Injection Molding for Automotive Applications
May 15, 2019
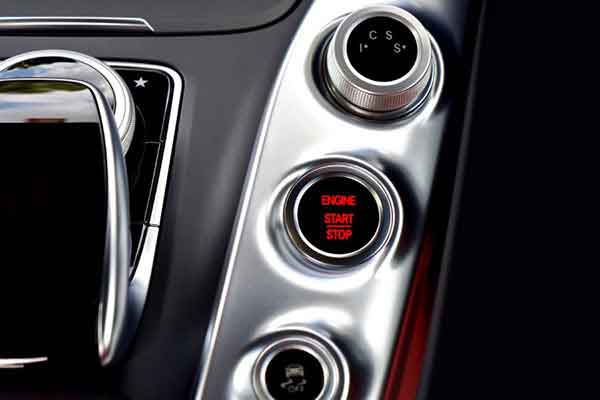
Injection molding is one of the most commonly used production processes for plastics, as it offers a viable solution for mass producing high quality and consistent parts from a broad range of polymers. In the automotive industry, where consistency, safety and quality are all of the utmost importance, automotive injection molding has become a staple.
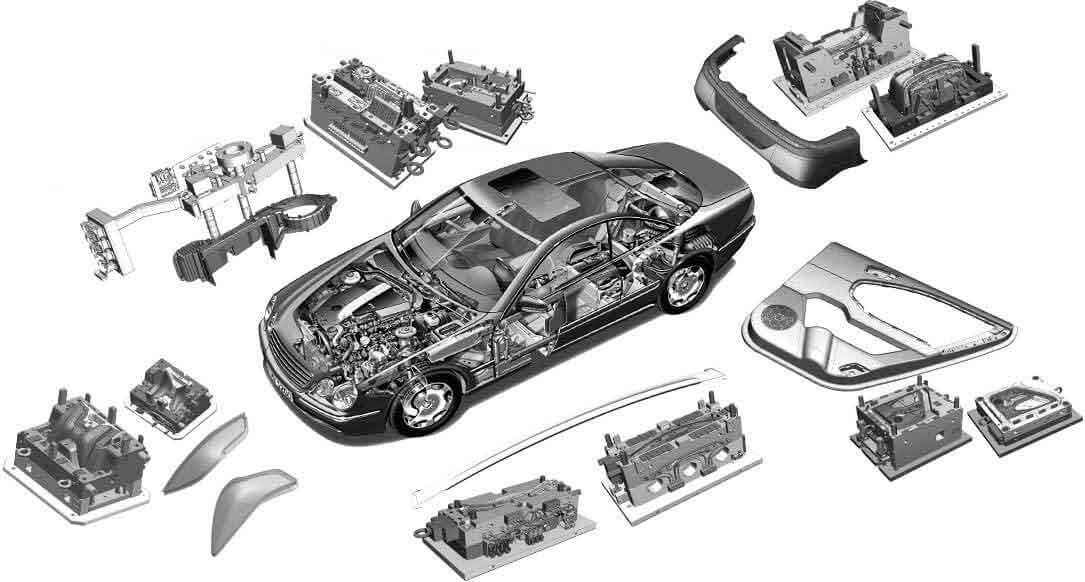
In the early days of the automotive industry, cars were made almost entirely of metal, which meant that they were clunky and extremely heavy. As the industry advanced and the plastics market erupted in the 1940s and 50s, automotive manufacturers began to explore the use of polymer parts for vehicle production. In the 1970s, the first cars with plastic decorative elements were rolled out, while more functional parts like plastic headlights, bumpers and fenders were introduced in the 1980s.
In the early 2000s, the first plastic structural components for cars were introduced, which had the advantage of being more lightweight than their metal counterparts, unlocking improved fuel efficiency and cheaper production. Today, injection molding is still one of the dominant production methods for manufacturing plastic parts in the automotive industry because it is well suited to mass production.
Advantages of Injection Molding for Automotive Applications
Injection molding is an established production process in which a molten plastic material is injected into a mold cavity. The melted plastic then cools and hardens and the finished part is removed. Though the mold design process is critical and challenging (a poorly designed mold can result in defects), injection molding itself is a reliable method for producing solid plastic parts with a high quality finish.
1. Repeatability
In the automotive industry, repeatability—or the ability to consistently produce identical parts—is crucial. Because injection molding typically relies on robust metal molds, the final plastic parts produced using the mold are practically identical. There are factors that come into play with injection molding, but if the mold is well designed and made, injection molding is a highly repeatable process.
