Summary: A look at the ecological impact of steel machining and how steel recycling is important for manufacturers.
Every day environmental pollution becomes more serious and the world’s response to it more urgent. To address and try to turn environmental pollution (and to avoid its disastrous effects), we have to reevaluate each part of our lives and our societies. In the following article, we’ll look at the ecological impact of steel machining and whether steel machining can become more sustainable through strategies like waste management.
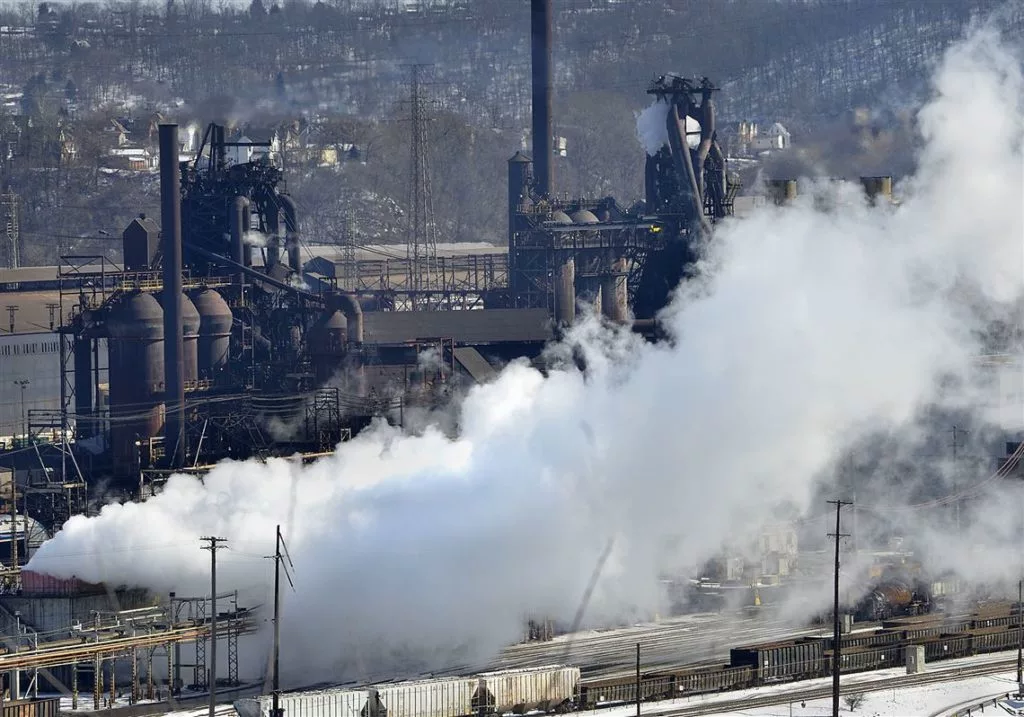
What is steel machining?
Steel is one of the most widespread metals for CNC machining. Its popularity is derived from its many material properties, including corrosion resistance, strength and durability. There are also many types of steel—including stainless steels and steel alloys—which can be used for a variety of applications, from industrial parts to medical devices. Of course, different types of steel have different rates of machinability, which means that they are easier or harder to cut, mill and drill using CNC machining tools.
For instance, stainless steel alloys, including stainless steel 303, are relatively easy to machine. Some steel alloys, including Carbon Steel 1045 are also well suited for CNC machining and present few problems for machining services.
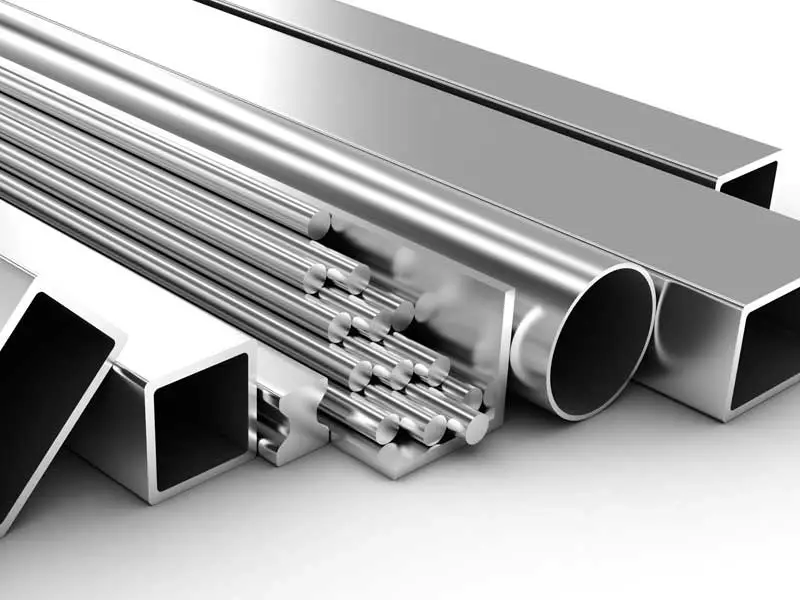
In the machining process, a block of steel metal (called a blank) is attached to the CNC machine, and computer-controlled tools, like mills and lathes, are used to cut away and remove material from the blank. Ultimately, the final component is created by removing enough raw material from the original block. This process leads to material waste, which is an ecological concern.
