Injection molding is compatible with a variety of materials, including thermoplastics, thermosets and elastomers. This article discusses the material possibilities of injection molding, as well as the differences between tooling materials.
Tooling metals for injection molding
Although your choice of injection molding material may influence your choice of tooling material, we will start with tooling material options, since the tooling stage precedes molding when your parts get made.
When thinking about tooling materials, it’s important to remember that injection molding is often used to make hundreds of thousands or even millions of identical plastic parts. Because of this, the metal molds used in the process must be highly durable.
Traditionally, hard tool steels have been used for injection molding, but aluminum has become a similarly popular choice. Metals like nickel can also be used, but we will focus at present on steel molds and aluminum molds since these are the most common.
Choosing a tooling material depends on several factors, including:
• How many molded parts will be made?
• What kind of plastic will be used for the molded parts?
• How complex is the part design?
• What is the total budget for the project?
In general, mild plastics are suitable for either steel or aluminum molds, but very abrasive plastics may be better suited to harder steel molds. Additionally, steel molds may be better at handling very large volumes of plastic parts.
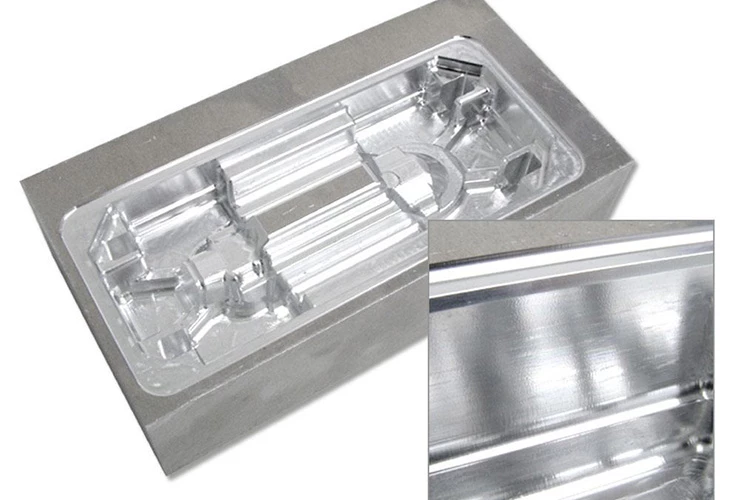
Aluminum molds, however, represent a highly cost-effective option. Many aluminum grades are affordable and able to be worked with processes like CNC machining, which also makes lead times very short. Aluminum may, therefore, be a preferable tooling material for low-volume orders.
Steel benefits:
• Longer lifespan
• Abrasion resistance
Aluminum benefits:
• Lower cost
• Shorter lead times
Important properties for injection molding materials
Choosing an injection molding material requires one to think about the purpose of the part. Does it require strength, toughness or elasticity? Should it exhibit high or low friction? Does it need to be chemically resistant or heat resistant? An injection molding material should be chosen only when the desired material properties have been identified.
Material properties to consider may include:
Property | Example materials |
---|---|
Strength | POM, Nylon, PEEK, |
Rigidity | POM, PMMA, PET, HIPS |
Flexibility | ABS, LDPE, PVC |
Heat resistance | PET, PEI, PP, PPS |
Fatigue resistance | POM, Nylon |
Chemical resistance | LDPE, HDPE, PP |
Affordability | LDPE, HDPE, PP, PVC |
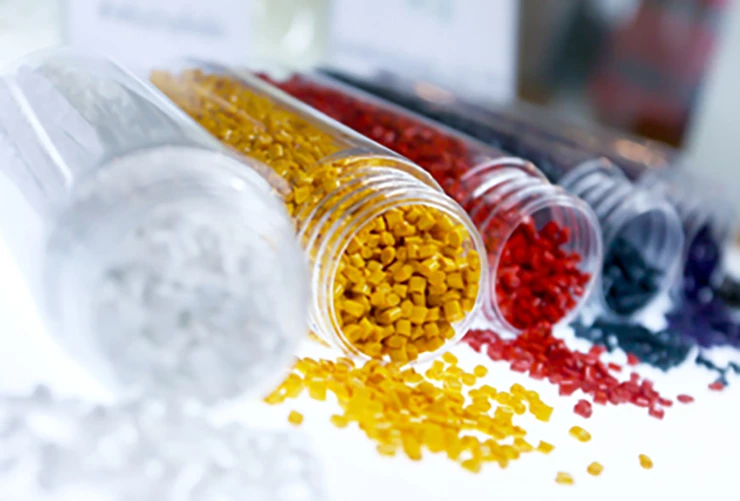
China Medical CNC Machining Inc. can help you find a suitable injection molding material based on your specific project. Just tell us what you need to make.
