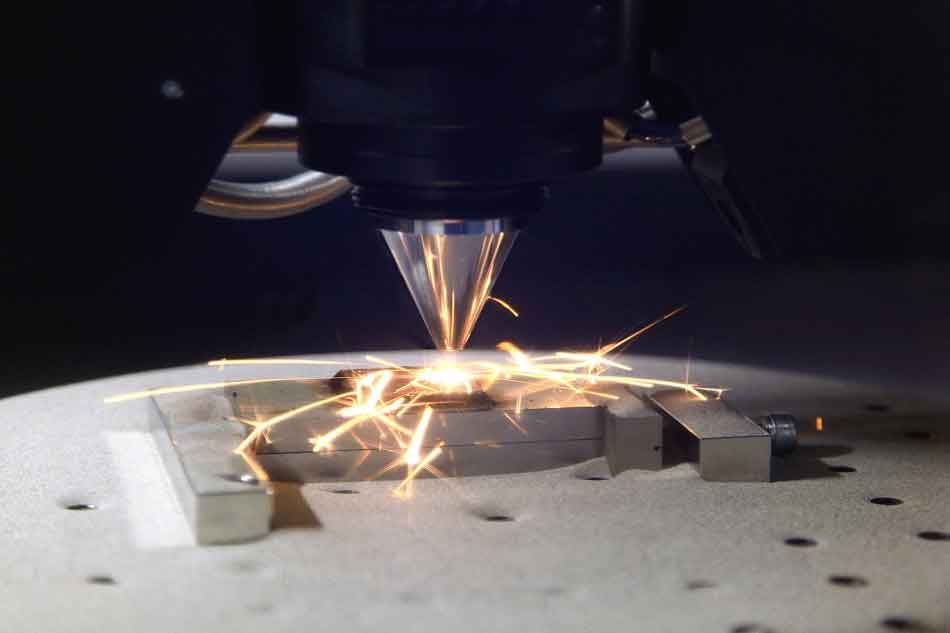
What are the benefits of metal 3D printing?
Contrary to what some believe, 3D printing was not invented to replace more traditional manufacturing processes. Instead, it gives manufacturers access to more possibilities, especially concerning design freedom.
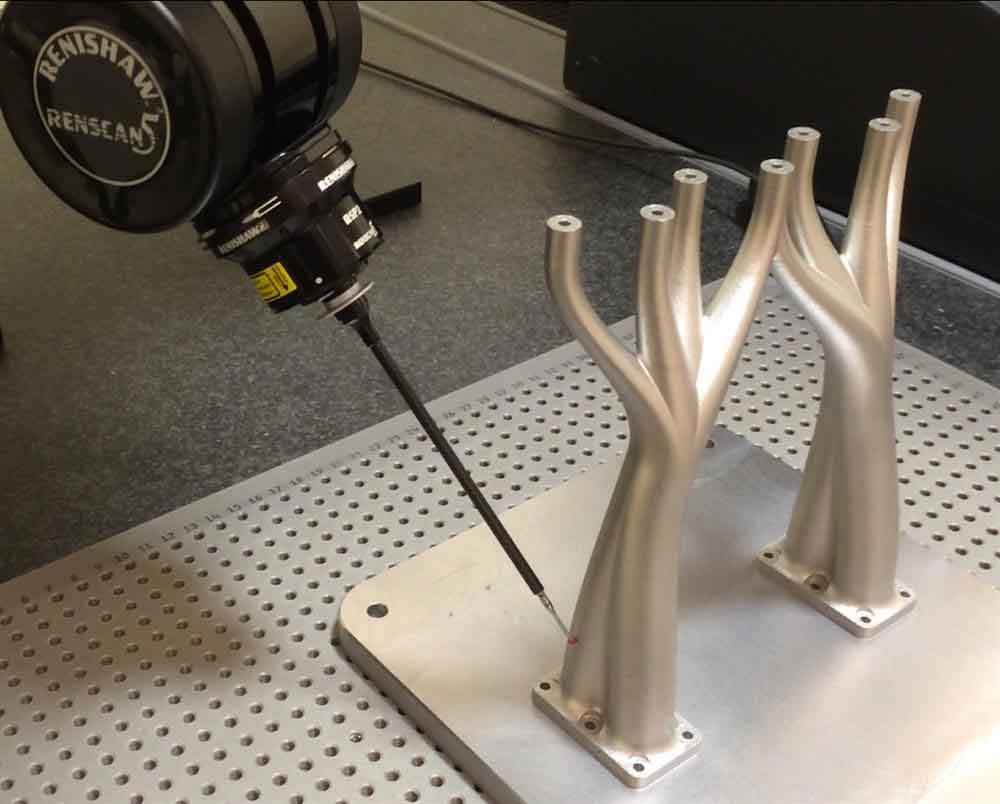
Because of its additive nature, 3D printing does not have the same design constraints as subtractive processes, like CNC machining. 3D printing can create components with complex internal geometries, as well as outer structures. It can also enable more organic forms, which can lead to more lightweight parts with optimized performance and strength. Looking at the aerospace industry, for example, where weight is a critical factor in developing parts, 3D printing is allowing for better, lighter parts to be integrated into aircraft, ultimately contributing to reduced fuel consumption.
Complex internal structures are also opening new possibilities in many areas. For example, parts like heat exchangers or engines that require cooling can integrate cooling channels directly into the structure. This means that parts can be printed in a single piece, rather than manufactured in many parts and then assembled.
These advantages do not mean that metal 3D printing is always the right option: for many parts, CNC machining is the more efficient and affordable option. However, 3D printing can be used in cases where special properties or functions are required. How to know if metal 3D printing is right for you? 3D printer services can help.
3D printer services
3D printer services such as RapidDirect provide access to the state-of-the-art technology without customers having to invest in the costly hardware and necessary skills. Our manufacturing experts not only know how to operate metal 3D printing systems—which require in-depth knowledge for optimal results—but we also know when metal 3D printing is the best option for your project.
Because 3D printing is still a relatively new technology, there are hurdles to its broad adoption. Among the key setbacks are lack of skills and design know-how. If you don’t have a team member who knows how to design for 3D printing or how the process works, you can’t take advantage of it. Another key challenge is capital investment. While there are many affordable plastic 3D printers on the market, metal 3D printing technologies and industrial polymer 3D printing systems are still very expensive. For a company that wants to explore 3D printing and learn about its potential, it is hardly worth it to buy an entire system right off the bat.
That’s where 3D printer services come in. We make the technology investment so you don’t have to. We also have trained operators that know the ins and outs of all our 3D printers. This ensures that when you do place an order for a 3D printed part it is a success. We can also provide design support, helping you to optimize a part design for additive manufacturing.
Today, China Medical CNC Machining Inc. offers professional 3D printer services for a range of technologies, including FDM, SLA, SLS and PolyJet. We also now offer metal 3D printing services for high-quality parts made from metals such as aluminum and steel. Whether you are interested in a prototype or a small batch of 3D printed metal parts, we are here to help!
Simply get in touch with us directly or upload your part design via our automated quoting engine. We’ll help you to figure out the best production method for your project and see it through to the end.
Share on social media...
Tags
Popular Topics
1
Understanding Plastic Fabrication Processes: A Complete Guide
Ayotomiwa Omotosho13 Feb
2
Ceramic CNC Machining: Another Option for Custom Manufacturing
Oluwafemi Adedeji13 Feb
3
The Overmolding Design Guide You Must Never Forget
Oluwafemi Adedeji13 Feb
4
What You Need to Know About the Overmolding Process
Paul Richard05 Feb