2. Scale and cost
Though the injection mold-making process is expensive (as well as the cost of the mold), injection molding is a highly scalable process whose overall cost decreases the more parts are made. For mass production applications, injection molding is thus beneficial to the manufacturer. For anything less than mass production, however, injection molding tooling costs may curb the cost efficiency of the process.
3. Material availability
A significant benefit of using injection molding for automotive production is the wide range of rigid, flexible and rubber plastics the process is compatible with. In the automotive industry, a range of different polymers are used for various applications, including ABS, polypropylene, acrylic, acetal, nylon, polycarbonate and more.
4. High precision and surface finish
Injection molding is ideal for producing plastic parts with relatively simple geometries and results in parts with high surface finish quality. Manufacturers have many finish options when producing parts, including various surface textures—such as glossy, rough or matte—which are applied directly to the mold rather than the molded part. Different plastic materials also influence the final surface finish.
5. Color options
When plastic injection molding automotive parts, it is easy to modify colors in order to fit within the color scheme of the vehicle. Unlike other processes, injection molding allows you to mix dyes with the raw material pellets before manufacturing begins. This produces solid, consistent coloration without the need for painting or tinting after the molding is complete.
6. Fast prototypes with rapid tooling
Although injection molding is widely used for mass production of auto parts, an automotive plastic parts manufacturer can also use it as a prototyping tool. By creating fast, low-cost aluminum molds with rapid tooling — usually by additive manufacturing or CNC machining — manufacturers can turn around short runs of prototype molded car components much faster than they can with traditional (steel) tooling.
Production Applications for Automotive Injection Molding
Within the automotive sector, injection molding is one of the predominant methods used for forming plastic parts. Looking at a completed car, it would be difficult to list every single component produced using injection molding, so we’ll take a look at some of the main ones.
1. Under-the-hood
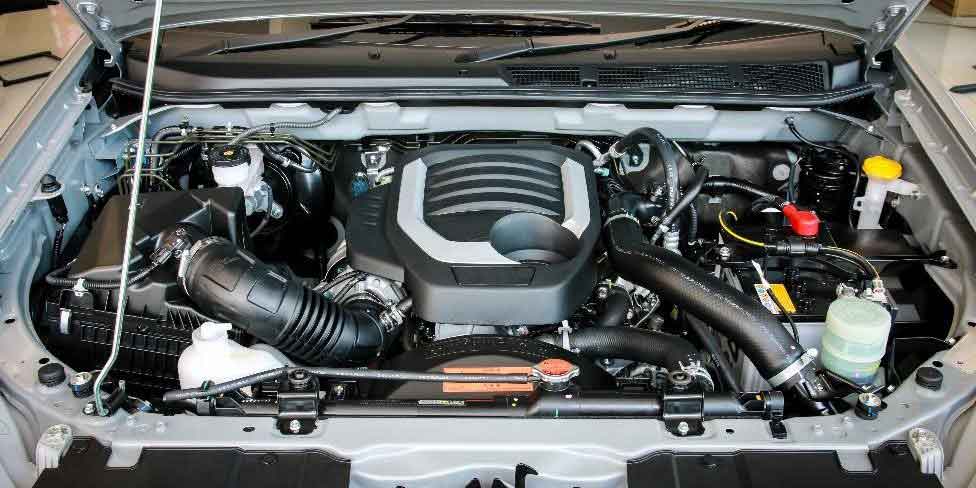
For the past two decades or so, many under the hood components that were once made from metal have been transitioned to plastic. For these applications, robust polymers such as ABS, Nylon and PET are common. Parts such as cylinder head covers and oil pans are produced using injection molding and offer lower weights and costs compared to metal parts.
2. Exterior
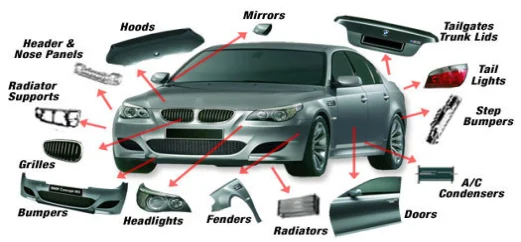
Injection molding is an established process for many exterior automotive components, including fenders, grilles, bumpers, door panels, floor rails, light housings and more. Splash guards are a fine example for demonstrating the durability of injection molded parts. The components, which protect the car from road debris and minimize splashing, are often made from rubber or other durable and flexible materials.
