6 Design Tips to Get the Most out of CNC Machining
Dec 10, 2019
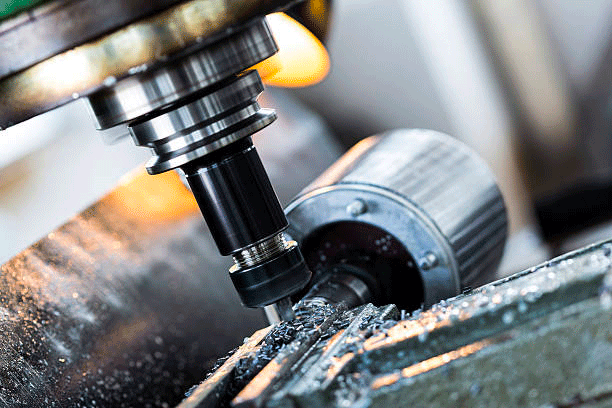
When designing for CNC machining, it is important to play to the technology’s strengths. Here are six design tips for achieving the best CNC machined parts.
Like any manufacturing process, CNC machining comes with its own set of design guidelines and rules. The subtractive manufacturing method, which enables the production of precision parts and products for many industries, has both strengths and weaknesses that are not only important to keep in mind during manufacturing but also during the design process.
Understanding how CNC machining works and understanding both the design opportunities and limitations of CNC machining can actually lead to faster production times and lower costs. Let’s take a look at some of the key design opportunities and limitations associated with CNC machining that will improve the production workflow and, ultimately, the quality of your product.
Design Opportunities for CNC Machining
When designing parts for CNC machining, it is important to play to the technology’s strengths. Thankfully, there are many. CNC machining is widely used across industries—both for in-house production and outsourced rapid prototyping and manufacturing—because of its ability to rapidly fabricate accurate, high-quality parts from a wide variety of metal and plastic materials. Let’s take a look at some of the core design opportunities that product designers should consider and take advantage of when coming up with part designs.
• Precision
CNC machining is capable of some of the highest tolerances of any manufacturing process, making it the ideal production process for parts or products that require precision or extreme accuracy. Though the cost may increase for tighter tolerances, it is still possible to achieve tolerances of (+/-) 100 μm or even (+/-) 50 μm. (At RapidDirect, our standard tolerance for CNC Machining is (+/-) 125 μm.)
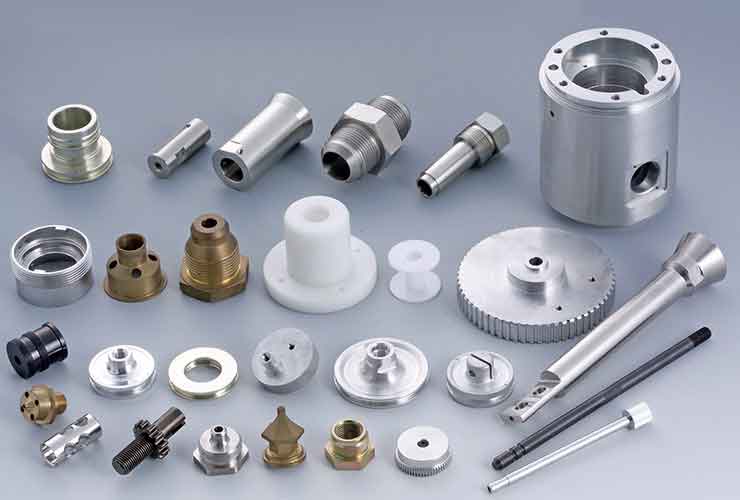
• Repeatability
When designing a part for CNC machining there is no real need to worry about human error on the production end. Because CNC machines are automated and are controlled by advanced computer software, they can achieve high repeatability. This means that you can be guaranteed that your product is fabricated exactly and uniformly—every time. For prototyping this can be especially valuable, as product designers can see exactly what their product will look like and how it will perform.
• Complexity and details
In addition to precision and repeatability, CNC machining also has the key benefit of enabling the fabrication of complex and detailed components. Thanks to advanced CNC machines—including 5-axis CNC milling and turning—a higher degree of design freedom is unlocked. Product designers can also integrate engraved details or text into their part design, which can be executed with extreme precision. It should be noted that more complex or detailed parts may take longer to machine and thus come at a higher cost than standard parts.
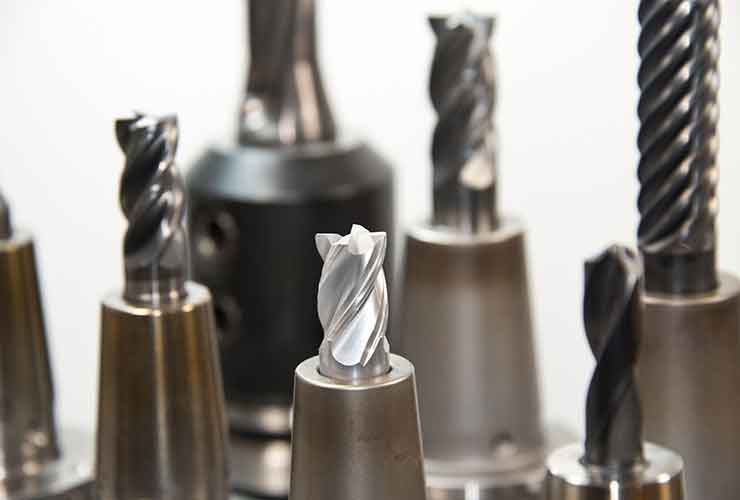
Design Limitations for CNC Machining
Keeping the design opportunities in mind, it is also equally important to remember that CNC machining also has certain limitations. By taking these limitations into consideration throughout the design process, the entire production workflow can be made smoother both for machine operator and customer.