Steel machining and its environmental impact
The debris created in the steel machining process, also known as swarf, is an inevitable part of CNC machining. After all, with any subtractive manufacturing process, there is bound to be leftover material. However, there are steps that manufacturers and CNC machining services can take to minimize the amount of waste and deal with whatever is left more ecologically.
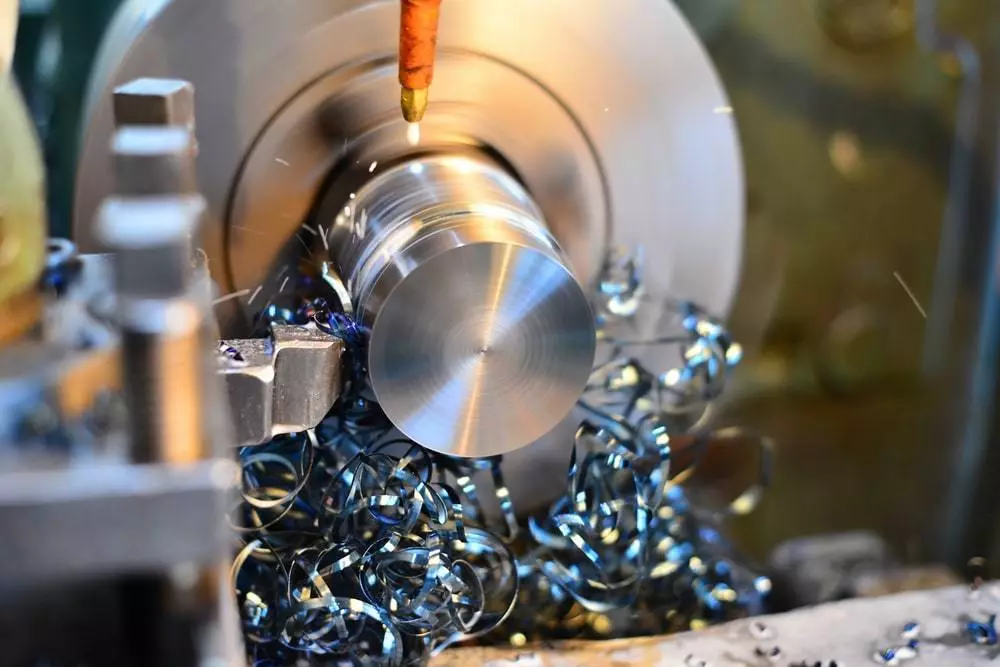
One of the easiest steps that manufacturers can take is choosing the right size of the steel blank. That is, if a blank is needlessly oversized, there will be more wasted material, whereas if the block of raw steel material is as close as possible to the final part’s dimensions, less waste will be generated.
The steel machining process can also be optimized to reduce the amount of material waste. By ensuring consistency and precision in the machining process, manufacturers and CNC machining services can reduce mistakes in part machining, which will minimize the number of failed parts that have to be tossed. Manufacturing the part right the first time will also save energy (less machining time=less energy used), as well as time and money for the service and their customer.
Steel machining waste management
Because metals like steel are not renewable—they are made from ores extracted from the earth and cannot be replenished naturally—the only way to use them efficiently is to recycle them. Today, steel is one of the most widely recycled materials. In fact, about 45% of the world’s steel production is derived from recycled materials.
It is therefore necessary for manufacturers to establish a recycling strategy for steel scraps created by steel machining. Many CNC machining services, including RapidDirect, have implemented systems that collect steel debris after the milling process. Once the steel scraps are collected, there are different options for recycling metal waste. Most often, manufacturing services work with a third party recycling partner, which processes and treats the scraps, turning them into reusable manufacturing raw materials.
In some cases, manufacturers may opt to implement the recycling equipment themselves, though this involves investing in the systems and skills needed for recycling metal. Bringing the recycling process in-house does have certain benefits: in the long-run manufacturers can save on shipping costs for the steel machining scraps, as well as on new material costs.
How is steel recycled?
Once steel swarf has been collected after the steel machining process, it undergoes a series of steps that transform the metal bits from waste to raw material ready for manufacturing. The first step in the recycling operation is processing. In this phase, the steel debris is broken down even more—or shredded—so that the steel pieces have the largest surface to volume ratio possible. This step enables the next one, melting.