3. Interior
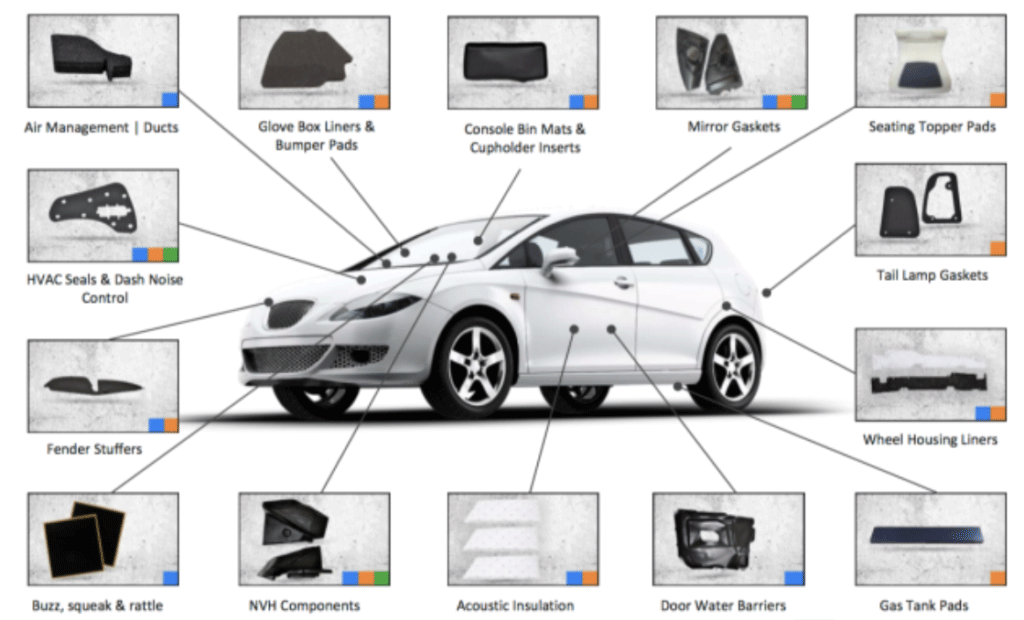
Many automotive interior parts are also produced using injection molding. They include instrumentation components, interior surfaces, dashboard faceplates, door handles, glove compartments, air vents and more. Decorative plastic elements can also be produced using injection molding.
Alternatives to Injection Molding for Low-cost Automotive Prototypes
In many cases, molded plastics serve as an alternative to metals. Items like brackets, trunk lids, seatbelt modules and air-bag containers would once have been made exclusively from metal, but today are regularly injection molded using plastics.
On the other hand, sometimes molded plastic parts can be replaced with 3D printed plastic parts — especially for prototyping where there is less need for extreme durability or a smooth surface finish. Many moldable plastics can also be used as FDM 3D printer filaments or, in the case of nylons, as SLS 3D printer powders. Some specialist and high-temp 3D printers can also print reinforced composites for high-strength parts.
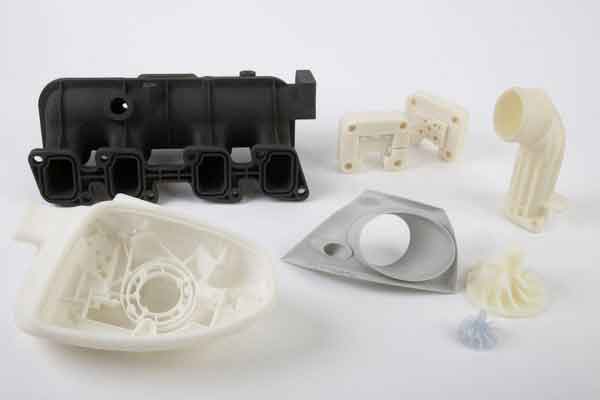
For one-off prototypes, especially non-mechanical parts, 3D printing may offer a cost-effective alternative to molding, since there are no tooling costs involved.
3D printing can even be used for a handful of end-use automotive parts. An automotive plastic injection parts manufacturer may use SLM 3D printing to make fluid handling components like valves (not usually injection molded), or SLS 3D printing to make parts like bumpers, trim and wind breakers, which are sometimes injection molded.
In the not-too-distant future, additive manufacturing may be used for a much wider range of auto parts, from doors and body panels (SLM) to powertrain and drivetrain parts (EBM).
China Medical CNC Machining Inc. Automotive Plastic Injection Molding Services
At China Medical CNC Machining Inc., we offer professional injection molding services, delivering mass produced parts to clients in the automotive and other industries. Our services include thermoplastic injection molding, over molding, insert molding and mold making. In the case of the latter, our experts work with clients to produce high quality molds for prototyping or large production runs.
We also offer a broad range of injection molding materials, including strong, heat resistant and rigid thermoplastics; flexible, fast curing thermoplastics; and durable, high temperature rubber plastics. Our professional finishing services enable our automotive clients to obtain high quality finishes that meet their application requirements.