Injection molding materials
Suitable injection molding materials fall into three main categories: thermoplastics, all of which can be used for the process; thermosets, some of which can be used; and elastomers, some of which can be used. It is also possible to create composites of two or more materials.
Thermoplastics are typically used because they are inherently suited to the molding process. These plastics become soft and pliable when temperatures are raised but return to their solid form when temperatures are decreased.
This means thermoplastics can be added to the hopper of the injection molding machine in solid, granular form, then melted in the heated chamber and injected into a metal mold. When the heated plastic hits the inside of the mold, it begins to cool down and solidify, forming the finished part.
Injection molding plastics offered by China Medical CNC Machining Inc. include:
• ABS
• POM
• Acrylic
• HDPE
• Nylon 6
• Nylon 6/6
• PBT
• PC-PBT
• PEEK
• PEI
• PLA
• Polycarbonate
• Polypropylene
• PPE-PS
• PPS
• PSU
• PVC
• LDPE
• PC-ABS
• PET
• Polyethylene
• Polystyrene
• TPE
• TPV
Injection molding materials for specific parts
Injection molding is a flexible process, and it may be possible to choose between several materials for an injection molded part. However, some conventions exist for widely manufactured parts such as housings, containers, valves, etc.
Below are some common injection molded parts and the materials usually chosen for their manufacture.
Containers
PC, LDPE, HDPE, Polystyrene
Containers are some of the most widely manufactured injection molded parts, whether for food, commercial products or other objects. Plastics with chemical resistance and translucency may be preferred.
Electrical components
PET, PEI, TPE
Electrical components are frequently made using the injection molding process. Tough and resistant plastics with low water absorption are often suitable.
Bearings
POM, Nylon, PET, PPS
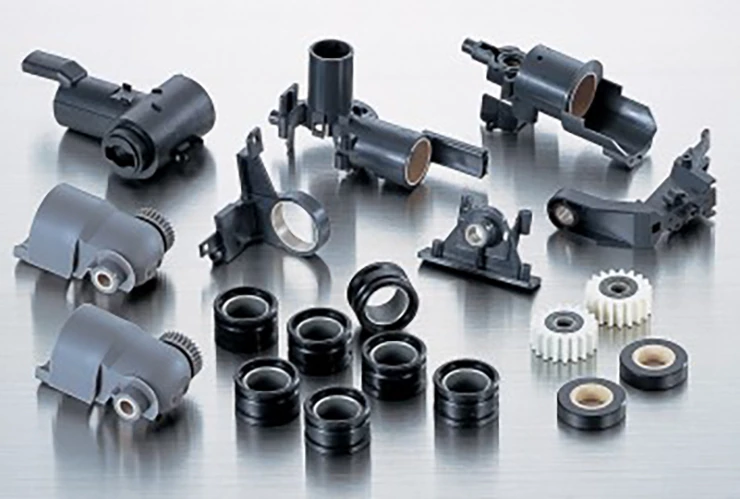
Bearings and other machine parts can be made with injection molding, as long as a strong plastic with a good level of fatigue resistance is used.
Valves
POM, PET
Valves are used to shut off air or liquid supply and are commonly made using the injection molding process. Chemically resistant materials like POM and PET are commonly used in their manufacture.
Automotive components
ABS, PC, PET
Injection-molded automotive components are commonplace, but the suitability of certain plastics depends on the nature of the part.
ABS may be used for consoles and panels, while more rigid materials like PET may be used for parts like filters and pumps. Bumpers are often made from polypropylene.
Toys
ABS, Polystyrene, PVC
Many children’s toys are made using injection molding but require a plastic with good toughness and impact resistance. LEGO bricks, some of the most famous toys of all, are made using ABS.
Injection-molded parts with color
Injection molding is widely used for commercial products, so it is important that manufacturers can create molded parts in a range of colors. (Companies may want to use colors that match their branding, for example.)
Thankfully, adding a splash of color to injection molded parts is easy.
Some raw materials come pre-mixed with pigment and therefore require no further coloration. These materials are known as compounded colors. For uncolored plastic pellets, however, there are three other ways to create a new hue:
Solvent coloring
Colorless pellets can be colored by using a pigmented oil mixed with a solvent. The mixture is applied as a spray just before the molding cycle begins.
Dry pigment mixing
Pellets can also be colored with dry pigmented powder instead of oil and solvent. With this process, the colored powder is mixed with the pellets in a hopper.
Share on social media...
Tags
Popular Topics
1
Understanding Plastic Fabrication Processes: A Complete Guide
Ayotomiwa Omotosho13 Feb
2
Ceramic CNC Machining: Another Option for Custom Manufacturing
Oluwafemi Adedeji13 Feb
3
The Overmolding Design Guide You Must Never Forget
Oluwafemi Adedeji13 Feb
4
What You Need to Know About the Overmolding Process
Paul Richard05 Feb