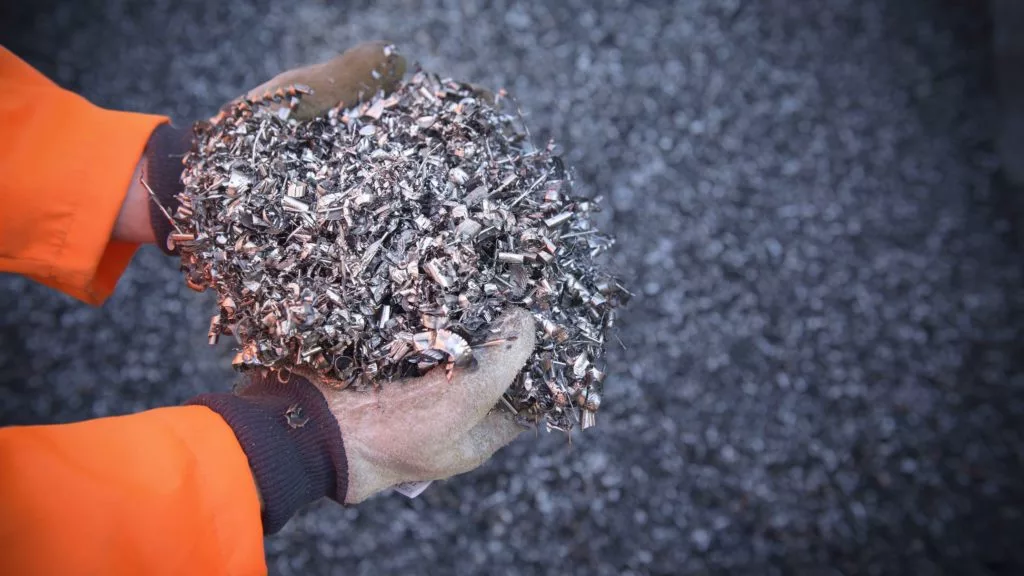
The smaller the steel pieces, the faster they will melt (and with the least amount of energy). The melting process is carried out in an industrial furnace, heated to a specific temperature, depending on the metal type. The length of the melting process depends on several factors, including the volume of steel and the size of furnace, but can take up to a few hours to complete.
Once the steel scrap metal has been melted, it then undergoes a purification process. This step ensures that any contaminants are removed from the raw melted material before it solidifies. The melted metal is then solidified into standard shapes, like bars or blocks, which can then be shipped to manufacturers for a variety of applications.
Thanks to its specific metallurgical properties, steel can be recycled over and over again without any degradation, meaning that the process continues for each manufacturing cycle.
Is steel recycling ecological?
The steel recycling process is energy intensive: the furnaces used to melt the steel down consume a lot of energy, which means that the process still comes with an ecological impact. However, compared to the energy and resources required to extract virgin ore from the earth and process it into different steel alloys, recycling steel is far more sustainable. Looking at steel specifically, recycling scraps can save over 50% in energy consumption compared to raw material extraction and processing.
By using recycled metal made from scraps, manufacturers also generate less mining waste and water consumption, which results in a smaller ecological footprint.
Steel debris left over from the steel machining process is among the easiest type of scrap to recycle: machining scraps can be reprocessed and ready for production within weeks. Other types of steel scrap, resulting from steel products that are damaged or no longer needed, can take months to process and recycle.
RapidDirect, steel machining at your service
At China Medical CNC Machining Inc., a Shenzhen-based rapid prototyping service, steel machining is among our manufacturing capabilities. We offer customers a choice of over 45 steel alloys and 16 stainless steel subtypes. We also offer machining services for other metal materials, including aluminum, copper, brass and titanium.
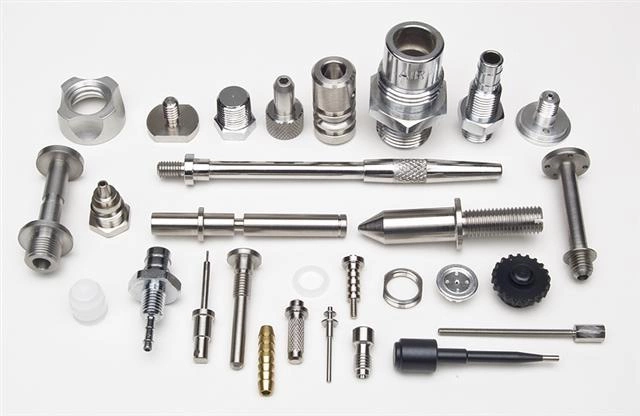
We are an active player in the steel recycling process, providing scrap metals to third party recycling centers. Many of our steel raw materials are also derived from recycled steel. If you have any questions about our steel machining capability, don’t hesitate to get in touch with us directly, or to get an instant quote for your production needs.
Share on social media...
Tags
Popular Topics
1
Understanding Plastic Fabrication Processes: A Complete Guide
Ayotomiwa Omotosho13 Feb
2
Ceramic CNC Machining: Another Option for Custom Manufacturing
Oluwafemi Adedeji13 Feb
3
The Overmolding Design Guide You Must Never Forget
Oluwafemi Adedeji13 Feb
4
What You Need to Know About the Overmolding Process
Paul Richard05 Feb