• Wall thickness
One of the key elements that can determine the success of a part is a viable wall thickness. At RapidDirect, we suggest a minimum wall thickness of 1mm for CNC machined parts though 2mm or 2.5mm is preferable for a rigid wall. Essentially, the thinner the thickness of a wall in a given part, the more it becomes susceptible to the vibrations of the CNC machine, which can have a negative effect on part precision. For this reason, it is advisable to design parts with thicker rather than thinner walls.
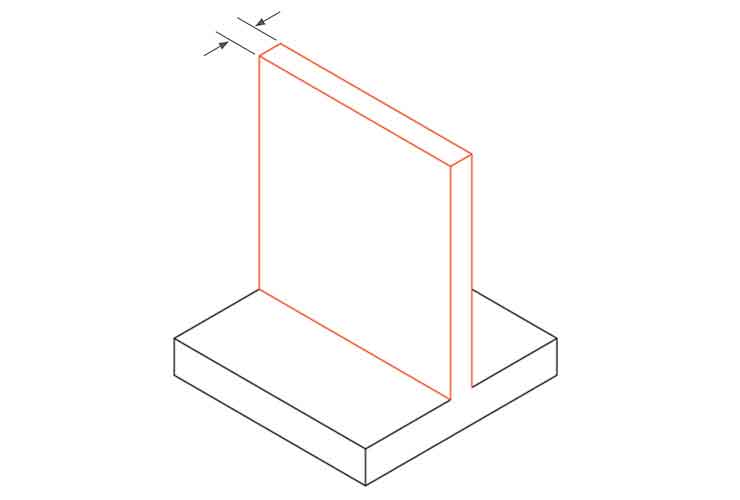
• Internal Radii
Because of the nature of tools used in the CNC machining process, part designs should have rounded corners with a minimum internal radius of 1mm. Rather than design parts with 90-degree internal corners, a rounded internal radius enables the tool to move in a smooth, circular path resulting in a better surface finish. When applicable, the larger the internal radii can be the better, as it allows for more material to be cut away at once, resulting in faster machining times.
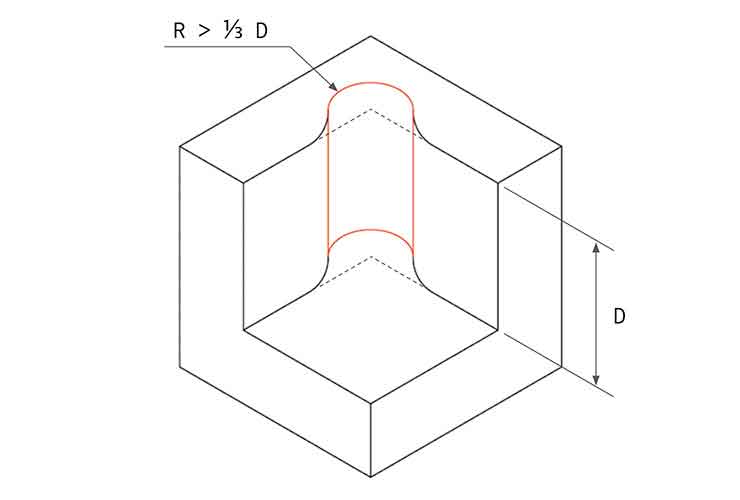
• Cavities and Pockets
When designing a part with features such as cavities or pockets, it is important to consider the tools used by the CNC machine. Typically, end mill tools have a cutting length that is no bigger than 3 or 4 times their diameter. Therefore, to ensure the machinability of your product it is important that cavities and pockets should measure up to 3 times the diameter of the end mill in depth. Sticking to this design tip will not only facilitate the machining of your part but will actually increase the quality of the part because of tool vibrations and deflection decrease with a shallower cavity.
Parts in as little as 3 days
As the largest manufacturing network in China, RapidDirect has the tools and skills necessary to support its clients with the prototyping and production of parts. China Medical CNC Machining Inc.’s skilled machine operators and engineers ensure that product designs are ready for CNC machining. This ensures that your CNC machined prototypes and products can be delivered in record time (as little as three days) while still maintaining the highest quality possible.
Share on social media...
Get Your Parts Into Production Today
Only 4 simple steps to complete your project. Follow the instruction and give it a try!
Upload Files
Get Quotation
Place an Order
Start Production
Latest news and stories
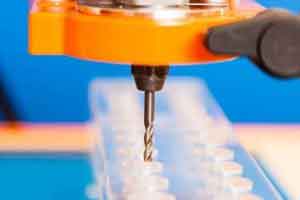
Understanding Plastic Fabrication Processes: A Complete Guide
Plastics are versatile materials with plenty of polymer options. They are among the most common […]
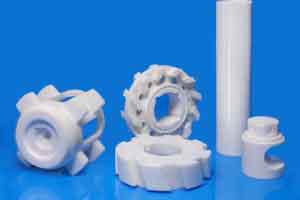
Ceramic CNC Machining: Another Option for Custom Manufacturing
It could be quite a cumbersome task to choose the best material for your manufacturing […]
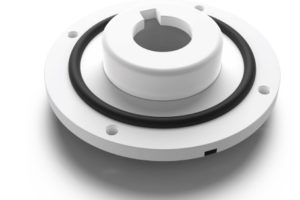
The Overmolding Design Guide You Must Never Forget
Overmolding is an injection molding process where you cast a layer of resin (usually a […]