Injection Molding Materials for Automotive Parts
Vehicles need to be built to rigorous safety standards and must meet several certifications in order to become roadworthy. As such, it is important to choose the right plastic for any plastic injection molding automotive parts.
The following is a non-exhaustive list of common automotive IM plastics, along with the parts they can be used to make.
Acrylonitrile butadiene styrene (ABS)
Widely used for injection molding and 3D printing, the durable plastic ABS is fairly weather-resistant. In cars, it may be used to make items like dashboards and covers.
Polyamide (PA)
Although not resistant to liquids, nylons have good abrasion and chemical resistance. They can be molded into automotive components like bushes and bearings.
Poly(methyl methacrylate) (PMMA)
The transparency of acrylic makes it an excellent (and shatterproof) substitute for glass. An automotive plastic parts manufacturer may use molded PMMA for headlight covers and internal screens (e.g. SatNav or radio).
Polypropylene (PP)
Resistant to water, chemicals and UV light, PP is used for some of the more high-intensity automotive parts, including several exterior components. PP parts include bumpers, cable insulation and battery covers.
Polyurethane (PU)
PU is often found in spongy and flexible items like foam seating. This includes car seating, but auto applications of PU also include seals and gaskets, insulation panels and suspension bushings.
Polyvinyl chloride (PVC)
PVC is the third most popular synthetic plastic polymer in the world, and within the auto industry it is used for many molded parts that require good chemical resistance. These include interior panels, dashboards and cable insulation.
Reinforced composites
Glass or carbon fiber reinforced plastics, much stronger than ordinary resins, can be used in the production of car bodywork and bumpers.
FAQ
A: Different parts demand different plastic materials, but the most widely used plastics are PP (seating, body, under the hood); PU (seating, upholstery); and PVC (seating, interior trim, electrical, upholstery). China Medical CNC Machining Inc. can advise you on a suitable material for your automotive parts.
A: It probably depends on your required quantity. For a hundred parts or so, manufacturers can make rapid tooling for a low-cost run of molded parts. But for just one or two units of a prototype, it might make more sense to use a specialist prototyping technology like additive manufacturing, where there are fewer up-front costs.
A: Injection molding is not used for metals, and the nearest alternative may be the process of metal casting, which manufacturers use to produce aluminum transmission housings and pistons as well as engine blocks and cylinder heads. CNC machining is also widely used in the automotive industry
Q: What is the best material for injection molding automotive parts?
A: Different parts demand different plastic materials, but the most widely used plastics are PP (seating, body, under the hood); PU (seating, upholstery); and PVC (seating, interior trim, electrical, upholstery). China Medical CNC Machining Inc. can advise you on a suitable material for your automotive parts.
Q: Should I use injection molding for automotive prototypes?
A: It probably depends on your required quantity. For a hundred parts or so, manufacturers can make rapid tooling for a low-cost run of molded parts. But for just one or two units of a prototype, it might make more sense to use a specialist prototyping technology like additive manufacturing, where there are fewer up-front costs.
Q: What about metal parts? A: Injection molding is not used for metals, and the nearest alternative may be the process of metal casting, which manufacturers use to produce aluminum transmission housings and pistons as well as engine blocks and cylinder heads. CNC machining is also widely used in the automotive industry
Share on social media...
Get Your Parts Into Production Today
Only 4 simple steps to complete your project. Follow the instruction and give it a try!
Upload Files
Get Quotation
Place an Order
Start Production
Latest news and stories
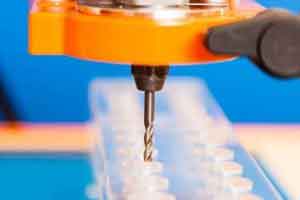
Understanding Plastic Fabrication Processes: A Complete Guide
Plastics are versatile materials with plenty of polymer options. They are among the most common […]
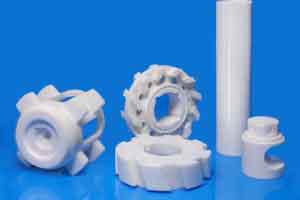
Ceramic CNC Machining: Another Option for Custom Manufacturing
It could be quite a cumbersome task to choose the best material for your manufacturing […]
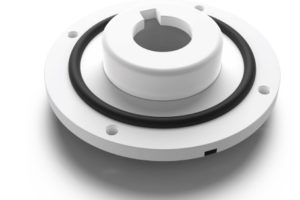
The Overmolding Design Guide You Must Never Forget
Overmolding is an injection molding process where you cast a layer of resin (usually a […]